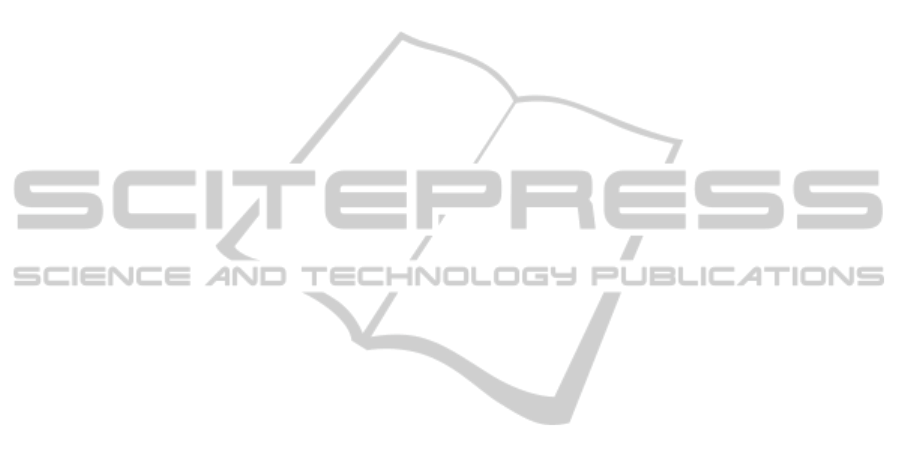
limits leads to termination of the jogging action and
requires it to be restarted. Similar problems arise
in singular robot poses. First tests with strategies
that limit joint velocities in such situations look very
promising.
In the future, we will continue to create case stud-
ies like this one, as we see them as an excellent option
for evaluating the current state of a software frame-
work. Beyond that, the developed teleoperation sys-
tem could be a valuable tool for controlling e.g. a
planned mobile two-arm manipulator.
ACKNOWLEDGEMENTS
This work presents results of the research project
SoftRobot which was funded by the European Union
and the Bavarian government within the High-
Tech-Offensive Bayern. The project was carried
out together with KUKA Laboratories GmbH and
MRK-Systeme GmbH and was kindly supported by
VDI/VDE-IT.
REFERENCES
Angerer, A., Hoffmann, A., Schierl, A., Vistein, M., and
Reif, W. (2010). The Robotics API: An object-
oriented framework for modeling industrial robotics
applications. In Proc. 2010 IEEE/RSJ Intl. Conf. on
Intelligent Robots and Systems (IROS 2010), Taipeh,
Taiwan, pages 4036–4041. IEEE.
Beetz, M., Klank, U., Kresse, I., Maldonado, A.,
M
¨
osenlechner, L., Pangercic, D., R
¨
uhr, T., and
Tenorth, M. (2011). Robotic roommates making pan-
cakes. In 11th IEEE-RAS International Conference on
Humanoid Robots, Bled, Slovenia.
Bischoff, R., Kurth, J., Schreiber, G., Koeppe, R., Albu-
Sch
¨
affer, A., Beyer, A., Eiberger, O., Haddadin, S.,
Stemmer, A., Grunwald, G., and Hirzinger, G. (2010).
The KUKA-DLR lightweight robot arm - a new ref-
erence platform for robotics research and manufactur-
ing. In Proc. IFR Int. Symposium on Robotics (ISR
2010).
Jain, A. and Kemp, C. (2010). El-e: an assistive mobile
manipulator that autonomously fetches objects from
flat surfaces. Autonomous Robots, 28:45–64.
Meeussen, W., Wise, M., Glaser, S., Chitta, S., McGann, C.,
Mihelich, P., Marder-Eppstein, E., Muja, M., Eruhi-
mov, V., Foote, T., Hsu, J., Rusu, R. B., Marthi, B.,
Bradski, G., Konolige, K., Gerkey, B., and Berger, E.
(2010). Autonomous door opening and plugging in
with a personal robot. In Int. Conference on Robotics
and Automation.
Micire, M., Desai, M., Drury, J. L., McCann, E., Norton, A.,
Tsui, K. M., and Yanco, H. A. (2011). Design and val-
idation of two-handed multi-touch tabletop controllers
for robot teleoperation. In Proc. 15th Int. Conf. on
Intelligent User Interfaces, IUI ’11, pages 145–154,
New York, NY, USA. ACM.
Seifried, T., Haller, M., Scott, S. D., Perteneder, F., Rendl,
C., Sakamoto, D., and Inami, M. (2009). CRISTAL: a
collaborative home media and device controller based
on a multi-touch display. In Proc. ACM Int. Conf.
on Interactive Tabletops and Surfaces, ITS ’09, pages
33–40, New York, NY, USA. ACM.
Siciliano, B. and Khatib, O., editors (2008). Springer Hand-
book of Robotics. Springer, Berlin, Heidelberg.
Skrzypczyliski, P. (1997). Supervision and teleoperation
system for an autonomous mobile robot. In Proc.
1997 IEEE/RSJ Int. Conf. on Intelligent Robots and
Systems, volume 2, pages 1177 –1181 vol.2.
Vistein, M., Angerer, A., Hoffmann, A., Schierl, A., and
Reif, W. (2010). Interfacing industrial robots using
realtime primitives. In Proc. 2010 IEEE Intl. Conf. on
Automation and Logistics (ICAL 2010), Hong Kong,
China, pages 468–473. IEEE.
Zalud, L. (2006). ARGOS - system for heterogeneous mo-
bile robot teleoperation. In Proc. 2006 IEEE/RSJ Int.
Conf. on Intelligent Robots and Systems, pages 211
–216.
ICINCO2012-9thInternationalConferenceonInformaticsinControl,AutomationandRobotics
332