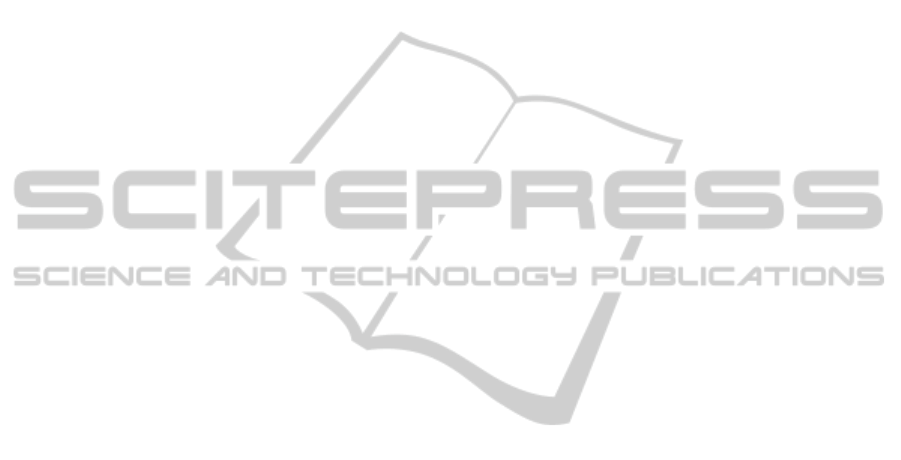
understanding of known systems, provide qualitative
and quantitative insights and guidance for
experimental work and produce qunatitative results
that replace difficult, dangerous or expensive
experiments (DePaoli, 2011).
The pyroprocessing contains various unit
processes and various types of nuclear materials that
flow in and out of those unit processes. It is a batch
type process in overall terms, i.e., reciept and
shipment of material among unit process, however,
unit process itself features continuous chemical or
electro-chemical process. Unit process may have a
different batch capacity and different processing
time. Also, there is feedback of output material on a
unit process into a prior unit process. In addition,
nuclear elements may take different routes as the
process goes on. Due to this complexity, it is
difficult to understand the dynamic behaviors of the
material flow in the pyroprocess. With this
background, this study was undertaken. Simple
material flow in the pyroprocess can be easily
understood by static mass balance. However, a
simple material flow based on the static mass
balance cannot give insight into any dynamic
behavior of the material flow because it cannot take
into account changes according to time and event.
An EXCEL-like software is widely used to
establish the static mass balance of the overall
process but it is very restrictive to implement a
dynamic material flow in the pyroprocess. In this
study, a modeling and simulation tool for discrete
event dynamic system (DES), ExtendSim was
utilized for the plant level framework of a dynamic
material flow. The pyroprocess was modeled as DES
in this work and then a dynamic material flow was
simulated under the framework.
2 R&D STATUS
2.1 The U.S.
Motivated by the challenges and needs in nuclear
energy systems that can be addressed bymodeling
and simulation, the Office of Nuclear Energy of the
U.S. Department of Energy hasarticulated a vision
for a Nuclear Energy Advanced Modeling and
Simulation (NEAMS) program.NEAMS is aimed
toward building on the success of recent programs in
advanced scientificcomputing, namely, ASCI and
SciDAC, with a focus on very different challenges.
Thesechallenges include the need for nuclear energy
systems to be licensed by regulators andmoving
advanced technologies out of the research
environment and into the hands of theengineers who
will design, build, and operate the new nuclear
energy systems. NEAMS will provide a
comprehensive solution and is organized into the
following five elements:
• Integrated Performance and Safety Codes (IPSC)
end-to-end codes to understand the detailed,
integrated performance of new nuclear systems
including the following: Nuclear Fuels, Reactor
Core & Safety, Separations and Safeguards, Waste
Forms and Near-Field Repositories.
• Fundamental Methods and Models
• Verification, Validation, and Uncertainty
Quantification
• Capability Transfer Enabling Computational
Technologies
Through the NEAMS-IPSC, the U.S. is devoting to
develop reprocessing plant level toolkit named
RPTk (Reprocessing Plant Toolkit), which uses open
source platform to accormodate legarcy codes
accross the U.S. (McCaskey, 2011). RPTk
implements a data flow architecture that is the
source of the system’s extensibility and scalability.
Data flows through physicochemical modules
sequentially, with each module importing data,
evolving it, and exporting the updated data to the
next downstream module. This is accomplished
through various architectural abstractions designed
to give RPTk true plug-and-play capabilities.
2.2 Japan
A decade ago, Japan developed an analysis code
(Okamura, 2002) using the object-oriented software
ExtendSim for the estimation of material balance for
the system design of the pyrochemical reprocessing
plants consisting of batch processes. This code can
also estimate the radioactivity balance, decay heat
balance and holdup, and easily cope with the
improvement of the process flow, and so on. The
study describes the outline of the code and
estimation of the material balance in the oxide
electrowining reprocessing system under
consideration of the solvent recycling time.
Howerver, it is difficult to find out current activity
with respect to modeling and simulation spent fuel
recyling facility in japan.
2.3 Korea
In order to analyze operational issues in a
pyroprocessing head-end facility, discrete event
modeling approach was applied (Lee et al., 2009).
Also, a code development study on the dynamic
SIMULTECH 2012 - 2nd International Conference on Simulation and Modeling Methodologies, Technologies and
Applications
378