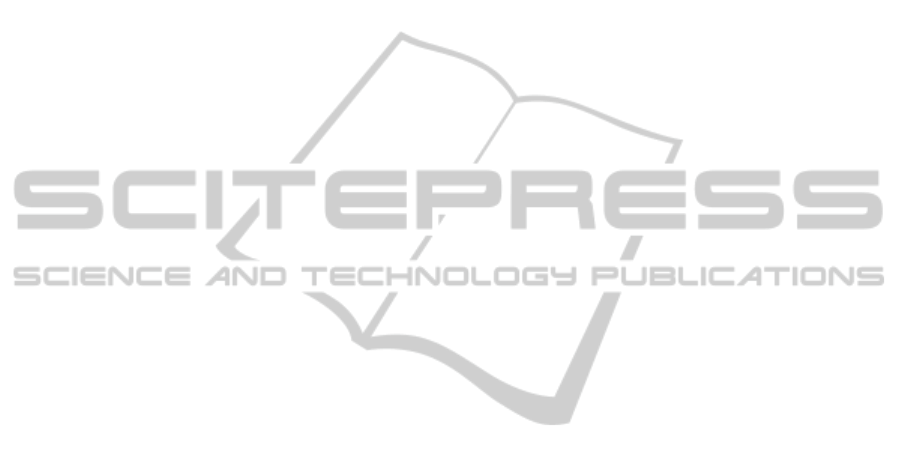
processes and dispatches information to all other
nodes over the network.
Historian Server. It has the responsibility to store
each data received from field devices through the
Application Engine. All events are recorded in its
optimized database in order to build a historical
base and retrieve them later for statistical and per-
formance computations.
ERP. It represents the contact point with business in-
telligence systems used at higher levels in the en-
terprise. The system downloads work orders from
the ERP and puts back results and statistics.
A key element to integrate new and legacy equip-
ment in the architecture is the introduction of a state
model according to one or both the standards previ-
ously discussed in the control software of each ma-
chine, so as to enable full interaction with the MES.
We have undertaken the effort to implement such
compatibility layer for a number of machines in-
volved in several packaging lines, thereby enabling
their integration into full Line Information Systems.
We claim that this effort is well worth given the po-
tential developments that it makes possible.
A system architecture like the one presented above
brings several advantages, due to the deep integration
among its components, floor plant and upper business
intelligence level. This integration makes possible a
bidirectional communication between involved actors
as well as the ”historicization” of all information re-
lated to the plant activities. Thus, the system permits
full supervision of process and machines, automat-
ing many procedures and doing computations over
data. From the enterprise management point of view,
this means to have a “plant dashboard” showing an
overview of the plant available 24Hx7D and popu-
lated with real time data. This dashboard enables pro-
duction planning and helps in justifying, or more pre-
cisely understanding, factory performance (e.g. from
OEE factors). Likewise, at a lower logical level, line
managers can monitor their lines from a single con-
trol point as well as be assisted in identifying trouble
sources and get reminded of planned maintenance op-
erations.
5 CONCLUSIONS
The issues discussed in this paper provide evidence of
the revolution that is currently in progress in the F&B
packaging domain, regarding line control and ma-
chine coordination. Although this revolution started
several years ago, only now an overall view of the
most innovative market players shows a new model of
plant organization, that is also affecting those who are
less caring at these issues. One can’t help but notice
that the evolution in packaging lines, from electrome-
chanical, to software-based controls, to mechatronic
systems, has several similarities with the techology
evolution in the ICT domain. In the same way in-
formation systems use middleware services for coor-
dinating actions in distributed environments, packag-
ing industries are now ready to move to fully super-
vised factories that exploit MES as core components
to bridge the gap between shop-floor and business lev-
els. In F&B packaging, adopting sound representa-
tional and communication standards at the machine
level has proven to be a key enabling step for MES-
based production and supervision.
ACKNOWLEDGEMENTS
The research and development described in this pa-
per has been carried out in the framework of the col-
laborative effort IntegraPack (www.integrapack.it),
partially funded and supported by Regione Emilia-
Romagna, Italy. We thank the many people who have
contributed to the issues and developments outlined
in the paper.
REFERENCES
Bratukhin, A. and Sauter, T. (2010). Bridging the gap be-
tween centralized and distributed manufacturing exe-
cution planning. In ETFA, 2010, pages 1–8.
ISA (2008). Machine and unit states: An implementation
example of ISA-88. Technical report, ISA.
Kather, A. and Voigt, T. (2010). Weihenstephan standards
for production data acquisition in bottling and packag-
ing plants, general part. Technical report, Technische
Universit
¨
at M
¨
unchen. Version 2005.03.
MESA (1997). MES explained: A high level vision. In
MESA White Paper 6. MESA International.
Qiu, R. and Zhou, M. (2004). Mighty mess; state-of-the-art
and future manufacturing execution systems. Robotics
Automation Magazine, 11(1):19–25, 40.
Ricken, M. and Vogel-Heuser, B. (2010). Modeling of man-
ufacturing execution systems: An interdisciplinary
challenge. In ETFA, 2010, pages 1–8.
Soplop, J., Wright, J., Kammer, K., and Rivera, R. (2009).
Manufacturing execution systems for sustainability:
Extending the scope of MES to achieve energy effi-
ciency and sustainability goals. In ICIEA 2009, pages
3555–3559.
Younus, M., Peiyong, C., Hu, L., and Yuqing, F. (2010).
MES development and significant applications in
manufacturing -a review. In ICETC, 2010, volume 5,
pages 97–101.
ICINCO2012-9thInternationalConferenceonInformaticsinControl,AutomationandRobotics
556