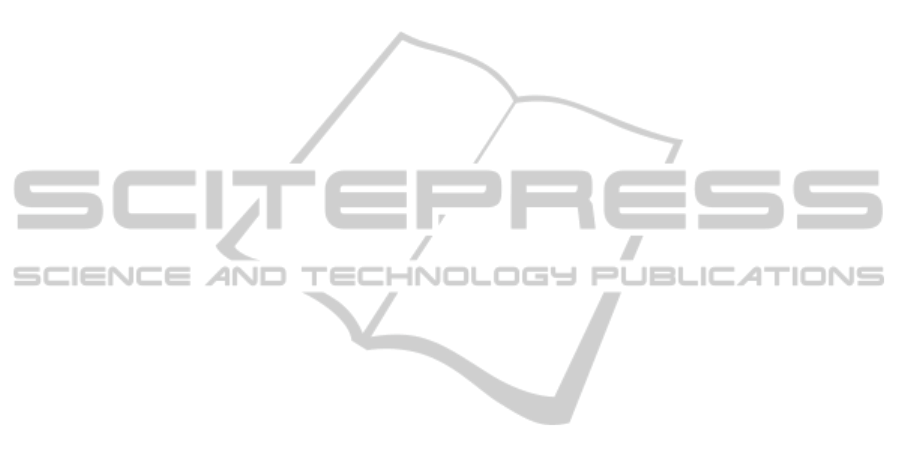
and sometimes just because they lost a site contract
or other reason.
In money terms, they have won £1,210,698.84
worth of quotes this year and lost £6,443,682.82
worth of quotes, £1,438,105.66 of them due to
inaccurate pricing, which were taken over by our
competitors’. Analysing the lost quotes due to
prices, and redoing them again through the ERP
system, a number of errors were found, but most
importantly out of 82 quotes lost due to prices, 56
were estimated with lower prices from what the
estimator sent to customer, 17 were underestimated
due to un tracking the price changes, and 9 quotes
files were unfound. No patterns were found for the
results because of the un-systematic approach the
estimator use, and asking the estimator, it was found
that some quotes were raised in price to make a
balance in some other lost jobs or mistakes done in
jobs, the exact example was: “I was quoting a
customer’s quote and I received a phone call about a
door at a customer site with a faulty meaning we
have to remake the door from scratch and to make it
up for the loss I’ve added around £200 to this
quote”, Company MD. This unsystematic approach
has been causing the company losses in both quotes
stage and job stage of the company work process.
6 FINDINGS FROM CASE STUDY
There are few questions to be asked in order to
verify the results of the implementation:
Can you observe productivity in your planning
area few months after ERP implementation? Do
things which have been assumed as complex before
implementation seem very simple after
implementation? Can you now control your budget,
stocks etc? Have you not stopped your and
customer's production lines because of material
shortage due to better planning system?
A successful ERP implementation in any case
study needs to fulfil these arguments. At the case
study, live prices are used for quotes, which if
accepted and turned into sales orders, transferring
them easily into a job that can automatically alert the
purchasing department of what needs to be
purchased for this jobs, updating quantities,
scheduling a job for the shop floor, tracking it
through the work, being able to determine job stages
and update customers, has been accomplished, and
made creating a job file much easier than previously
as each file use to be typed manually into excel
sheets, paper work. The case study was able to
overcome a number of barriers to the
implementation and can feel a financial difference in
the quotes sent to customers, which help in losing
fewer customers and with increasing the
productivity of the company.
7 CONCLUSIONS AND FUTURE
WORK
A successful ERP implementation is based on the
understanding and clarity of the processes and work
flow through the various departments in the
organization. It also depends on the support
employees get when using the system, especially
from top management. There were many barriers to
successful implementation, many of which were not
predicted. Bani-Hani et al. described these focusing
on the difficulty of persuading many of the
employees that the ERP system could make their job
easier and more successful.
This paper was able to identify the costs and
benefits from the ERP system, and what difference it
can make to the financial status of the company if
used properly. In fact the improvement in accuracy
played a major part in convincing the management
of the value of the system. It was also clear that
there is a critical mass of support that is necessary to
persuade management to adopt the improved
procedures.
REFERENCES
Esteves J. M., Pastor J. A. (1999) “An ERP Life-Cycle-
based Research Agenda”, First international
workshop in Enterprise management and resource
panning: Methods, Tools and Architecture _
EMRPS’99, Venice, Italy.
Shahnorbanun Sahran, Feybi Ariani Goni, Muriati
MukhtarSahran, (2010) “ERP Implementation
Challenges in Small and Medium Enterprise: A
Framework and Case Study”, Advanced Materials
Research (Volumes 139 - 141).
Sanna Laukkanen, Sami Sarpola, Petri Hallikainen (2005),
“ERP System Adoption - Does the Size Matter?”
Proceedings of the 38th Hawaii International
Conference on System Sciences – 2005.
Chuck C. H. Law, Eric W. T. Ngai (2007), “ERP systems
adoption: An exploratory study of the organizational
factors and impacts of ERP success”, Information &
Management, Volume 44, Issue 4, June 2007, Pages
418-432.
Paul Bocij, Andrew Greasley, Simon Hickie (2006)
“Business information systems: technology,
development and management” Book By Paul Bocij,
Andrew Greasley, Simon Hickie
KMIS2012-InternationalConferenceonKnowledgeManagementandInformationSharing
288