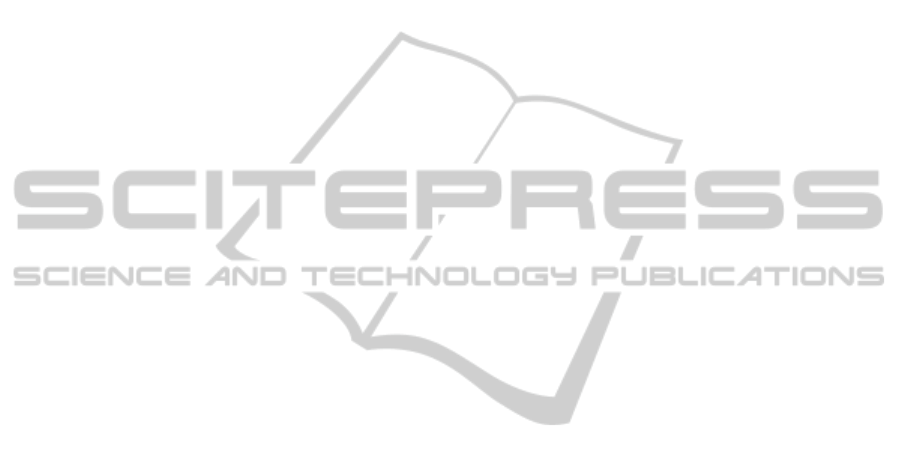
were found. As an example, a frequent failure of the
MainMicroController component, caused by the
raising of temperature over +135 °C, is emerged
with a subsequent swapping of the control to the
FailSafeMicroController component, and the
frequent disabling of the actuators with the
consequent shutdown of the ABS subsystem. To
overcome this abnormal behavior, which is emerged
in the simulation phase and reported in the DS
(Design Suggestions) document, a cooling fan and
the related task for its management have been
introduced. This task is able to turn cooling fan on
when temperature is higher than a fixed threshold by
avoiding an unnecessary operation of switching and
improving, as a consequence, the performance of the
overall ESC system and its reliability.
4 CONCLUSIONS
Despite a general consensus on the advantages that
could derive from the exploitation of model-based
approaches for system reliability analysis, the use of
these techniques has been traditionally unusual and
has not been recommended by international
standards until recently (IEC 61508, 2010). This
delay in the adoption is mainly due to the lack of
methods able to integrate available modeling
languages, tools and techniques in a consistent
modeling framework. To contribute to fill this lack,
the paper has presented an enhancement of a model-
based method for System Reliability Analysis
(RAMSAS), recently proposed in (Garro et al.,
2011; Garro, Tundis, 2012), through a case study in
the automotive domain concerning the reliability
analysis of an Electronic Stability Control system. In
particular, in the exploited version of RAMSAS the
following improvements have been introduced: (i)
the System Modeling phase now consists of four new
modeling activities (System Structure Modeling,
System Behavior Modeling, System Failure
Modeling, and System Integration Modeling); (ii) a
complementary adoption of Activity, Sequence, and
Statechart Diagrams for the behavioral modeling of
the system is proposed; (iii) the System Simulation
phase now consists of three new simulation activities
(Modeling Transformation, Parameters Setting, and
Simulation Execution); (iv) the Design Suggestions
(DS) document, produced in the Results Assessment
phase, adopts typical FMECA and FTA formats so to
ease the use of RAMSAS in conjunction with
classical RAMS techniques.
The proposal is strongly related to the approach
presented in (Cressent et al., 2011), however, as it
strongly relies on the Method Engineering paradigm
(Henderson-Sellers, 2003) its main ambition is to
provide a self-consistent method fragment for
system reliability analysis which can be easy
pluggable in various phases of a typical system
development process.
ACKNOWLEDGEMENTS
Andrea Tundis was supported by a grant funded in
the framework of the “POR Calabria FSE
2007/2013”.
REFERENCES
Cressent, R., Idasiak, V., Kratz, F., David, P., 2011.
Mastering safety and reliability in a model based
process. In Proc. of the Reliability and Maintainability
Symposium (RAMS). Lake Buena Vista, FL, USA,
January 24-27.
De Filippi, P., Tanelli, M., Corno, M., Savaresi, S. M.,
2010. Toward electronic stability control for two-
wheeled vehicles. In Proc. of the ASME Dynamic
Systems and Control Conference (DSCC). Boston,
MA, USA, September 13-15.
Dodson, B., Nolan, D., 2001. Practical Reliability
Engineering. John Wiley & Sons Ltd.
D’Ambrogio, A., Iazeolla, G., Pieroni, A., Gianni, D.,
2011. A model transformation approach for the
development of HLA-based distributed simulation
systems. In Proc. of the Int. Conf. on Simulation and
Modeling Methodologies, Technologies and
Application (SIMULTECH). Noordwikerhout, The
Netherlands, July 29–31.
Garro, A., Tundis, A., Chirillo, N., 2011. System
reliability analysis: a model-based approach and a case
study in the avionics industry. In Proc. of the 3rd Air
and Space Int. Conf (CEAS). Venice, Italy, Oct 24-28.
Garro, A., Tundis, A., 2012. A model-based method for
system reliability analysis. In Proc. of the Symposium
on Theory of Modeling and Simulation (TMS’12).
Orlando, FL (USA) 26-29 March.
Goga, V., Jediný, T., Královič, V., Klúčik, M., 2012.
Mechatronic model of Anti-lock Braking System (ABS)
- A Book Chapter of Mechatronics. Springer.
Henderson-Sellers B., 2003. Method engineering for OO
systems development. Communications of the ACM,
Vol. 46, No. 10, pp.73–78.
IEC 61508, 2010. Functional safety of
electrical/electronic/programmable electronic safety-
related systems, Parts 1-7.
Enhancing the RAMSAS Method for System Reliability Analysis - An Exploitation in the Automotive Domain
333