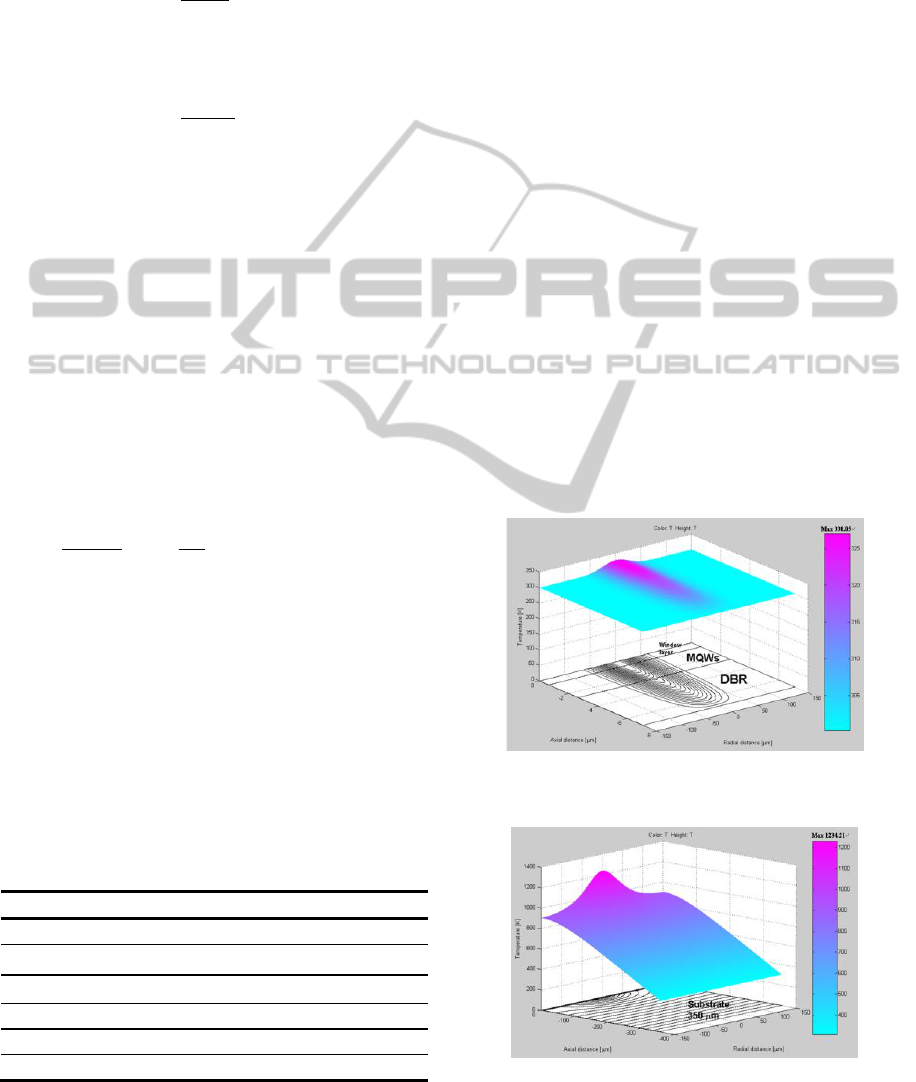
the whole structure into four parts: the window
layer, the multiple QWs, the DBR and the substrate.
The total thermal conductivity in axial and radial
direction of each part including multiple layers can
be written as
And the total absorption coefficient of each
part is obtained by
where
and
are the thermal conductivity
and absorption coefficient of the ith layer, and
is
the thickness. In the computation, the wavelengths
of pump and laser are 808 and 1040 nm; the value of
0.475µm
-1
for the absorption coefficient of GaAs
layer and 1µm
-1
for the absorption coefficient of
In0.2Ga0.8As/Al0.05Ga0.95As QWs are used.
Then, the temperature, the heat flux and the
gradient of temperature can be obtained by solving
the standard heat equation (steady state):
where k is the thermal conductivity and T is the
temperature.
The heat loading density Q is calculated by
www
ww
w
zz
r
P
Q
0
2
2
2
exp
2
exp
2
where
is the fraction of absorbed pump
power that goes to heating, andη=1-λ
pump
/λ
laser
in
MQWs part and η=1 in other parts. α is the
absorption coefficient of each part, r is the
coordinate in radial direction and z is the coordinate
in axial direction. The start position z0 of each part is
different and the start position of window layer is
chosen to be zero. In this paper, the pump power and
the pump spot radius are assumed to be 10W and 50
mm unless there is a special explanation.
Table 1: Parameters of some materials.
2.2 Results of the Simulation
We used the finite-element analysis method to
simulate the heat distribution of the semiconductor
chip when the heat sink temperature was 300 k. The
parameters used is in table 1. We could discovery
the heat spread affected by the thickness of the
substrate illustrated in Fig.2. and Fig.3. We also can
find the outstanding heat spread result of the
diamond chip from Fig.3. and Fig. 4.
The Fig.2 described the temperature variation
when the thickness of the gain chip substrate is 0
µm, the maximum temperature rise is 30.05 K,
compare to the 934.21 K of the max temperature rise
represented in Fig.3. when the thickness of the gain
chip is 350 µm. So the substrate removal is an
effective method to improve the heat spread of gain
chip.
At the same time, a 300µm-thick diamond chip
was bonded on the gain chip with 350 µm substrate,
as shown in Fig. 4. The maximum temperature rise
is 56.79 K, which is much lower than the 934.21 K
shown in Fig.3. Therefore, the diamond has
outstanding heat spread results. Whilst using
heatspreader has superior heat spread effect, and
we’ll try to bonding the diamond on the gain chip to
obtain higher fundamental power so as to get higher
harmonic power in our next work.
Figure 2: Heat distribution of the semiconductor chip
without substrate.
Figure 3: Heat distribution of the semiconductor chip
when its substrate is 350 µm-thick.
SIMULTECH 2012 - 2nd International Conference on Simulation and Modeling Methodologies, Technologies and
Applications
232