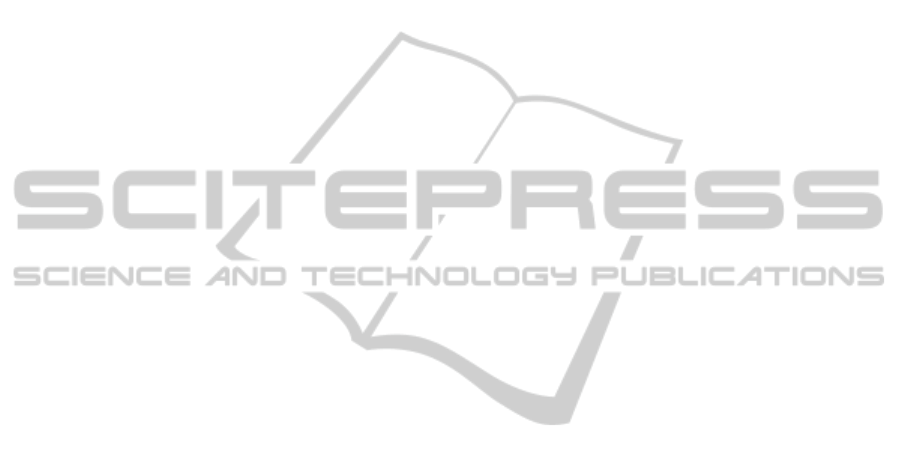
6 CONCLUSIONS
Studies on the process of information technology
acquisition (Davis et al, 1994) clearly show that
these systems go through several evolutionary stag-
es. During this development the priority in order to
succeed doesn’t seem to be tied only to the acquisi-
tion process, but mainly to the paths of learning and
organizational change. Experience suggests that
these paths should be designed and carefully man-
aged in order to allow the acquisition and effective
use of ICT applications by the users and the whole
enterprise. The traditional methodology for the train-
ing, in fact, results incomplete to furnish a suitable
medium in the professional training field, because of
dynamic and continuous changes in the ICT sector
and the increasing demand of knowledge more and
more in the quality field (Casalino, D’Atri et al.,
2005). AutoMatic can contribute to the success of
the SMEs. The strategy is based on the creation of a
system for the training that meets the distance learn-
ing with the traditional benefits; therefore the two
different methodologies are integrated. In fact, on
one side the distance statement is a comfortable
method for the training of a vast entourage of people
within automation but, on the other hand a lot of
people doesn’t believe in the effectiveness of such
method of statement because of the lack of a teacher
that mostly involves the trainees. This research pro-
ject includes the analysis of some indicators and
specific key aspects that regard the current situation
of automation and innovation culture in the Europe-
an SMEs. These are:
• what is the current situation of quality aspects
dissemination through on-line courses?
• how are the main models used and applied?
• what role can have national agencies or institu-
tions, as the universities, on the diffusion of in-
novation culture or the implementation of auto-
mation for SMEs through both traditional and
web-based learning?
• how organizational and cultural specificities af-
fect automation implementation?
The importance of automation is increasing for the
reason that lack of quality control and assurance
systems, lack of accreditation and certification pro-
cedures, poor conformity marks, are still extremely
diffused. Such impediments are considered as major
potential and unnecessary technical barriers to trade,
especially concerning international competitiveness
and globalization. It is important to underline that
SMEs have to meet the challenges of globalization
and the new knowledge-driven economy aims.
REFERENCES
Butler, J., 1999. A practical model for technology and
innovation management, Proceedings of the Portland
International Conference on Management of Engi-
neering and Technology, PICMET, 1, pp.103-105.
Cardinal, L.B., Alessandri, T.M., Turner, S.F., 2001.
Knowledge modifiability, resources, and science-
based innovation, Journal of Knowledge Management,
Vol. 5, No. 2, pp.195-204.
Carneiro, A., 2000. How does knowledge management
influence innovation and competitiveness?, Journal of
Knowledge Management, Vol. 4, No. 2, pp.87-98.
Casalino, N., 2009. An Innovative Model of Trans-
national Learning Environment for European Senior
Civil Servants - Organizational Aspects and Govern-
ance, Proceedings 11th International Conference on
Enterprise Information Systems - ICEIS, Milan, Italy,
INSTICC, pp.148-153.
Casalino, N., D’Atri, A., Manev, L., 2007. A quality man-
agement training system on ISO standards for enhanc-
ing competitiveness of SMEs, Proc. 9th International
Conference on Enterprise Information Systems -
ICEIS 2007, June 12-16 2007, Funchal, Madeira - Por-
togallo, INSTICC, pp. 229-235.
Casalino, N., D’Atri, A., 2005. Quality, usability and
economical aspects in a medical web-based training
service, Proceedings of “The 4th IASTED Internation-
al Conference on web-based education - WBE 2005”,
Grindelwald, Swiss, ACTA Press, Vol., Zurich,
pp.304-310.
Casalino, N., Di Persio, F., 2004. Integrating medical
services, training and education: the Hermes project
platform, in ATL - Advanced Technology for Learning
Journal, ACTA Press Anaheim - Calgary - Zurich,
Vol. 1, Issue 2, pp.71-80.
Chesbrough, H., 2003. The New Business Logic of Open
Innovation, Strategy & Innovation, 1, pp.11-15.
De Marco, M., 2004. Le metodologie di sviluppo dei
sistemi informativi, Franco Angeli, Milan.
Gatti, M., 2000. I costi nel governo dell’impresa.
Strumenti di supporto dei processi decisionali, Cedam.
Jin, Z., 1999. Organizational innovation and virtual insti-
tutes, Journal of Knowledge Management, Vol. 3, No.
1, pp.75-83.
Johannessen, J. A., Olsen, B., Olaisen, J., 1999. Aspects of
innovation theory based on knowledge-management,
International Journal of Information Management,
Vol. 19, No. 2, April, pp.121-139.
Kaplan, S. M., 1999. Discontinuous innovation and the
growth paradox, Strategy and Leadership, March-
April, pp.16-21.
Kessler, E. H., Chakrabarti, A. K., 1997. Methods for
improving the quality of new product innovations,
Proceedings of the Portland International Conference
on Management and Technology, PICMET, pp.405-
408.
ICEIS2012-14thInternationalConferenceonEnterpriseInformationSystems
288