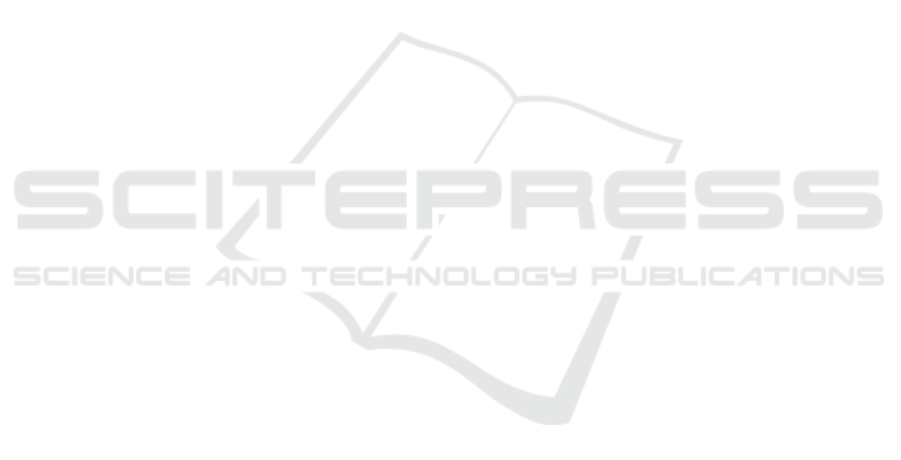
Development of Parallel Two-wheel Vehicle with Lower Gravity Center
of Vehicle Body
Yoshiyuki Noda
1
, Yukinori Sago
2
, Kazuhiko Terashima
2
, Kiyoaki Kakihara
3
and
Hirotoshi Kawamura
4
1
Department of Mechanical Engineering, University of Yamanashi, 4-3-11, Takeda, Kofu, 400-8511, Japan
2
Department of Mechanical Engineering, Toyohashi University of Tech.,
1-1, Hibarigaoka, Tempaku, Toyohashi, 441-8580, Japan
3
KER Co., Ltd., 215, Toyogaoka, Toyokawa, 442-0808, Japan
4
Sinfonia Technology Co., Ltd., 150, Motoyashiki, Mitsuya, Toyohashi, 441-3195, Japan
Keywords:
Parallel Two-wheel Vehicle, Lower Gravity Center, Sway Suppression Control of Vehicle Body, Active Mass
Damper, Backstepping Control.
Abstract:
This paper presents an advanced parallel two-wheel vehicle which has lower gravity center of vehicle body.
The gravity center is assigned at the lower position than the wheel axis. Therefore, the vehicle has a structure
of the pendulum, and enables the vehicle body with the passenger to always keep the stable posture, even if
the vehicle is in the power-off or control-off condition. And, 2-DOF joystick which has operation with back-
and-forth direction and rotation is applied to the proposed vehicle. The elderly or handicapped passenger
can operate easily the vehicle by this joystick. Moreover, in order to suppress the sway of the vehicle body
as a pitching oscillation while driving the vehicle, the sway suppression control system with an active mass
damper system is proposed in this paper. The control system is designed by a backstepping method. The
effectiveness of the proposed sway suppression control system with the active mass damper system is verified
by the experiments using the proposed parallel two-wheel vehicle with lower gravity center.
1 INTRODUCTION
In recent years, barrier-free society is advancing, and
welfare environment has been gradually improved.
There have been many studies about an electric
wheelchair as welfare device for elderly and people
with lower physical ability. And the demand for the
electric wheelchair will be increased in the future.
In addition, many researches and developments have
also focused on personal vehicle with low energy re-
quirement, which is required to support for short-
distance transport, (Hun-ok Lim and Tamai, 2008),
(Y. Ueno and Kitagawa, 2009) and (Y. Noda and
Terashima, 2010).
The typical electric wheelchair is drivenwith four-
wheel which is composed of the front casters and the
rear wheels. However since these wheelchairs have
the large turning radius, it is difficult to pass through
in a narrow passage. A parallel two-wheel vehicle
with structure of inverted pendulum, which has small
turning radius, has been developed in recent years,
(M. Sasaki, 2005). In such vehicle, an inverted pen-
dulum control system is used for standing the vehicle
stably by only using the two driving parallel wheels,
(C. Nakagawa and Hirayama, 2011) and (Karkoub
and Parent, 2004). Therefore, the gravity center of
the vehicle body is higher than the wheel axis, and
the vehicle is moved by tilting the vehicle body for-
ward or backward by moving the gravity center. How-
ever, when the vehicle is in the power-off or control-
off conditions which are caused by a breakdownin the
vehicle, the vehicle cannot keep the standing posture.
Moreover, we consider the vehicle with the passen-
ger sitting which can be used by elderly and handi-
capped people. In this case, since the gravity center
is lower than the standing posture, the larger action of
the passenger’s upper body is required for operating
the vehicle. The elderly or handicapped passenger is
difficult to the large action in the vehicle.
Therefore, we propose a parallel two-wheel vehi-
cle with safety and easy operation which can be used
by elderly and handicapped people. The proposed ve-
hicle has the lower gravity center of the vehicle body
as shown in Figure 1. The position of the gravity cen-
70
Noda Y., Sago Y., Terashima K., Kakihara K. and Kawamura H..
Development of Parallel Two-wheel Vehicle with Lower Gravity Center of Vehicle Body.
DOI: 10.5220/0004036400700076
In Proceedings of the 9th International Conference on Informatics in Control, Automation and Robotics (ICINCO-2012), pages 70-76
ISBN: 978-989-8565-22-8
Copyright
c
2012 SCITEPRESS (Science and Technology Publications, Lda.)