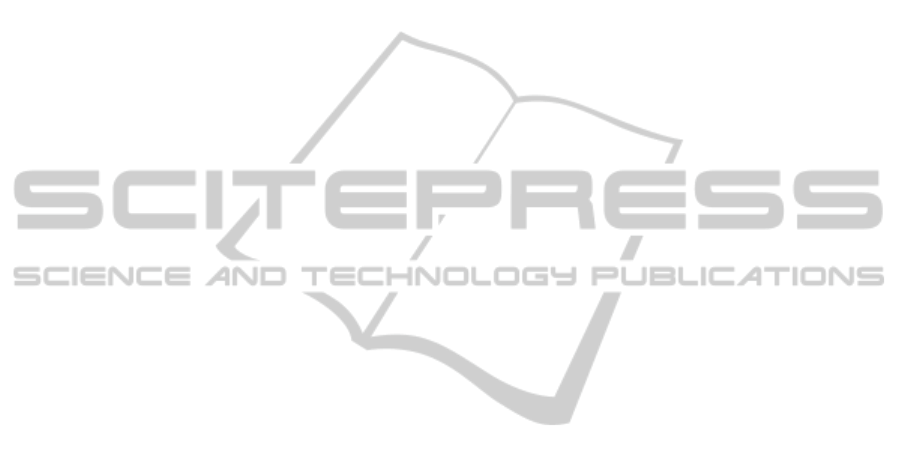
In the same time from Figures 7-11 it can be
seen, that the increase of operating temperature has
positive effect on repeatability of the piezoresistive
effect during cyclic loading. The noticeable decrease
of the initial electrical resistivity at the start of each
loading cycle is observed only for operating
temperatures of 55 °C and below as the initial
resistivity for repeated cycles shifts lower. If the
operating temperature was at least 70 °C or higher,
only negligible drift of initial resistivity was
observed. Thus it can be seen, that LHPS performs
considerably better at elevated temperatures which
can be attributed to better mobility of filler particles
allowing the more rapid mechanical modification
and sequencial recombination of electroconductive
network of HSCB particles to occur.
4 CONCLUSIONS
The observed positive thermal coefficient of
resistivity (PTC) for PNCBC with 8 p.h.r. of HSCB
could be explained with large difference in thermal
expansion coefficients for both: polymer matrix and
HSCB filler causing the sufficient broadening of
tunnel junctions with subsequent exponential rise of
electrical resistivity versus temperature.
Behaviour of LHPS at evaluated operating
temperatures has been successfully investigated.
It has been found out that the sensitivity of
LHPS enhances gradually with the increase of
operating temperature. The increase of the operating
temperature improves the repeatability of the
piezoresistive cycles due to greater mobility of
particles of electroconductive filler and better partial
destruction/recombination of electroconductive
structure in the PNCBC.
ACKNOWLEDGEMENTS
The research was supported by Ministry of
Education and Science of the Republic of Latvia.
REFERENCES
Zavickis, J., Knite, M., Podins, G., Linarts, A., Orlovs, R.,
2011. Polyisoprene-nanostructured carbon composite
– A soft alternative for pressure sensor application.
Sensors and Actuators A: Physical. V171, 38-42
Knite, M., Zavickis, J., Podins, G., Orlovs, R., Ozols, K.,
2009. Prospective Elasto-plastic Pressure Sensors: All-
elasto-plastic polyisoprene/ nanostructured carbon
pressure sensing element. In Proceedings of 6th
International Conference on informatics in Control,
Automation and Robotics. 409-412
Knite, M., Podins, G., Zike, S., Zavickis, J., Tupureina, V.,
2008. Elastomer – carbon nanostructure composites as
prospective materials for flexible robotic tactile sensors.
In Proc. of 5th International Conference on Informatics
in Control, Automation and Robotic. 234-238
Huang, Y., Lu, W., Zhao, X., Lian, C., Ge, Y., 2011.
Design and experiment of flexible multi-functional
tactile sensors for robot skin. Jiqiren/Robot. V 33,
347-353
Chang, F.-Y., Wang, R.-H., Lin, Y.-H., Chen, T.-M.,
Lee, Y.-F., Huang, S.-J., Liu, C.-M., 2011. Flexible
sensing arrays fabricated with carbon nanofiber
composite thin films for posture monitoring. Japanese
Journal of Applied Physics. V 50, N 6-2, 06GE081-
06GE084
Knite, M., Klemenok, I., Sakale, G., Teteris, V., Zicans, J.,
2007. Polyisoprene-carbon nano-composites for
application in multifunctional sensors. Journal of
Alloys and Compounds. V 434-435, 850-853
Knite, M., Teteris, V., Kiploka, A., Klemenoks, I., 2004.
Reversible tenso-resistance and piezo-rezistance
effects in conductive polymer-carbon nanocomposites.
Advanced Engineering Materials. V 6, 742-746
Balberg, I., 2002. A comprehensive picture of the
electrical phenomena in carbon black–polymer
composites. Carbon. V 40, 139-143
Balberg, I., Azulay, D., Toker, D., Millo, O., 2004.
Percolation and tunnelling in composite materials.
International Journal of Modern Physics B. V 18,
2091-2121
ICINCO2012-9thInternationalConferenceonInformaticsinControl,AutomationandRobotics
498