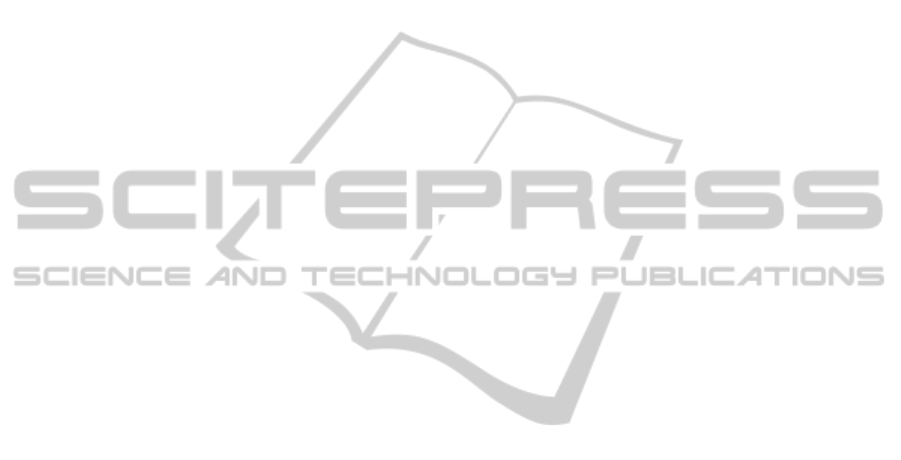
7 CONCLUSIONS
Reducing machining error in old turning machines
using smart material can reduce industrial waste, save
money and, improve design flexibility for new
cutting tools. The outcome of this work show
stiffness ratios in toolpost structural design have a
major rule in actuator selection and design. Support
stiffness in the direction of actuation should be
minimal. Tool bit to actuator stiffness should be
higher than one and to the extents that make tool error
is acceptable. Tool bit to actuator stiffness and tool
carrier (holder) to actuator stiffness both are preferred
to be high. The developed fuzzy algorithm for voltage
activation factor based on normalized error and its
rate proved a significant effectiveness in error
attenuation. Implementation if intelligent scheme
proved effectiveness during FEM simulation. Using
cognitive chips in real application as in Figure 8 is the
idea of future development.
REFERENCES
Abboud, N. N., Wojcik, G. L., Vaughan, D. K., Mould, J.,
Powell, D. J., and, Nikodym, L., (1998), Finite Element
Modeling for Ultrasonic Transonic Transducers,
Proceedings SPIE Int. Symposium on Medical Imaging,
San Diego, Feb 21-27, 1-24.
Dold, G., (1996), Design of a Microprocessor-Based
Adaptive Control System for Active Vibration
Compensation Using PMN Actuators, MS Thesis,
University of Maryland at College Park.
Eshete, Z., (1996), In Process Machine Tool Vibration
Cancellation Using Electrostrictive Actuators, Ph.D.
Thesis, University of Maryland at College Park.
Frankpitt, B. A., (1995), A Model of the Dynamics of a
Lathe Toolpost that Incorporates Active Vibration
Suppression, Institute for System Research, University
of Maryland at College Park.
Gopalakrishnan, V., Fedewa, D., Mehrabi, M. G., Kota, S.
and Orlandea, N., (2002), Design of Reconfigurable
Machine Tools, ASME J. Manuf. Sci. Eng., Technical
Briefs, 124, 483-485.
Hurtado, J. F., and Melkote, S. N., (2001), Improved
Algorithm for Tolerance-Based Stiffness Optimization
of Machining Fixtures, ASME J. Manuf. Sci. Eng., 123,
720-730.
Luan, J., and, Lee, F. C., (1998), Design of a High
Frequency Switching Amplifier for Smart Material
Actuators with Improved Current Mode Control, PESC
98, Vol. 1, Fukuoka, 59-64.
Moon, Y., and, Kota, S., (2002), Design of Reconfigurable
Machine Tools, ASME J. Manuf. Sci. Eng., Technical
Briefs, 124, 480-483.
Passino, K. M., and Yurkovich, S., (1998), Fuzzy Control,
Addison Wesley Longman, Inc.
Piefort, V., (2001), Finite Element Modeling of
Piezoelectric Active Structures, Ph.D. Thesis, ULB,
Active Structures Laboratory- Department of
Mechanical Engineering and Robotics.
Rashid, M. K. (2011). Neurofuzzy Implementation in
Smart Toolpost To Improve Performances. Global
Journal of Researches in Engineering (A), Volume XI,
Issue VII, Version 1.0 December, 1-10.
Rashid, M. K., (2004), Smart Actuator Stiffness and
Switching Frequency in Vibration Suppression of a
Cutting Tool, Smart Materials and Structures, Vol.13:
1-9.
Zhang, G., Ko, W., Luu, H., and Wang, X. W., (1995),
Design of a smart Tool Post for Precision Machining,
Proceedings of the 27
th
CIRP International Seminar on
Manufacturing Systems, Ann Arbor, MI, 157-164.
Zienkiewicz, O. C., and, Taylor, R. L., (2001), The Finite
Element Method, Fifth edition Vol.1: The Basis,
Butterworth-Heinemann.
Implementation of Cognitive Chips in Machining Error Attenuation
267