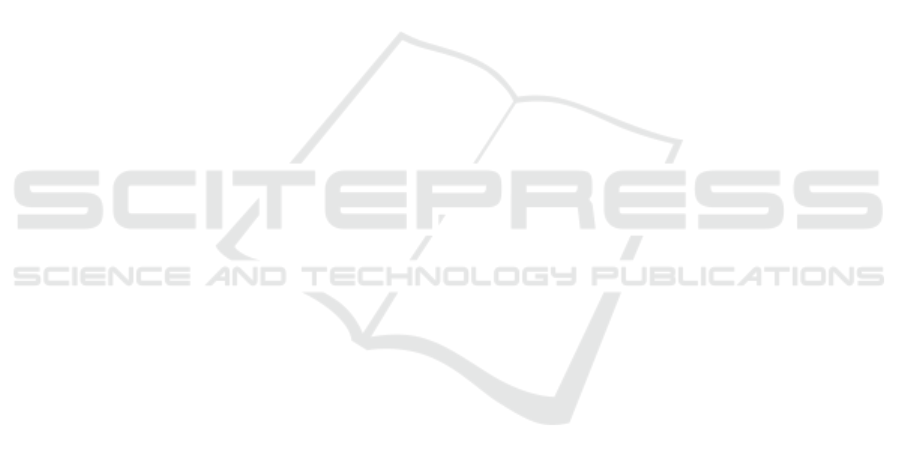
Virtual Mechanism Approach for Dual-arm Manipulation
Nejc Likar
1,2
, Bojan Nemec
2
and Leon
ˇ
Zlajpah
2
1
Jozef Stefan International Postgraduate School, Jamova 39, 1000 Ljubljana, Slovenia
2
Jozef Stefan Institute, Jamova 39, 1000 Ljubljana, Slovenia
Keywords:
Dual-arm Manipulation, Object Manipulation, Virtual Mechanism.
Abstract:
We propose a novel control approach for cooperative dual-arm object manipulation. Our scheme has three
typical features: (1) the two arms with the object together form a new kinematic chain, where the base of
the second arm is the end-effector of the new robot; (2) the object between the robots is defined as a virtual
mechanism, therefore manipulating the object is accomplished by controlling the virtual mechanism; (3) the
proposed scheme allows cooperative dual-arm systems performing a task while moving on mobile platforms.
The proposed algorithm is verified with experiments on a dual-arm system with Kuka LWR robots, and simu-
lations with 2 different robots: Kuka LWR on a fixed support and Mitsubishi PA10 robot on a mobile platform
Nomad XR400.
1 INTRODUCTION
There are many advantages and benefits using dual-
arm robots. For example, two arms can perform inde-
pendent or coordinated complex bimanual assembly
tasks without the aid of fixtures or jigs, transfer volu-
minous and heavy objects. Cooperative manipulation
of objects with a dual-arm robot provides more flexi-
ble and versatile task execution than the manipulation
of object with a single arm robot.
Control policies for cooperative manipulators
can be roughly divided into two categories: sym-
metric formulation and task-oriented formulation.
The kinetostatic symmetric formulation proposed by
(Uchiyama and Dauchez, 1992) is based on mappings
between forces and velocities at the tightly grasped
object and their counterparts in the ”virtual sticks”.
The major problem in this formulation is that the task-
space kinetostatic variables are often unsuitable for
the description of the cooperative task. The task-
oriented formulation proposed by (Caccavale et al.,
2000) and (Chiacchio and Chiaverini, 1998) fully
characterises a cooperative operational space and al-
lows the user to specify the task in terms of geometri-
cally meaningful motion variables defined at the posi-
tion/orientation level. The main advantage of defining
the cooperative task-space is that the control can be
applied to flexible objects and to nonrigid grasps. In
both formulations above, the cooperative task is de-
scribed by the absolute position and orientation of the
objects origin, and the relative position and orienta-
tion between the arm end-effectors. However, many
cooperative tasks that can be performed with a dual-
arm robot are independent of absolute position and
orientation of the object. Example of such a task are
screwing a cap on the bottle, playing a harmonica, etc.
In industrial practice cases when robots are placed
on a conveyor or on a vehicle, are common. The
control of cooperativemanipulators performing a task
when base of one robot is moving is not straightfor-
ward. (Khatib et al., 1996) proposed a dynamic co-
ordination strategy for multiple mobile manipulator
cooperation. (Osumi, 1996) proposed cooperativepo-
sition controlled manipulators on mobile platforms as
free joint mechanisms for achieving mechanical com-
pliance in order to avoid excessive inner forces be-
tween the manipulators.
In this paper, a different approach for control the
cooperative manipulators performing a task is pro-
posed. Our approach is based on a representation of
two robot arms together with the object, as an aug-
mented kinematic chain. The base frame of this kine-
matic chain is located at the base frame of the first
robot, while the end-effector is located at the base
frame of the second robot. The task between the robot
arms is defined as a virtual mechanism with arbitrary
degrees of freedom (Nemec and
ˇ
Zlajpah, 2009). The
task is performed by controlling the internal variables
(joints) of the virtual mechanism.
The proposed formulation allows cooperative ma-
nipulators performing a task also in the case when
their bases are moving on a conveyor or on a mo-
321
Likar N., Nemec B. and Žlajpah L..
Virtual Mechanism Approach for Dual-arm Manipulation.
DOI: 10.5220/0004046203210326
In Proceedings of the 9th International Conference on Informatics in Control, Automation and Robotics (ICINCO-2012), pages 321-326
ISBN: 978-989-8565-22-8
Copyright
c
2012 SCITEPRESS (Science and Technology Publications, Lda.)