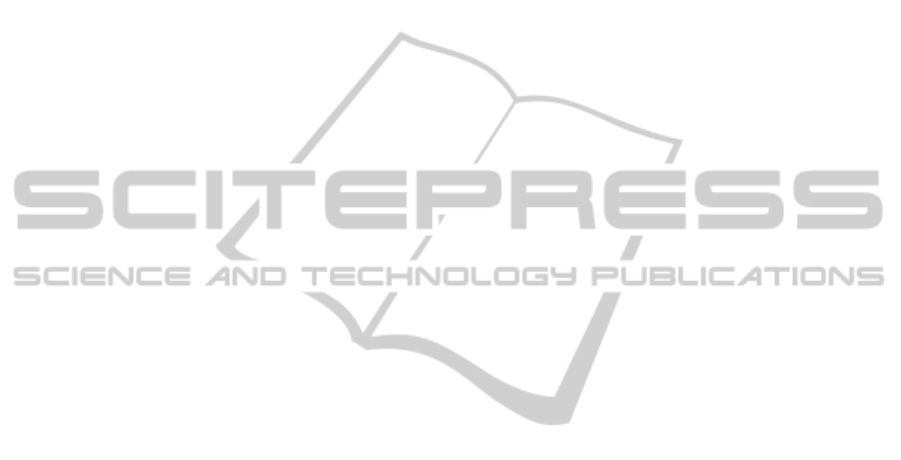
reaction to specific events. This framework allows
to define real-time transactions where multiple steps
have to be executed with timing constraints in a given
sequence or as reaction to certain events. Further-
more, this approach incorporates means to specify
safe strategies that are to be applied when errors occur
or the task was canceled. Based on these high-level
command descriptions, we introduced an algorithm to
transform them into a low-level dataflow language, so
that they can be executed on a robot controller with
real-time guarantees.
Upon this foundation, high-level features such as
advanced error handling on the non-realtime side can
be implemented and provided. To achieve this, real-
time reaction to error events within transaction com-
mands is used to bring the robot into a stable state,
and an exception on the Java side is thrown to in-
voke error handling in the application. Furthermore,
we have experimented with strategies to safely switch
between two real-time transactions while the robot
is still in motion. For industrial robots, this can be
used to change the executed task without requiring the
robot to stop during the task switch (e.g. for blending
motions). We are also currently working on ways of
describing the robot transactions and command coor-
dination in an even more user-friendly way, such as
through recurring patterns and graphical editors for
state charts or flow charts.
ACKNOWLEDGEMENTS
This work presents results of the research project Soft-
Robot which was funded by the European Union and
the Bavarian government. The project was carried
out together with KUKA Laboratories GmbH and
MRK-Systeme GmbH and was kindly supported by
VDI/VDE-IT.
REFERENCES
Andr
´
e, C. (1996a). Representation and analysis of reactive
behaviors: A synchronous approach. In Proc. IMACS
Multiconference on Computational Engineering in
Systems Applications, pages 19–29, Lille, France.
Andr
´
e, C. (1996b). SyncCharts: A visual representation of
reactive behaviors. Technical Report RR 95–52, rev.
RR (96–56), I3S/INRIA, Sophia-Antipolis, France.
Angerer, A., Hoffmann, A., Schierl, A., Vistein, M., and
Reif, W. (2010). The Robotics API: An object-
oriented framework for modeling industrial robotics
applications. In Proc. 2010 IEEE/RSJ Intl. Conf. on
Intelligent Robots and Systems (IROS 2010), Taipeh,
Taiwan, pages 4036–4041. IEEE.
Bischoff, R., Kurth, J., Schreiber, G., Koeppe, R., Albu-
Sch
¨
affer, A., Beyer, A., Eiberger, O., Haddadin, S.,
Stemmer, A., Grunwald, G., and Hirzinger, G. (2010).
The KUKA-DLR lightweight robot arm - a new ref-
erence platform for robotics research and manufactur-
ing. In Proc. IFR Int. Symposium on Robotics (ISR
2010).
Borrelly, J.-J., Coste-Mani
`
ere, E., Espiau, B., Kapellos, K.,
Pissard-Gibollet, R., Simon, D., and Turro, N. (1998).
The ORCCAD architecture. Intl. J. of Robotics Re-
search, 17(4):338–359.
Bruyninckx, H. (2001). Open robot control software: the
OROCOS project. In Proc. 2001 IEEE Intl. Conf. on
Robotics and Automation, pages 2523–2528, Seoul,
Korea.
Caspi, P., Pilaud, D., Halbwachs, N., and Plaice, J. A.
(1987). LUSTRE: A declarative language for real-
time programming. In Proc. 14th ACM SIGACT-
SIGPLAN Symposium on Principles of Programming
Languages, pages 178–188, Munich, Germany.
Hoffmann, A., Angerer, A., Ortmeier, F., Vistein, M., and
Reif, W. (2009). Hiding real-time: A new approach
for the software development of industrial robots. In
Proc. 2009 IEEE/RSJ Intl. Conf. on Intelligent Robots
and Systems (IROS 2009), St. Louis, Missouri, USA,
pages 2108–2113. IEEE.
MacKenzie, D. C., Arkin, R., and Cameron, J. M.
(1997). Multiagent mission specification and
execution. Autonomous Robots, 4:29–52.
10.1023/A:1008807102993.
Peterson, J. L. (1981). Petri Net Theory and the Modeling
of Systems. Prentice Hall PTR, Upper Saddle River,
NJ, USA.
Pires, J. N. (2009). New challenges for industrial robotic
cell programming. Industrial Robot, 36(1).
Schneider, S. A., Chen, V. W., Pardo-Castellote, G., and
Wang, H. H. (1998). ControlShell: A software archi-
tecture for complex electromechanical systems. In-
ternational Journal of Robotics Research, 17(4):360–
380.
Simmons, R. and Apfelbaum, D. (1998). A task description
language for robot control. In Proc. 1998 IEEE/RSJ
Intl. Conf. on Intelligent Robots and Systems, Victoria,
Canada.
Smits, R., Laet, T. D., Claes, K., Bruyninckx, H., and Schut-
ter, J. D. (2008). iTASC: a tool for multi-sensor inte-
gration in robot manipulation. In Proc. IEEE Interna-
tional Conference on Multisensor Fusion and Integra-
tion for Intelligent Systems.
Soetens, P. and Bruyninckx, H. (2005). Realtime hybrid
task-based control for robots and machine tools. In
Proc. 2005 IEEE Intl. Conf. on Robotics and Automa-
tion, pages 259–264, Barcelona, Spain.
Vistein, M., Angerer, A., Hoffmann, A., Schierl, A., and
Reif, W. (2010). Interfacing industrial robots using
realtime primitives. In Proc. 2010 IEEE Intl. Conf. on
Automation and Logistics (ICAL 2010), Hong Kong,
China, pages 468–473. IEEE.
ICINCO2012-9thInternationalConferenceonInformaticsinControl,AutomationandRobotics
158