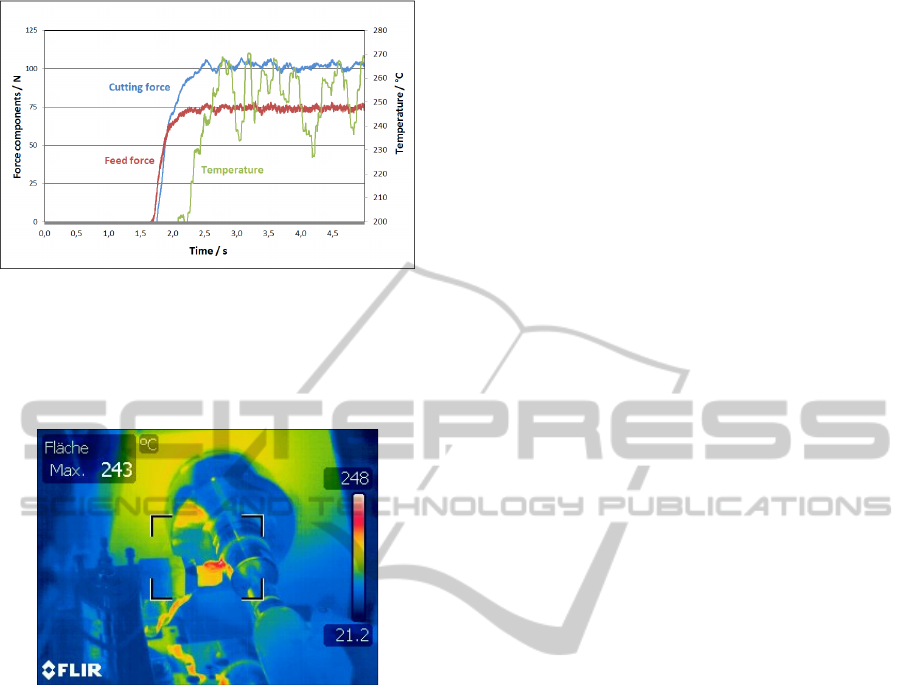
Figure 6: Cutting force, feed force and temperature,
straight turning of titanium alloy with carbide inserts.
Infrared camera pictures and videos have been
shot to validate the temperature results and to get an
impression of the whole thermal field (Fig. 7).
Figure 7: Infrared picture of titanium machining.
It should be pointed out that satisfying
correlation between the thermal radiation result (see
Fig. 6) and the infrared method could be achieved
(maximum temperature of about 250°C).
4.2 Simulation
Optimization of chipping processes based on
measurements should be extended to simulation. The
target of this project (Blaha, 2010) is the FEM
simulation of turning operations for three materials
(C45, X2CrNiMo17-13-2 and Ti6Al4V).
As the most important simulation assessment criteria
cutting forces have to be analysed and compared
with measurements mentioned above.
The required tribologically parameters have to be
determined by special tests (Horwatitsch, 2007). The
comparison of measurement versus simulation has
shown a satisfying compliance in the case of
numerical integration of the local cutting forces
along the comma-shaped chip (Blaha, 2010).
Depending on the material the deviation varies
between 2 and 12 percent considering the cutting
force results.
5 CONCLUSIONS
The triangle relationship between workpiece, cutting
tool and machine tool finally determines the
economic production and always requires new
solutions for each particular case, which can only be
found as a result of chipping tests and process
monitoring.
The paper presents a measuring device for
laboratory purposes as well as a mechatronic tool for
industrial production. The idea of the laboratory
device is to pick up all necessary process data for
optimization purposes. In the case of the
mechatronic product low cost and robust design are
of higher importance. This principle is not limited to
specific manufacturing techniques, it is generally
applicable and represents a significant module to
fulfil the targets of intelligent production.
REFERENCES
Audy J., 2006. An appraisal of techniques and equipment
for cutting force measurement, In Journal of Zhejiang
University, p. 1781-1789.
Blaha, J., Horwatitsch, D., (et al.), (2010). Endbericht
F&E Headquarter Strategy, TCM International Tool
Consulting & Management GmbH, p. 7-28.
Haas, F., Nuspl, E., 2011. Präzises, schnelles Messgerät
für mobiles Condition Monitoring von Zerspa
nungsprozessen, In AALE 2011, p. 161-169.
Horwatitsch, D. (et al.), (2007). Ermittlung der Reibung
zur Verwendung in einer FE-basierten Prozess-
simulation eines Zerspanungsprozesses, In
Proceedings ÖTG Symposium 2007, p. 45-52.
Kistler (Ed.), 2009. Präzise Messsysteme für die
spanabhebende Fertigung, p. 7-9.
Tani, Y., Hatamura, Y., Nagao, T., (1983). Development
of Small Three-component Dynamometer for Cutting
Force Measurement, p. 657-658.
OptimizedChippingProcesseswithaNewMechatronicToolSystem-ApplicationofStrainGaugeSensorsand
PiezoelectricActuators
617