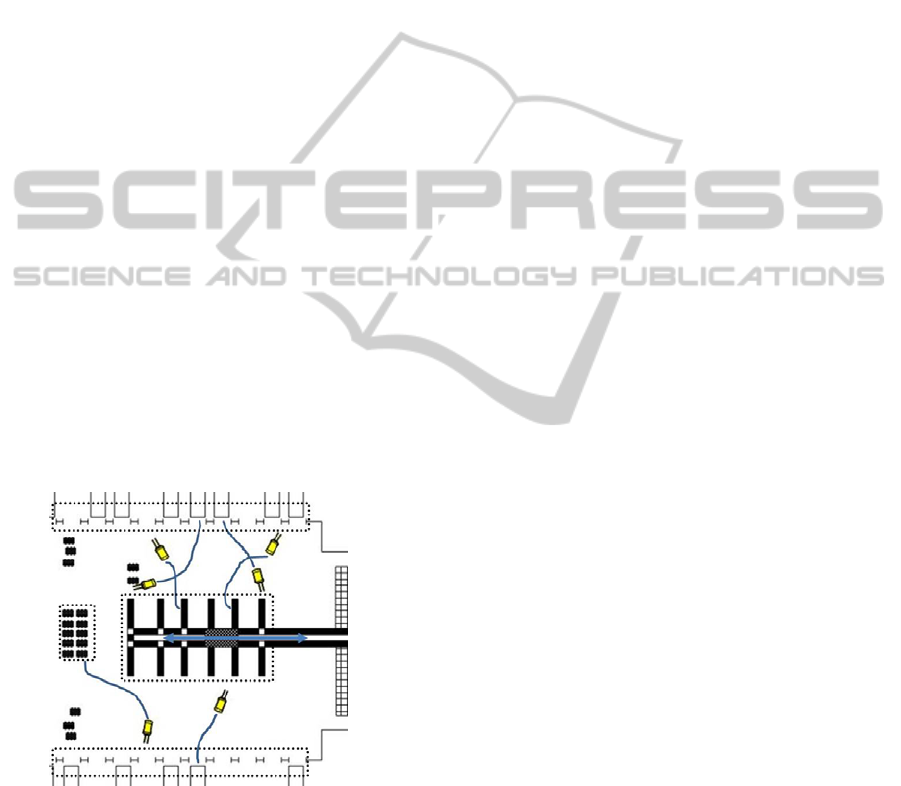
of each package. Path is an accumulation of the
positions where a TO was detected. To steer the
transport in the warehouse, there are also planned
paths in the digital representation. For controlling
purpose the planned and the actual path can be
compared. The real world consists of multiple
warehouses that interact with each other by
conveyors that transport goods. Each warehouse has
its own representation of the transportation process.
A warehouse has internal and external conveyors to
transport goods within, to, or from a warehouse.
The conveyors and sensors within a warehouse
provide information about the current status of the
transportation process. This information is used to
build a digital representation of the real world
transportation process.
3.2.2 System Model
The system model is an instance of the model
structure and contains detailed information about all
identified components involved in the analysed
process. An example of a system model is a special
warehouse layout, with conveyors and sensors at
defined positions with a defined behaviour. In
general, such models are used to abstract from the
complex real world using the outcome of the process
analysis. In our methodology the model instance is
the basis for the reliability evaluation, described in
section 3.3. The content of the model depends on a
specific system, as illustrated in figure 2.
Figure 2: An Example Warehouse Layout.
The warehouse consists of forklifts, several belt
conveyor modules, packages, sensors and storage
space. Each conveyor has its own behaviour that
must be modelled to represent the material flow.
Also sensors have their own behaviour, because
different sensors detect different events with
different accurateness.
Sensors in the real world are not perfect. The use
of sensors is always related to failures and
restrictions. Typical restrictions are temperature,
humidity or light restrictions where the sensor
measurements contain errors. But also under ideal
conditions sensors are not perfect. In order to
evaluate the reliability and observability of the
material flow, the sensors play a major role.
3.3 Reliability Evaluation Phase
In (Laprie, 2001) the reliability is defined as the
”continuity of correct service”. Continuity means
that the reliability requirement applies to the whole
runtime. Correct service in our context stands for the
consistency between real world and representation.
”The validity of the reliability analysis of a system is
directly related to the validity of the model used to
represent the system” (Allan, 1992). In (Allan, 1992)
there are two main categories of reliability
evaluation techniques: analytical and simulation. A
popular analytical technique in research and
industrial practice is model checking (Clarke, 1999).
These complementary techniques are compared in
(Harris, 2006). It has been shown that simulation is
not complete in terms of error detection and model-
checking is vulnerable to state explosion problems in
complex systems. Therefore, simulation is the
common technology to analyse complex
transportation processes in the logistics. These can
be classified as dynamic, deterministic and discrete
(Law, 2000). After a model has been analysed by
simulation or model-checking, we evaluate the
actual reliability in the process. In (Allan, 1992) one
tool for reliability evaluation is probability theory
which helps to transform knowledge of the system
into a prediction of its likely future behaviour. In our
case we examine the components involved in the
transfer between real world and representation in
order to reveal errors and to distinguish the
probability for an error of a component. When all
components are described with probability theory,
the relation between components and the process is
known, then the reliability evaluation of the
components can be expanded to the whole system,
for instance by quantitative fault tree analysis.
We derive reliability from observability. This
means that the material flow is reliable when we
observe at any time any package within the material
flow. Also with a high degree of observability we
cannot exclude failures during the material flow, but
the system is able to recognise failures at the time
they appear. This recognition is done by sensors at
the spots where packages are transferred between
conveyors. At these spots the system compares the
digital representation with the real world. But as
ICINCO2012-9thInternationalConferenceonInformaticsinControl,AutomationandRobotics
550