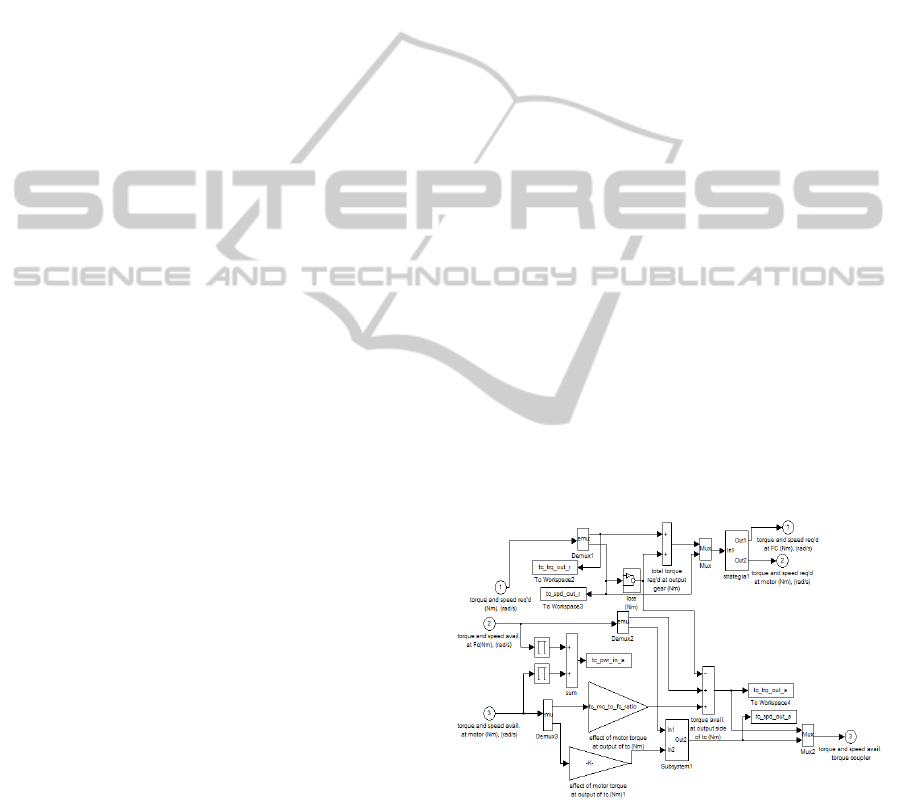
deviates from the constant power regime can be
much higher than of a motor, operating at constant
power throughout its speed range in a vehicle. In its
normal operation mode, the electric motor, can
provide constant rated torque up to its base or rated
speed. At this speed, the motor reaches its rated
power limit. The operation beyond the base speed,
up to the maximum speed, is limited to this constant-
power region. The range of this constant-power
operation depends primarily on the particular motor
type and its control strategy. An electric machine
should be able to perform a long constant-power
operation in order to be suitable for HEV
2 HYBRID ELECTRIC VEHICLE
SIZING AND CONTROL
STRATEGY IN ADVISOR
An effective HEV design requires optimal sizing of
its key mechanical and electrical components. In the
design process of an HEV, there are a range of
design variable choices, including HEV
configuration, key mechanical, electrical
components sizes, and control parameters. On the
other hand, the HEV design problem is focused at
several simultaneous objectives such as the
minimization of fuel consumption (FC) and exhaust
emissions (e.g., HC, CO, and NOx) while
maintaining driving performance. However, these
aspects are often in conflict with each other. The
minimum FC does not necessarily result in the
minimum emissions. Several approaches and
methods have been reported to optimize HEV
component sizes and control strategy parameters,
with the aim of simultaneously reducing FC and
exhaust emissions (Banvait, 2009). A parallel hybrid
powertrain is used in this paper, where two
mechanical powers are added together in a
mechanical coupler. The control strategy of a
parallel HEV is responsible for distributing the
driver’s required torque between the IC engine and
electric motor while sustaining a charge in the
batteries. The IC engine is the primary power plant,
and the batteries and the electric motor drive
constitute the energy bumper. Both IC engine and
electric motor may deliver power to the vehicle
wheels. In addition, the electric motor may also be
used as a generator to charge the battery by either
regenerative braking or absorbing the excess power
from the engine when its output is greater than the
output required to drive the wheels. For simulations,
it was used ADVISOR 2003 and Matlab 2011. In
order to reduce the fuel consumption, less required
torque from the ICE was calculated in the control
strategy, and more required torque from electric
motor. In ADVISOR the cumulative fuel use (CFU),
expressed in Laplace is calculated like below:
CFU = 1/s*x*3.785*231/r*61.02
where r is the fuel density (749), and x is the fuel
use (FU), measured in L/s. 1/s means that the
function is integrated.
FU=y*(0.1*pow((m-n)/(m-20), 0.65)+1)
where y is the hot fuel use (HFU), m is the
engine coolant thermostat set temperature(96 Celsius
degrees), and n is the coolant temperature. HFU is
obtained from a 2-D lookup table with the inputs
arguments: fc_map_spd (speed map), and
fc_map_trq (torque map). The torque available (T)
from the ICE is calculated as below:
T=max(min[(Tr+Ei), maxt], Tcl)-Ei
where Tr is the required torque, Ei is the engine
inertia, maxt is the maximum torque required, and
Tcl, is the torque when the throttle is closed. In the
torque coupler block in Advisor, the needed power
from the driver is divided between the requested
power from the ICE and the requested power from
the motor. The inputs in the torque coupler bloc are:
torque and speed required, torque and speed
available from the ICE, and torque and speed
available from the electric motor (EM).
Figure 1: Torque Coupler in Advisor.
The outputs are torque and speed available at
torque coupler, torque and speed required from ICE,
and the required torque and speed from EM. Torque
available at torque coupler (Ta) is the sum of the
torque available from the ICE and EM, minus the
losses in this bloc, because of the friction force.
ICINCO 2012 - 9th International Conference on Informatics in Control, Automation and Robotics
544