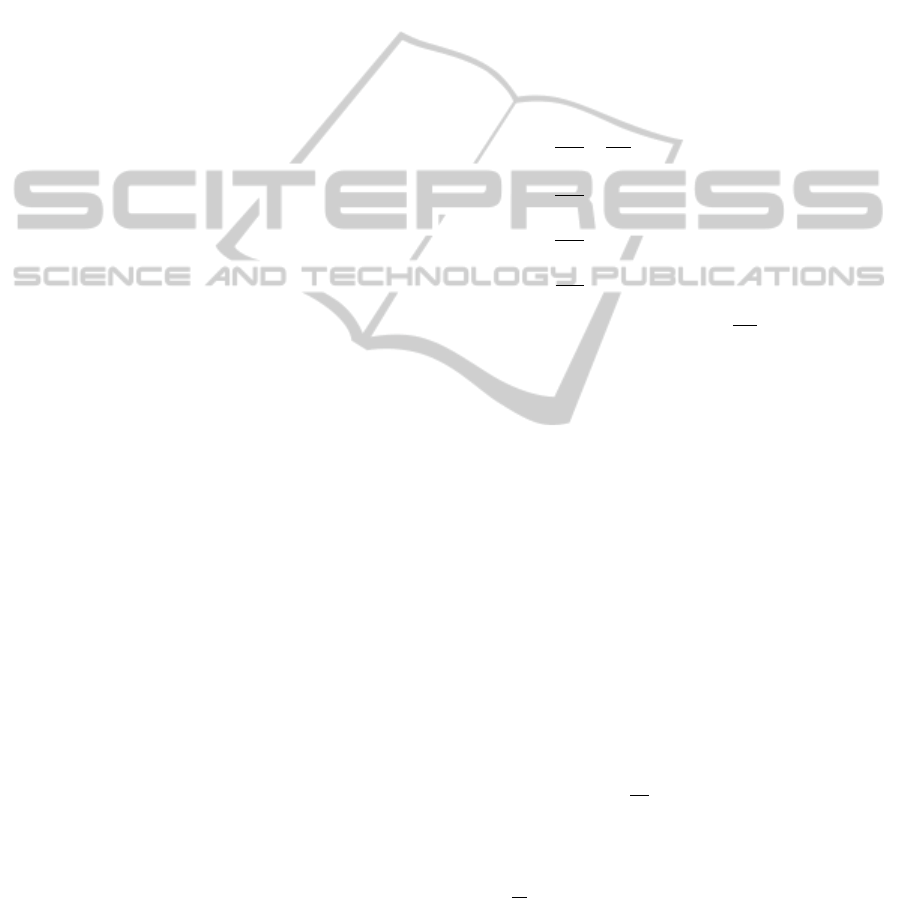
LA-2010-246461 and FP7-ICT-2009-4248940.
REFERENCES
Arellano-Garcia, H., Martini, W., Wendt, M., Li, P., and
Wozny, G. (2003). Chance constrained batch distil-
lation process optimization under uncertainty. In IE
Grossmann, CM McDonald (Eds.): Proc. FOCAPO
2003, pages 609–612.
Ben-Tal, A. and Nemirovski, A. (1999). Robust solutions of
uncertain linear programs. Operations Research Let-
ters, 25(1):1–14.
Blankenship, J. and Falk, J. (1976). Infinitely constrained
optimization problems. Journal of Optimization The-
ory and Applications, 19(2):261–281.
Bock, H. and Plitt, K. (1984). A Multiple Shooting algo-
rithm for direct solution of optimal control problems.
In Proceedings of the 9th IFAC World Congress, pages
243–247. Pergamon Press.
Diehl, M., Bock, H., and Kostina, E. (2006). An approx-
imation technique for robust nonlinear optimization.
Mathematical Programming, 107(1):213–230.
Diehl, M., Gerhard, J., Marquardt, W., and Mnnigmann,
M. (2008). Numerical solution approaches for robust
nonlinear optimal control problems. Computers and
Chemical Engineering, 32(6):1287–1300.
Heine, T., Kawohl, M., and King, R. (2006). Robust model
predictive control using the unscented transformation.
In Control Applications CCA, pages 224–230. Perga-
mon Press.
Hettich, R. and Kortanek, K. O. (1993). Semi-Infinite Pro-
gramming: Theory, Methods, and Applications. SIAM
Review, 35(3):380–429.
Julier, S. and Uhlmann, J. (1996). A general method for ap-
proximating nonlinear transformations of probability
distributions. Dept. of Engineering Science, Univer-
sity of Oxford, Tech. Rep.
Julier, S. and Uhlmann, J. (1997). A new extension of
the Kalman filter to nonlinear systems. In Int. Symp.
Aerospace/Defense Sensing, Simul. and Controls, vol-
ume 3, page 26. Citeseer.
Kuehl, P., Milewska, A., Diehl, M., Molga, E., and Bock,
H. (2005). NMPC for runaway-safe fed-batch reac-
tors. In Proc. Int. Workshop on Assessment and Future
Directions of NMPC, pages 467–474.
Leineweber, D., Bauer, I., Bock, H., and Schlder, J. (2003a).
An efficient multiple shooting based reduced SQP
strategy for large-scale dynamic process optimization.
Part 1: theoretical aspects. Computers and chemical
engineering, 27(2):157–166.
Leineweber, D., Schfer, A., Bock, H., and Schlder, J.
(2003b). An efficient multiple shooting based reduced
SQP strategy for large-scale dynamic process opti-
mization. Part II: Software aspects and applications.
Computers and chemical engineering, 27(2):167 –
174.
Li, P., Arellano-Garcia, H., and Wozny, G. (2008). Chance
constrained programming approach to process opti-
mization under uncertainty. Computers & Chemical
Engineering, 32(1-2):25–45.
Milewska, A. (2006). Modelling of batch and semibatch
chemical reactors - safety aspects. Ph.d. thesis, War-
saw University of Technology.
Moennigmann, M. and Marquardt, W. (2002). Normal vec-
tors on manifolds of critical points for parametric ro-
bustness of equilibrium solutions of ODE systems.
Journal of Nonlinear Science, 12(2):85–112.
APPENDIX
The model of the semibatch process (as used in
(Kuehl et al., 2005)) reads as follows:
dn
A
dt
=
u
M
A
−r ·V (33)
dn
B
dt
= −r ·V (34)
dn
C
dt
=r ·V (35)
(C
p,I
+C
p
) ·
dT
R
dt
=r ·(−∆H
r
) ·V −q
dil
−U ·Ω(T
R
−T
J
)
−α ·(T
R
−T
a
) −
u
M
A
·c
p,A
·(T
R
−T
d
)
(36)
where n
i
denotes the molar amount of components
i = A,B,C,D and V the volume. T
R
,T
J
,T
a
and T
d
stand for the reactor, jacket, ambient and dosing tem-
peratures. The reaction rate is denoted by r, (−∆H
r
)
is the reaction enthalpy and Q
dil
the dilution’s heat.
U is an overall heat transfer coefficient and Ω the
heat exchanger area. The approximated heat capac-
ity of solid inserts (stirrer, baffles) is C
p,I
. C
p
denotes
the approximated heat capacity of the entire reaction
mixture and c
p,i
is the specific molar heat capacity of
component i. As the number of moles of D always
equals the number of moles of C, the equation for D
has been omitted. The molar concentrations c
i
are cal-
culated as c
i
= n
i
/V . The molar dosing rate u of A to
the batch reactor serves as control input. The defining
algebraic equations are:
ρ
i
=M
i
P
i
·Q
1−
T
R
T
c,i
0.2857
i
−1
, i = A,B,C,D
(37)
c
i
=
n
i
V
, i = A,B,C,D,K (38)
c
p,i
=a
i
+ b
i
·T
R
+ c
i
·T
2
R
+ d
i
·T
3
R
, i = A,B,C,D
(39)
c
p
=
∑
i=A,B,C,D
c
p,i
·n
i
(40)
SIMULTECH2012-2ndInternationalConferenceonSimulationandModelingMethodologies,Technologiesand
Applications
206