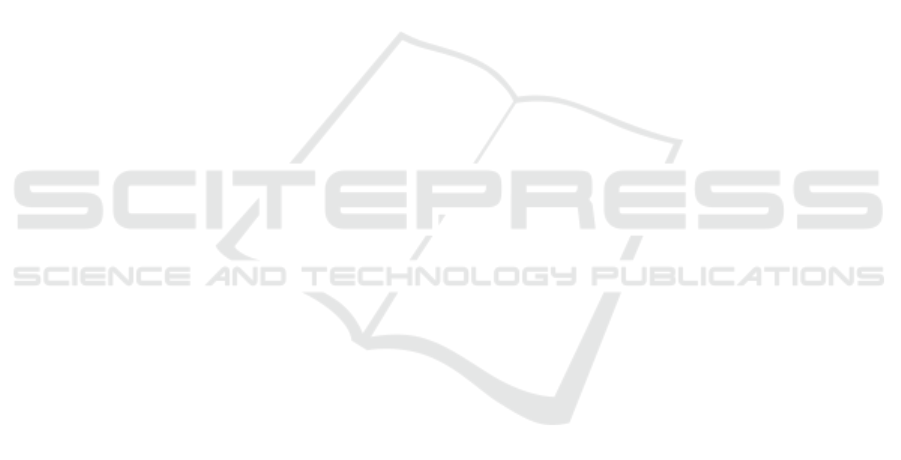
Estimating Real Process Derivatives in on-Line Optimization
A Review
M. Mansour
Faculty of Electronics and Computer Science, USTHB, PO. BOX 32, El_Allia. Bab-Ezzouar, Algiers, Algeria
Keywords: on-Line Optimization, Model-based, Process Derivatives, ISOPE Algorithm, ANN.
Abstract: The solution of the Integrated System Optimization and Parameter Estimation (ISOPE) problem necessitates
the calculus of real process output derivatives with respect to the inputs. This information is needed in order
to satisfy first and second order optimality conditions. Several methods exist and have been developed for
calculating these derivatives. In this paper a review of most of the existing methods is presented, in which
the Finite Difference Approximation, Dual Control Optimization, Broydon’s method, Dynamic Model
Identification, with both linear and nonlinear models, together with a neural networks scheme are presented
and applied, under simulation, to a cascade Continuous Stirred Tank Reactor (CSTR) system. The results
are then discussed and compared to identify the advantages and disadvantages of using each method.
1 INTRODUCTION
The requirement for processes to operate at their
optimum operating condition is becoming
increasingly prevalent. One model-based algorithm
that has been developed and which can achieve
optimum process operation in spite of model-reality
mismatch is the Integrated System Optimization and
Parameter Estimation (ISOPE) algorithm (Roberts,
1979). One requirement of the ISOPE algorithm, in
order to satisfy the necessary optimality conditions,
is the need for estimates of real process derivatives.
These derivatives are estimated on-line at each
iteration of the algorithm. The finite difference
method originally used by Roberts (1979) to
estimate these derivatives has proven not to be
efficient in the case of large, slow and noisy
processes (Mansour and Ellis, 2003). Alternative
methods have therefore been developed. The
dynamic model identification technique, which is
based on the identification of a dynamic model, was
incorporated within the ISOPE algorithm by Zhang
and Roberts (1990). Although this technique proved
to be fast enough as it performs the identification
during transient, it encountered some difficulties
such as: the huge amount of data needed and the
poor, inaccurate, model it produces at the beginning
of the identification. After that, an algorithm with
dual control effect was proposed (Brdys and
Tatjewski, 1992). In this algorithm the current
control signal is generated to satisfy the main control
goal and at the same time provide sufficient
information for future identification action. The
main advantage of this algorithm is that it does not
need excessive set-point changes to estimate the
process derivatives. However, this method
encountered the same type of problems as the
previous ones. Broydon's approximation method
based on the well-known Broydon’s family of
formulas which are mainly oriented to the
approximation of derivatives was also implemented
(Fletcher, 1980). Lately, a nonlinear version of the
dynamic model identification was applied and
implemented (Mansour and Ellis, 2003). In this
paper, a review of all these techniques together with
a method based on artificial neural networks is
presented. In addition, a comparison is made using
simulations carried out on a cascade CSTR system
to show the advantages and disadvantages of each
method.
2 THE OPTIMIZATION
PROBLEM AND THE ISOPE
ALGORITHM
We The ISOPE algorithm (or modified two steps)
was proposed by Roberts (Roberts, 1979) to solve
the general optimization problem of finding the
120
Mansour M..
Estimating Real Process Derivatives in on-Line Optimization - A Review.
DOI: 10.5220/0004059101200124
In Proceedings of the 2nd International Conference on Simulation and Modeling Methodologies, Technologies and Applications (SIMULTECH-2012),
pages 120-124
ISBN: 978-989-8565-20-4
Copyright
c
2012 SCITEPRESS (Science and Technology Publications, Lda.)