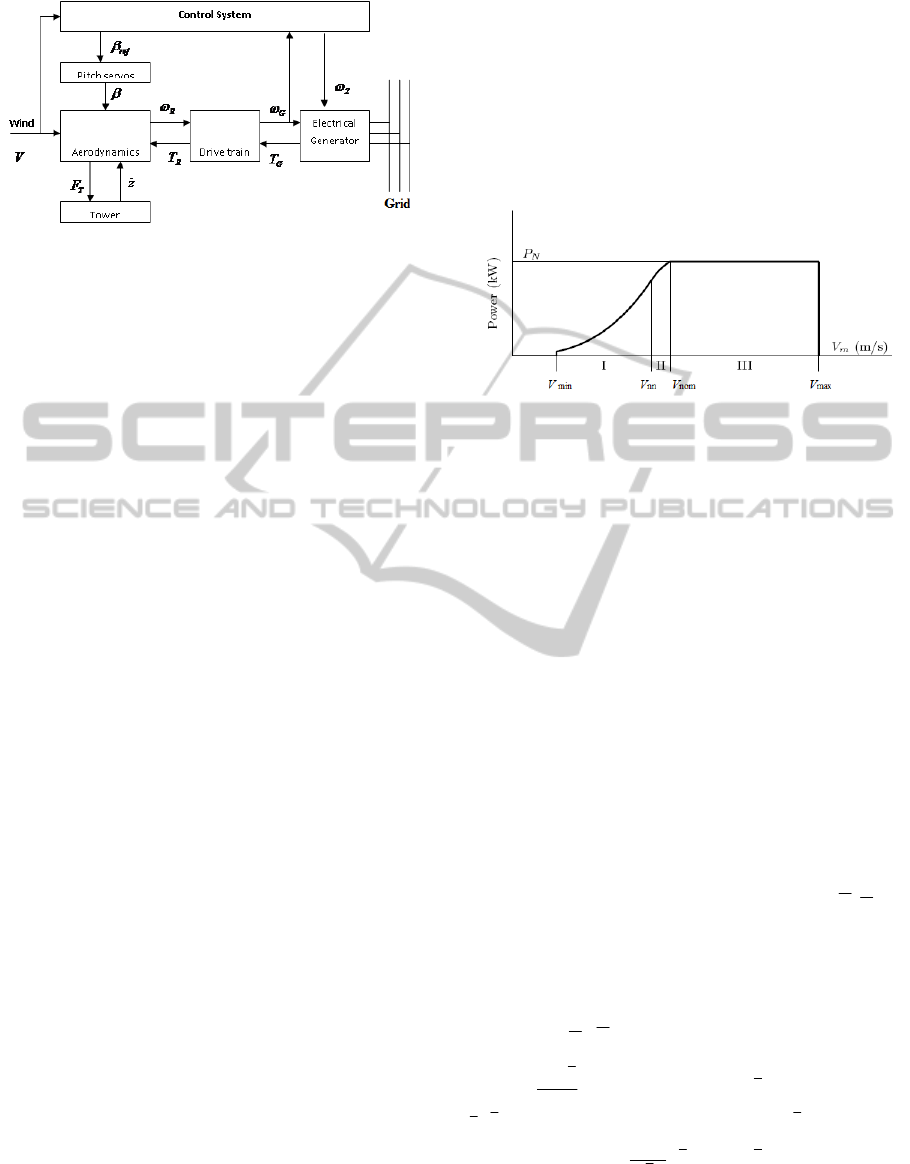
Figure 2: Wind energy conversion structure.
is the control input of the electrical generator.
The structure comprised by the tower and the
foundation supports the thrust force
, producing
an axial displacement z of the tower, nacelle and
blades.
Various analytical models of wind turbines were
introduced in the literature so far. A complete
description of wind energy conversion systems can
be found in (Burton et al., 2001), (Manwell et al.,
2009). Nowadays, there is a trend to take into
account even the smallest constructive details. Quite
complex models based on finite element theory are
also adopted, in order to describe the blades variable
geometry. But the most important and complex
subsystem of a wind turbine is the electrical
generator. Many wind turbines installed in grid
connected application use squirrel cage induction
generators (SQIG), operating within a range of
speeds slightly higher than the synchronous speed.
Driven by the desire of operating the wind turbine at
maximum efficiency, an increasingly popular option
today is the doubly fed IG (DFIG), being used in
variable-speed applications.
In this paper, the main goal is to shape and design
the control strategy for a variable speed wind
turbine. Thus, by using suitable power electronic
converters in our variable-speed machine, a robust
controller could be implemented. The pitch angle
will be fixed at its optimum value, that is
opt
.
3.2 Control Objectives and Strategies
One promising way to reduce the electricity cost
produced by a wind energy conversion system is to
improve its control system. This involves a series of
partial objectives and the judicious balancing of their
requirements. First of all, maximizing the energy
production is a main requirement. This involves
optimum conversion of wind energy, guaranteeing
both maximum yield and a good power quality.
Another objective is to maximize the faultless life of
the rotor drive train and other structural components
(actuators, mechanical structure) in the presence of
changes in the wind (direction, speed, turbulence),
as well as start-stop cycles. These two objectives are
actually conflicting (the tighter the closed loop
tracks the control strategy, the larger the transient
loads will be), and therefore well balanced
compromise must be formulated.
Figure 3: Power characteristic of a HAWT.
As already known, the ideal power characteristic
of a HAWT looks like in Figure 3. The turbine
analyzed here is generating the nominal power
nom
P
kW it was designed to provide, only in
case the wind speed is large enough (at least 12 m/s)
and varies in range III, between
V
and
max
V
m/s, the cut-off speed. When
varies in
range I, that is between the cut-in speed
min
V
m/s
and
nn
V
m/s, the generated power is smaller.
Thus, the generation objective is to extract all the
available power. Finally, there is region II, which is
a transition between region I and III.
A well chosen control strategy can provide a
trade-off between the ideal power characteristics and
the maximum faultless life of the structural
components. The basic control strategy, adopted in
this research, and detailed in (Lescher, 2006), is
plotted in Figure 4, in the parameter space
,
V
,
formed by the generator rotational speed and the
wind speed.
This strategy is selected to make the best use of
the HAWT. The function that describes the
dependence
ω
is defined as:
(
)
nn
3
nom nom
λ
ω ω
ω
ω s.t. k =
opt
G
P
G
V
V V
R
R
C V P V V
V
≤
= ≤ ≤
≥
(17)
Note that this curve represents the desired
trajectory (thus, the locus) of all the operating points
ICINCO2012-9thInternationalConferenceonInformaticsinControl,AutomationandRobotics
406