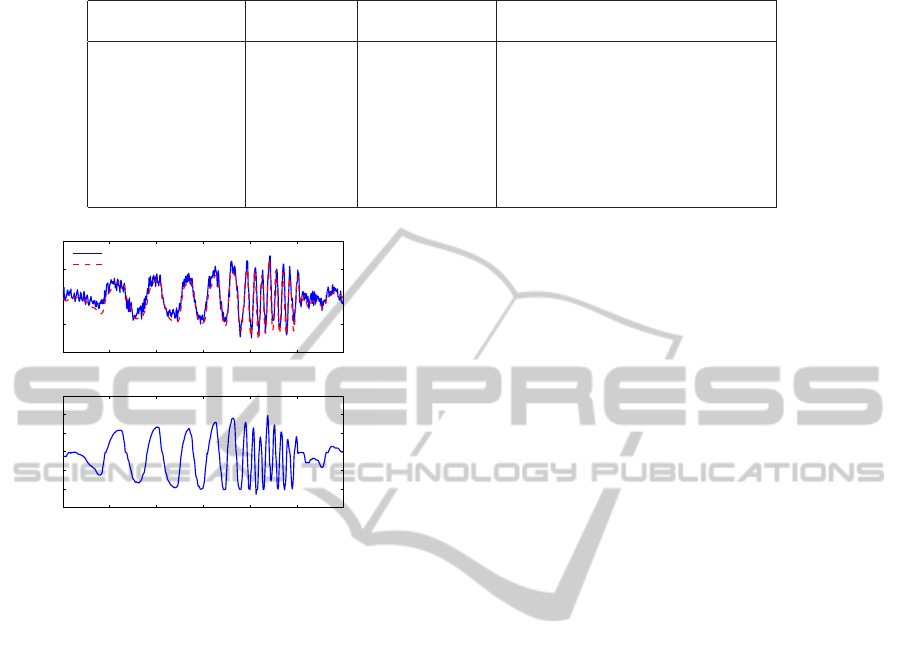
Table 1: Parameters identified from CIFER.
Parameter
Cramer-Rao
Insensitivity(%) Physical meaning
Percent(%)
L
b
= 675.8s
−2
7.171 2.433 Lateral rotor spring derivative
M
a
= 794.7s
−2
7.525 2.589 Longitudinal rotor spring derivative
τ = 0.068s 9.301 3.537 Equivalent flapping time constant
A
′
lon
= 0.898rad/s 4.152 1.962 Longitudinal control derivative
B
′
lat
= 1.069rad/s 4.157 1.935 Lateral control derivative
τ
lat
= 0.03355s 12.08 4.477 Lateral control delay
τ
lon
= 0.03390s 12.17 4.440 Longitudinal control delay
K
β
= 11.5029Nm NA NA Rotor spring constant
0 2 4 6 8 10 12
−2
−1
0
1
2
q (rad/s)
Experiment
Simulation
0 2 4 6 8 10 12
−1.5
−1
−0.5
0
0.5
1
1.5
Time(s)
δ
lon
Figure 7: Time domain verification of longitudinal input to
pitch angular rate.
regarding the development and modeling of a coaxial
UAV platform. For platform construction, the payload
capability of the bare coaxial helicopter is guaranteed
by careful selection of the key components such as
motor, blade and ESC. The onboard avionic system
is designed and assembled onto the helicopter frame
using mechanical dampers. For modeling of the heli-
copter, the model structure of the platform has been
laid out. The coaxial rotor thrust has been empir-
ically derived. More importantly, the roll-pitch dy-
namics of the helicopter are formulated. Through fre-
quency domain identification in CIFER, the equiva-
lent flapping time constant and spring constant are
fine-tuned. Time domain verification using a new set
of test data has validated the fidelity of the identi-
fied roll-pitch dynamics. Future research work will
focus on the modeling of heave dynamics and yaw
dynamics which will produce a complete model. Ad-
ditional effort will be made to study the coaxial rotor
wake structure so that an optimal coaxial configura-
tion could be achieved.
ACKNOWLEDGEMENTS
The authors would like to thank Dr. Feng Lin and Dr.
Guowei Cai from NUS Temasek Laboratories for the
constructive discussion and genuine help. We would
also like to thank ‘Temasek Defence Systems Insti-
tute’ for funding the project.
REFERENCES
Cai, G., Chen, B. M., and Lee, T. H. (2011). Unmanned
Rotorcraft Systems. Springer, London.
Cai, G., Chen, B. M., Lee, T. H., and Lum, K.-Y. (2012).
Comprehensive nonlinear modeling of a miniature un-
manned helicopter. Journal of the American Heli-
copter Society, 57(1):1–13.
Coleman, C. P. (1997). A survey of theoretical and experi-
mental coaxial rotor aerodynamic research. Technical
report, NASA Ames Research Center.
Fankhauser, P., Bouabdallah, S., Leutenegger, S., and Sieg-
wart, R. (2011). Modeling and decoupling control of
the coax micro helicopter. In Proc. of the IEEE/RSJ
International Conference on Intelligent Robots and
Systems (IROS).
Kim, H. and Brown, R. (2006). Coaxial rotor performance
and wake dynamics in steady and manoeuvring flight.
In American Helicopter Society 62nd Annual Forum
Proceedings, volume 62, page 20.
Kim, H. and Brown, R. (2008). Modelling the aerodynam-
ics of coaxial helicopters–from an isolated rotor to a
complete aircraft. In Proceedings of the EU-Korea
Conference on Science and Technology, pages 45–59.
Lim, J. W., McAlister, K. W., and Johnson, W. (2009).
Hover performance correlation for full-scale and
model-scale coaxial rotors. Journal of the American
Helicopter Society.
Mettler, B. (2002). Identification Modeling and Charac-
teristics of Miniature Rotorcraft. Kluwer Academic
Publisher, Nowell, MA.
Mettler, B., Tischler, M. B., and Kanade, T. (1999). System
identification of small-size unmanned helicopter dy-
namics. In American Helicopter Society 55th Annual
Forum Proceedings, volume 2, pages 1706–1717.
Schafroth, D., Bermes, C., Bouabdallah, S., and Siegwart,
R. (2010). Modeling and system identification of
the mufly micro helicopter. Journal of intelligent &
robotic systems, 57(1):27–47.
Tischler, M. and Remple, R. (2006). Aircraft and rotor-
craft system identification: Engineering Methods with
Flight Test Examples. AIAA.
ConstructionandModelingofaVariableCollectivePitchCoaxialUAV
291