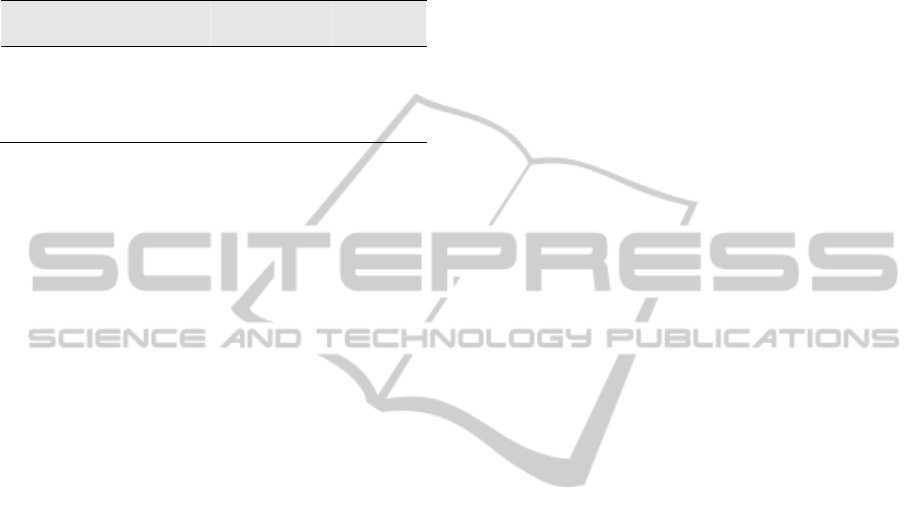
0.058 mm to 0.00014 mm (99.8%). Maximum
defilation in the machining profile has been reduced
from 0.063 mm to 0.0047 mm (92.6%). Low frequency
remained the same for both cases.
Table 2: Milling trajectory accuracy before and after com-
pliance error compensation.
Performance measure
Original
trajectory
Modified
trajectory
Low frequency,[ Hz] 6.70 6.70
Static deviation y
s
, [mm] 58.1e-3 0.14e-3
Max deviation y
MAX
,
[mm]
63.2e-3 4.70e-3
Hence, obtained results show that the developed com-
pliance error compensation allows us significantly
increase the accuracy of the robotic-based machining.
7 CONCLUSIONS
In robotic-based machining, an interaction between
the workpiece and technological tool causes essential
deflections that significantly decrease the manufactur-
ing accuracy. Relevant compliance errors highly de-
pend on the manipulator configuration and essentially
differ throughout the workspace. Their influence is
especially important for heavy serial robots. To over-
come this difficulty this paper presents a new tech-
nique for compensation of the compliance errors
caused by technological process. In contrast to previ-
ous works, this technique is based on the non-linear
stiffness model and the reduced elasto-dynamic model
of the robotic based milling process.
The advantages and practical significance of the
proposed approach are illustrated by milling with of
KUKA KR270. It is shown that after error compensa-
tion technique significantly increase the accuracy of
milling. In future the proposed technique will be inte-
grated in a software toolbox.
ACKNOWLEDGEMENTS
The authors would like to acknowledge the financial
support of the ANR, France (Project ANR-2010-
SEGI-003-02-COROUSSO) and the Region “Pays de
la Loire”, France.
REFERENCES
Alici G., Shirinzadeh B., 2005. Enhanced stiffness model
ing, identification and characterization for robot manip-
ulators. Proceedings of IEEE Transactions on Robotics,
vol. 21, pp. 554–564.
Altintas Y., 2000. Manufacturing automation, metal cutting
mechanics, machine tool vibrations and CNC design.
Cambridge University Press, New York.
Brissaud D., Gouskov A., Paris H., Tichkiewitch S., 2008.
The Fractional Model for the Determination of the Cut-
ting Forces. Asian Int. J. of Science and Technology -
Production and Manufacturing, vol. 1, pp.17-25.
Briot S., Pashkevich A., Chablat D. Reduced elastodynamic
modelling of parallel robots for the computation of their
natural frequencies. 13th World Congress in Mechanism
and Machine Science, 19 - 25 Juin, 2011, Guanajuato,
Mexico.
Chen S., Kao I., 2000. Conservative Congruence Transfor-
mation for Joint and Cartesian Stiffness Matrices of Ro-
botic Hands and Fingers. The International Journal of
Robotics Research, vol. 19(9), pp. 835–847.
Dépincé P., Hascoët J-Y., 2006. Active integration of tool
deflection effects in end milling. Part 2. Compensation
of tool deflection, International Journal of Machine
Tools and Manufacture, vol. 46, pp. 945-956
Dumas C., Caro S., Garnier S., Furet B., 2011. Joint stiff-
ness identification of six-revolute industrial serial ro-
bots, Robotics and Computer-Integrated Manufactur-
ing, vol. 27(4), pp. 881-888.
Eastwood S. J., Webb P., 2010. A gravitational deflection
compensation strategy for HPKMs, Robotics and Com-
puter-Integrated Manufacturing, vol. 26 pp. 694–702
Gong, C., Yuan J., Ni, J., 2000. Nongeometric error identi-
fication and compensation for robotic system by inverse
calibration. International Journal of Machine Tools &
Manufacture, vol. 40(14) pp. 2119–2137.
Kövecses J., Angeles J., 2007. The stiffness matrix in elas-
tically articulated rigid-body systems. Multibody System
Dynamics. vol. 18(2), pp. 169–184.
Laporte S., K’nevez J.-Y., Cahuc O., Darnis P., 2009. Phe-
nomenological model for drilling operation. Int. J. of
Advanced Manufacturing Technology, vol.40, pp.1-11.
Merchant M. E., 1945. Mechanics of metal cutting process.
I-Orthogonal cutting and type 2 chip. Journal of Applied
Physics, vol.16(5), pp.267–275.
Pashkevich A., Klimchik A., Chablat D., 2011. Enhanced
stiffness modeling of manipulators with passive joints.
Mech. and Machine Theory, vol. 46(5), pp. 662-679.
Ritou M., Garnier S., Furet B., Hascoet J.Y., 2006. A new
versatile in-process monitoring system for milling, Int.
J. of Machine Tools & Manufacture, 46/15:2026-2035.
Tlusty J., Ismail F., 1981, Basic non-linearity in machining
chatter. Annals of CIRP, Vol.30/1, pp.299-304.
Tyapin I., Hovland G., 2009. Kinematic and elastostatic de-
sign optimization of the 3-DOF Gantry-Tau parallel
kinamatic manipulator. Modelling, Identification and
Control, vol. 30(2), pp. 39-56
Su H.-J., McCarthy J. M., 2006. A Polynomial Homotopy
Formulation of the Inverse Static Analyses of Planar
Compliant Mechanisms. Journal of Mechanical Design
,
vol. 128(4), pp. 776-786.
ICINCO2012-9thInternationalConferenceonInformaticsinControl,AutomationandRobotics
122