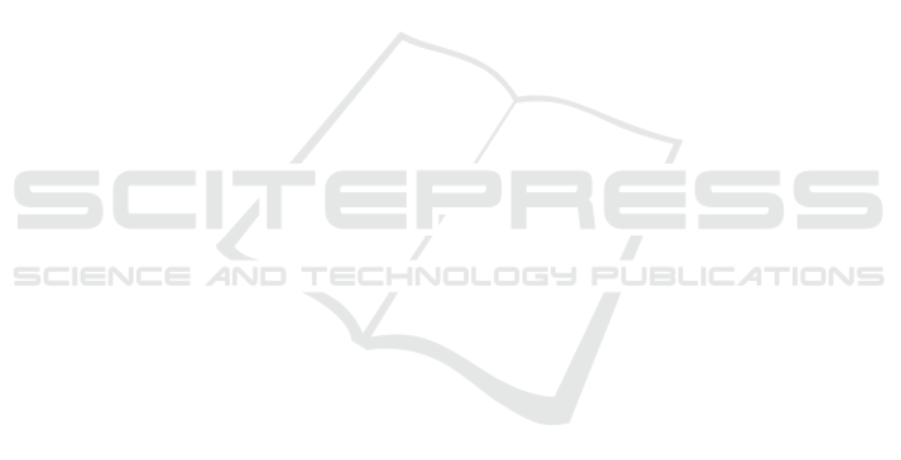
Direct Numerical Simulation of Flow Past a Sphere in a Plane
Turbulent Boundary Layer with Immersed Boundary Method
Hui Zhao, Anyang Wei, Kun Luo and Jianren Fan
State Key Laboratory of Clean Energy Utilization, Zhejiang University, Hangzhou, China
Keywords: Direct Numerical Simulation, Immersed Boundary Method, Boundary Layer, Sphere, Plane.
Abstract: Direct Numerical Simulation coupled with Immersed Boundary Method (IBM) has attracted wide atten-
tion recent years, making this technique a significant role in many practical engineering areas. This paper
described a direct numerical study of flow past a sphere above a plane, which can obtain detail infor-
mation of flow field and vortex structure. A combined multiple-direct forcing and immersed boundary
method (MDF/IBM) was used to deal with the coupling between fluid and solid. The Reynolds number
based on sphere diameter was 4171. Behaviours of the vortices were observed through the simulation. The
velocity distribution switched from laminar boundary to turbulent boundary. A recirculation region was
observed behind the sphere. The influence of the sphere on the boundary layer, the center peak defect, the
turbulence intensity and the Reynolds stresses are explored.
1 INTRODUCTION
A number of studies have been carried out on a flow
pasting a three-dimensional obstacle placed on the
plane boundary, especially the flow past a sphere.
Obtaining enough data and understanding the struc-
ture of flow field and vortex are extremely necessary.
Because from an engineering viewpoint, the spheri-
cal structure application can be seen everywhere in
practice, such as some structures exposed in the
wind, vehicles moving in fluid and so on. After
Schlichting studied a blunt obstacle placed on the
plane boundary with the effect of surface roughness
(Schlichting, 1939), the drag of a sphere placed on a
ground plate (Klemin et al., 1939) was investigated.
An experimental study of the turbulent shear layer
behind a sphere placed on a plane boundary was
performed (Okamoto, 1980). The surface pressure
distribution on a sphere, the velocity and pressure
distribution in the shear layer behind a sphere were
measured. It was found that the wall wake behind a
sphere became low and spreads transversely with the
downstream distance increasing. Takayuki (Taka-
yuki, 2008) investigated the flow around a sphere
placed at various heights above a plane boundary. In
Takayuki’s experimental study, the surface pressure
distribution on the sphere and the plane were meas-
ured, meanwhile empirical equations of the drag and
lift coefficients were defined.
In recent years, with the development of the
computer technology, it becomes possible to do
research on two-phase flow in turbulent boundary
layer using direct numerical simulation method.
Fully resolved direct numerical simulations were
considered to investigate a turbulent channel flow
over an isolated particle of finite size (Zeng et al.,
2008) with the spectral element methodology (SEM).
To validate a joint application of direct numerical
simulation and a combined multiple-direct forcing
and immersed boundary method (MDF/IBM), a flow
past an isolated three-dimensional hemispherical
roughness element mounted on a flat plate was
simulated (Zhou et al., 2010). Nevertheless,
numerical simulation studies on the interaction
between sphere and plane boundary layer are
lacking, which could be significant to engineering
application.
This paper describes a direct numerical study on
the flow field and the vortex structure on a sphere
above a plane. The influence of the sphere on the
boundary layer is explored, such as velocity
distribution, turbulence intensity, Reynolds stresses
and vortex structure.
243
Zhao H., Wei A., Luo K. and Fan J..
Direct Numerical Simulation of Flow Past a Sphere in a Plane Turbulent Boundary Layer with Immersed Boundary Method.
DOI: 10.5220/0004056802430249
In Proceedings of the 2nd International Conference on Simulation and Modeling Methodologies, Technologies and Applications (SIMULTECH-2012),
pages 243-249
ISBN: 978-989-8565-20-4
Copyright
c
2012 SCITEPRESS (Science and Technology Publications, Lda.)