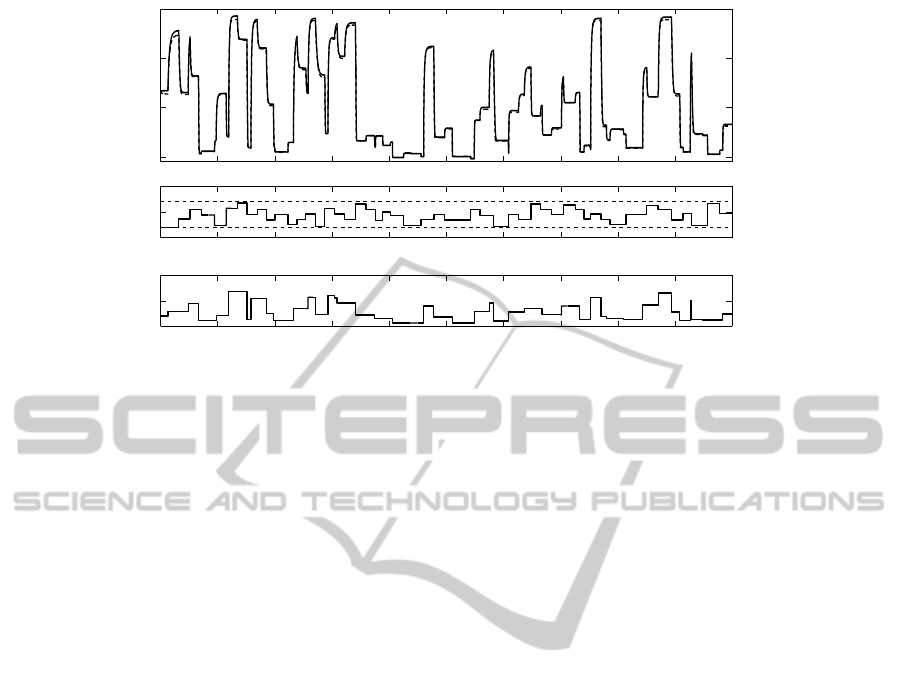
0 10 20 30 40 50 60 70 80 90 100
5
10
15
20
0 10 20 30 40 50 60 70 80 90 100
0
100
200
0 10 20 30 40 50 60 70 80 90 100
0
0.5
1
Output Voltage [V]
Output
Current [mA]
Duty-Cycle
Time [s]
Figure 10: Upper: measured output response of the system (solid line) and output response of the model (dashed line) to
arbitrary varying sequences of the input signal and output current. Middle: arbitrary varying output current sequence (solid
line) in the defined range 40mA ≤ i
R
≤ 140mA (dashed lines). Lower: arbitrary varying input sequence.
be drawn from the converter, which is realised by a
load as shown in Figure 3. Furthermore, the asso-
ciated identification steps make use of polynomials,
so that parameters can be identified straightforwardly
by making use of standard system identification algo-
rithms such as least-squares. Additionally, the tran-
sients are modelled by considering the time constants
in the continuous time domain of the equivalent lin-
ear models at several operating points, which are then
mapped back in the discrete time domain. In this
way, the identification of the transient behaviour is
also modelled in a straightforwardway by making use
of linear relationships. The resulting state dependent
parameter model is able to deal with varying loads by
taking the output current into account. Finally, the
state dependent parameter model has been validated
via a laboratory based experiment confirming its ac-
curacy and appropriateness.
REFERENCES
Erickson, R. W. and Maksimovic, M. (2001). Fundamen-
tals of Power Electronics. Kluwer Academics/Plenum
Publishers, New York, 2nd edition.
Hitzemann, U. and Burnham, K. J. (2011). State depen-
dent parameter modelling and control of a dc-dc boost
converter in discontinuous conduction mode. In Pro-
ceedings of the 9th European Workshop on Advanced
Control and Diagnosis, ACD 2011, Budapest, Hun-
gary.
Hsia, T. C. (1977). System Identification: Least-Squares
Methods. Lexington Books, Massachusetts.
Kontoroupis, P., Young, P. C., Chotai, A., and Taylor, C. J.
(2003). State dependent parameter-proportional inte-
gral plus (sdp-pip) control of nonlinear systems. Proc.
16th Int. Conf. on Systems Engineering, ICSE’2003,
pages 373–378.
Middlebrook, R. D. and Cuk, S. (1976). A general uni-
fied approach to modelling switching-converter power
stages. In IEEE Proceedings of Power Electronics
Specialists Conference, pages 18–34.
Sun, J., Mitchell, D. M., Greuel, M. F., Krein, P. T., and
Bass, R. M. (2001). Averaged modeling of pwm con-
verters operating in discontinuous conduction mode.
IEEE Transaction on Power Electronics, 16(4):482–
492.
Taylor, C. J., Chotai, A., and Young, P. C. (2009). Non-
linear control by input-output state variable feedback
pole assignment. International Journal of Control,
82(6):1029–1044.
Taylor, C. J., Shaban, E. M., Stables, M. A., and Ako,
S. (2007). Proportional-integral-plus control appli-
cations of state-dependent parameter models. Proc.
IMechE Part I: Journal of Systems and Control Engi-
neering, 221(7):1019–1032.
Wang, C. L. and Young, P. C. (1988). Direct digital and
adaptive control by input-output state variable feed-
back pole assignment. International Journal of Con-
trol, 47(1):97–109.
Xie, G., Fang, H., and Cheng, X. (2010). Non-ideal models
and simulation of boost converters operating in dcm.
International Journal of Computer and Electrical En-
gineering, 2(4):730–733.
Young, P. C. (2000). Nonlinear and Nonstationary Signal
Processing, chapter Stochastic, dynamic modelling
and signal processing: time variable and state depen-
dent parameter estimation., pages 74–114. Cambridge
University Press, Cambridge.
Young, P. C., Behzadi, M. A., Wang, C. L., and Chotai, A.
(1987). Direct digital and adaptive control by input-
output state variable feedback pole assignment. Inter-
national Journal of Control, 46(6):1867–1881.
StateDependentParameterModellingofaDC-DCBoostConverterinDiscontinuousConductionMode
487