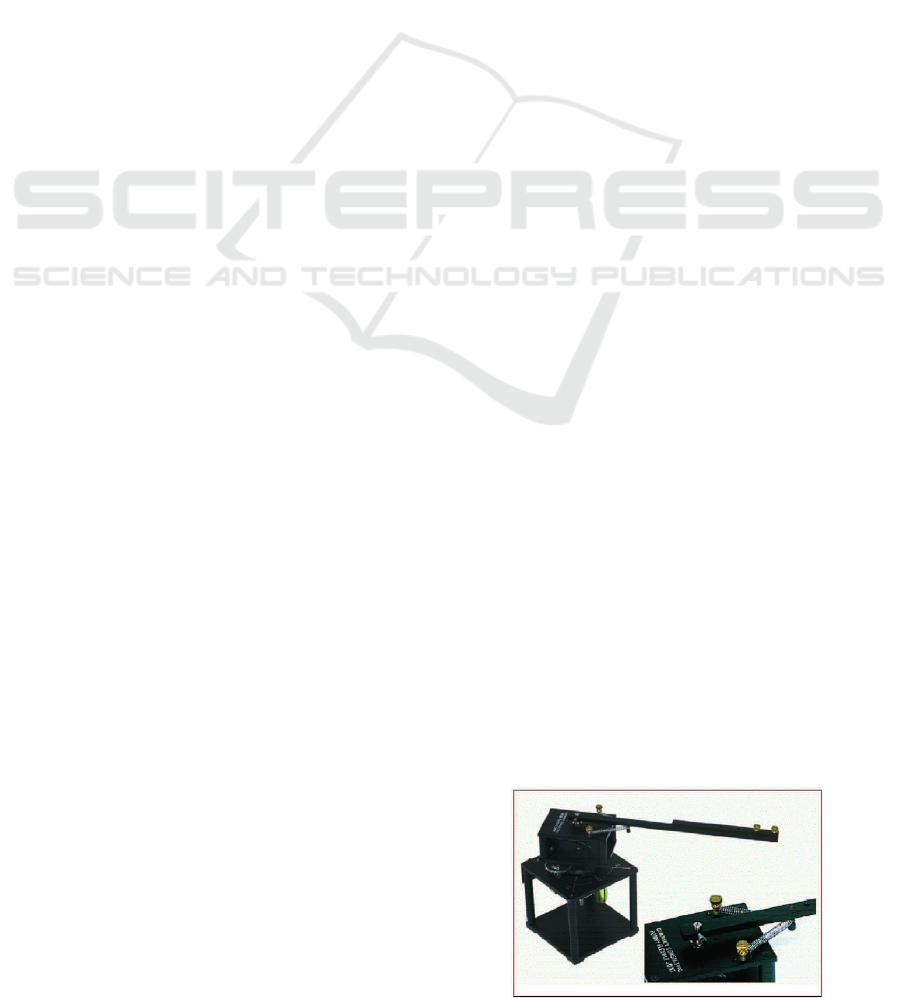
Flatness based Control of a 2 DOF Single Link Flexible Joint
Manipulator
E. D. Markus
1
, J. T. Agee
1
, A. A. Jimoh
1
, N. Tlale
2
and B. Zafer
3
1
Department of Electrical Engineering, Tshwane University of Technology, Pretoria, South Africa
2
Mobile Intelligent and Autonomous Systems, CSIR, Pretoria, South Africa
3
Department of Mechatronics Engineering, Kocaeli University, Kocaeli, Turkey
Keywords:
Flexible Joint Manipulator, Differential Flatness, Position Control.
Abstract:
The demand for high speed robotic manipulators with little or no vibrations has been a challenging research
problem. In this paper, a position control for a 2 DOF single link flexible manipulator with joint elasticity
is studied. It is shown that using the flatness control approach, faster response and less oscillations and
overshoots can be achieved. The flat output of the linearized system is determined as the tip of the manipulator
end effector. This output and a finite order of its derivatives is defined in terms of the input and states variables
of the manipulator. Using the parameters of the output in flat space, a trajectory is planned and executed to
test the effectiveness of the designed control.
1 INTRODUCTION
The control of flexible robotic manipulators is re-
quired in many applications where faster response,
lower energy consumption, lighter body mass, and
high position accuracy at the end effector are de-
manded. The problem of vibration control in these
systems has been a subject of research over the years
(Ghorbel et al., 1989; Sira-Ramirez et al., 1992;
Ider and
¨
Ozg¨oren, 2000; Ozgoli and Taghirad, 2006;
Tokhi and Azad, 2008; Jiang and Higaki, 2011). Ma-
nipulators with flexible links are difficult to control
due to their slow control response, high oscillations
and high overshoots. The flexible joint manipulator is
also known to exhibit a nonminimum phase behaviour
(Tokhi and Azad, 2008). This makes trajectory track-
ing for the system harder to achieve. From a robot ma-
nipulator design perspective, these disadvantages are
minimised by building the robot from rigid links and
joints that results in high stiffness. However such stiff
systems have been shown to be ineffective in terms of
high power consumption and positional inaccuracy.
Many mathematical and analytical models have
been proposed in the past to achieve control of these
flexible systems (Dwivedy and Eberhard, 2006; Tokhi
and Azad, 2008). Among these include the classical
PID control, feedback linearization, fuzzy logic con-
trol, sliding mode, H∞ control, linear quadratic con-
trol and neuro-fuzzy inference system. A comprehen-
sive survey of research in the control of flexible ma-
nipulators can be found in (Dwivedy and Eberhard,
2006; Ozgoli and Taghirad, 2006).
The concept of differential flatness proposed by
Fliess, Levine, Martin and Rouchon(1995) has been
applied to complex control problems(Fliess et al.,
1995). This study will apply the differential flatness
technique for the control of the single link flexible
joint robot manipulator. The differential flatness ap-
proach through the flat output is used to design an
asymptotically stable controller for suppressing vi-
brations of the flexible joint manipulator. Abdul-
Razak (2007) and Quanser (2012) have reported the
use of the linearized model of the flexible manipu-
lator(Abdul Razak, 2007; Quanser, 2012). The lin-
earized model is simulated with a PID controller and
compared with the flatness based control.
Figure 1: Physical model of flexible joint robot manipulator.
437
D. Markus E., T. Agee J., A. Jimoh A., Tlale N. and Zafer B..
Flatness based Control of a 2 DOF Single Link Flexible Joint Manipulator.
DOI: 10.5220/0004061104370442
In Proceedings of the 2nd International Conference on Simulation and Modeling Methodologies, Technologies and Applications (SIMULTECH-2012),
pages 437-442
ISBN: 978-989-8565-20-4
Copyright
c
2012 SCITEPRESS (Science and Technology Publications, Lda.)