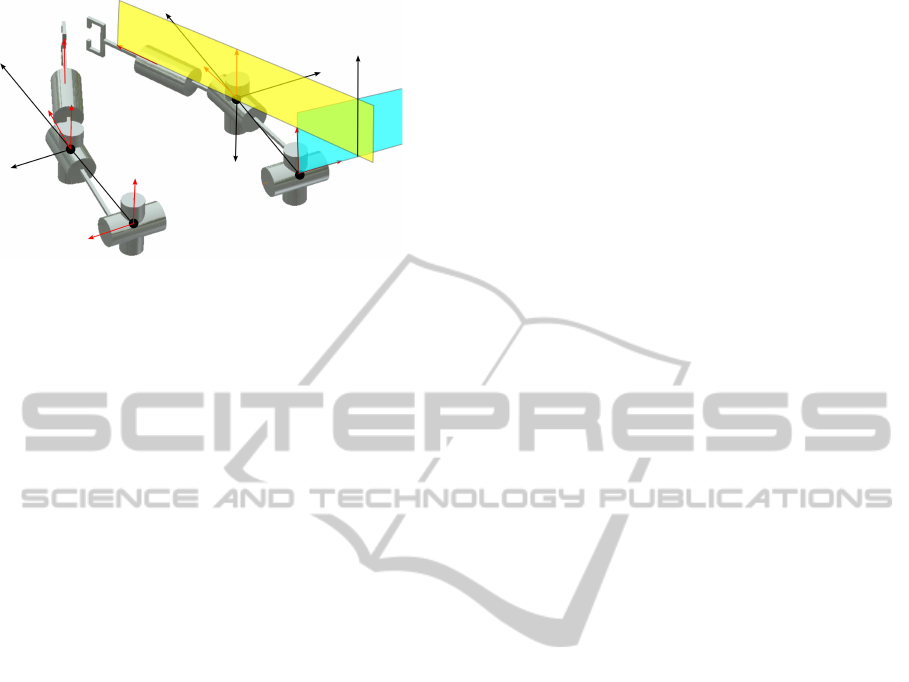
s
2
s
1
s
4
s
3
s
5
s
6
s
7
s
8
s
9
s
10
Π
45
Π
12
ζ
01
ζ
02
ζ
a
01
k s
2
ζ
a
02
k s
1
ζ
a
03
ζ
a
07
k s
6
A
B
Figure 6: Admissible actuation scheme.
more interesting is the presence of constraint singu-
larities. The issue of actuation singularities, present
due to dependent joint variables, was investigated.
By considering the wrenches exerted by the actuators,
both an admissible and inadmissible actuation scheme
were shown.
REFERENCES
Amine, S., Caro, S., Wenger, P., and Kanaan, D.
(2011). Singularity analysis of the H4 robot using
Grassmann–Cayley algebra. Robotica, 1(1):1–10.
Amine, S., Tale Masouleh, M., Caro, S., Wenger, P., and
Gosselin, C. (2012). Singularity analysis of 3T2R
parallel mechanisms using Grassmann–Cayley alge-
bra and Grassmann geometry. Mechanism and Ma-
chine Theory.
Ball, S. R. (1900). A Treatiseon the Theory of Screws. Cam-
bridge Univ Pr.
Bicchi, A., Melchiorri, C., and Balluchi, D. (1995). On the
mobility and manipulability of general multiple limb
robots. Robotics and Automation, IEEE Transactions
on, 11(2):215–228.
Caccavale, F., Chiacchio, P., and Chiaverini, S. (2000).
Task-space regulation of cooperative manipulators.
Automatica, 36(6):879–887.
Caccavale, F., Chiacchio, P., Marino, A., and Villani, L.
(2008). Six-DOF impedance control of dual-arm co-
operative manipulators. Mechatronics, IEEE/ASME
Transactions on, 13(5):576–586.
Cheng, H., Yiu, Y.-k., Member, S., and Li, Z. (2003). Dy-
namics and control of redundantly actuated parallel
manipulators. IEEE/ASME Transactions on Mecha-
tronics, 8(4):483–491.
Chiacchio, P., Chiaverini, S., and Siciliano, B. (1996). Di-
rect and inverse kinematics for coordinated motion
tasks of a two-manipulator system. Journal of Dy-
namic Systems, Measurement, and Control, 118:691.
Gogu, G. (2007). Structural Synthesis of Parallel Robots:
Part 1: Methodology. Springer Verlag.
Hunt, K. (1978). Kinematic geometry of mechanisms. Cam-
bridge Univ Press.
Khalil, W. and Kleinfinger, J. (1986). A new geometric no-
tation for open and closed-loop robots. In Robotics
and Automation. Proceedings. 1986 IEEE Interna-
tional Conference on, volume 3, pages 1174–1179.
IEEE.
Liu, Y., Xu, Y., and Bergerman, M. (1999). Cooper-
ation control of multiple manipulators with passive
joints. IEEE Transactions on Robotics and Automa-
tion, 15(2):258–267.
¨
Ozkan, B. and
¨
Ozg¨oren, M. (2001). Invalid joint ar-
rangements and actuator related singular configura-
tions of a system of two cooperating scara manipu-
lators. Mechatronics, 11(4):491–507.
Sadati, N. and Ghaffarkhah, A. (2008). Decentral-
ized impedance control of nonredundant multi-
manipulator systems. In Networking, Sensing and
Control, 2008. ICNSC 2008. IEEE International Con-
ference on, pages 206–211.
Uchiyama, M. and Dauchez, P. (1988). A symmetric hybrid
position/force control scheme for the coordination of
two robots. In 1988 IEEE International Conference
on Robotics and Automation, Philadelphia, PA, pages
350–356.
Yeo, H.-J., Suh, I. H., Yi, B.-J., and Oh, S.-R. (1999). A sin-
gle closed-loop kinematic chain approach for a hybrid
control of two cooperating arms with a passive joint:
an application to sawing task. IEEE Transactions on
Robotics and Automation, 15(1):141–151.
Zielinski, C. and Szynkiewicz, W. (1996). Control of two
5 dof robots manipulating a rigid object. In Industrial
Electronics, 1996. ISIE’96., Proceedings of the IEEE
International Symposium on, volume 2, pages 979–
984. IEEE.
Zlatanov, D., Bonev, I., and Gosselin, C. (2002). Constraint
singularities of parallel mechanisms. In Robotics and
Automation, 2002. Proceedings. ICRA’02. IEEE In-
ternational Conference on, volume 1, pages 496–502.
IEEE.
KinematicAnalysisofLowerMobilityCooperativeArmsbyScrewTheory
285