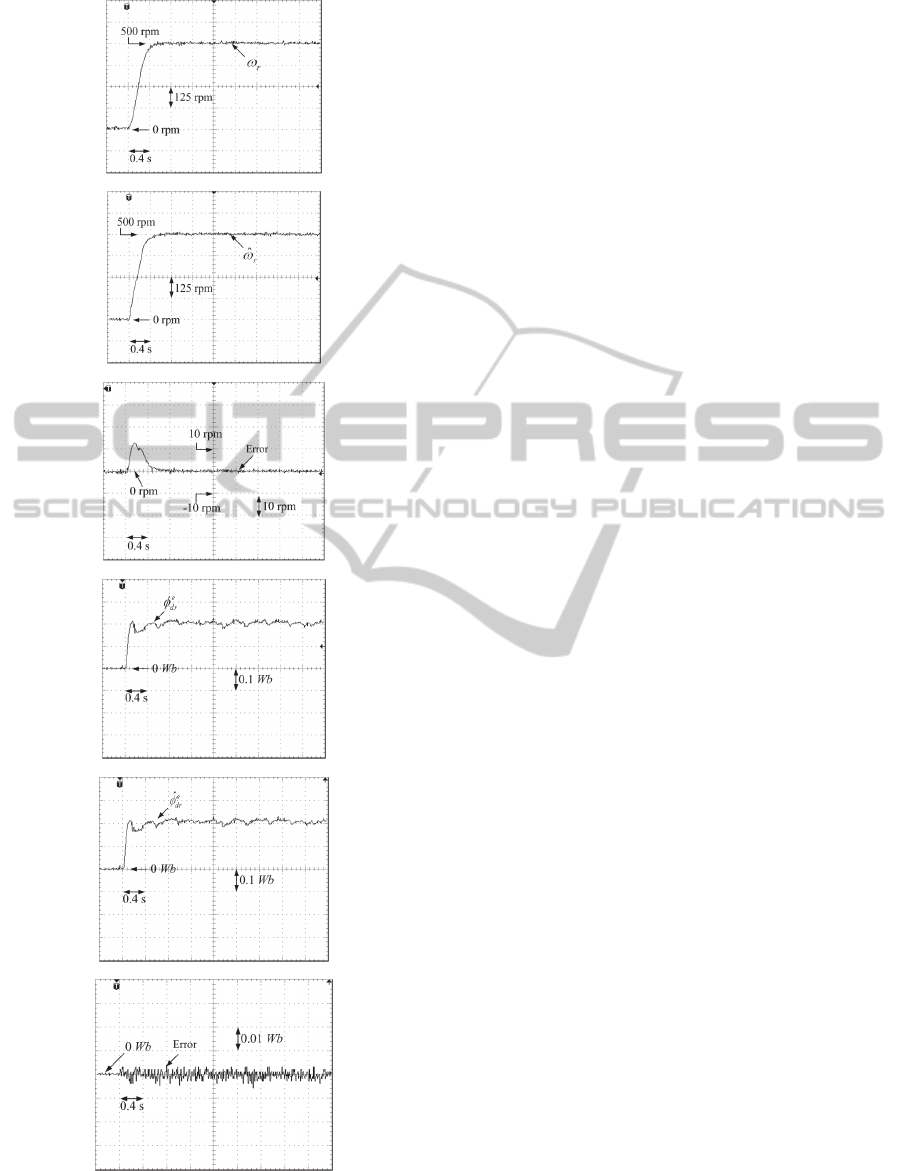
(a) Actual motor speed response
(b) Estimated motor speed response
(c) Speed error
(d) Actual d-axis rotor flux
(e) Estimated d-axis rotor flux
(f) The d-axis rotor flux error
Figure 6: Experimental results for speed command of 500
rpm.
ACKNOWLEDGEMENTS
The authors would like to express their appreciation
to NSC for supporting under contact NSC 100-2218-
E-168 -004.
REFERENCES
Angelo, C. D., Bossio, G., Solsona, J., Garcia, G. O.,
Valla, M. I., 2006. Mechanical Sensorless Speed
Control of Permanent-Magnet AC motors Driving an
Unknown Load.
IEEE Transactions on Industrial
Electronics, vol. 53, no. 2, pp. 406-414
.
Perera, P. D. C., Blaabjerg, F., Pedersen, J. K., Thogersen,
P., 2003. A Sensorless Stable V/f Control Method for
Permanent-Magnet Synchronous Motor Drives
. IEEE
Transactions on Industry Applications, vol. 39, no. 3,
pp. 783-791
.
Singh, G. K., Singh, D. K. P., Nam, K., Lim, S. K., 2005.
A Simple Indirect Field-Oriented Control Scheme for
Multiconverter-Fed Induction Motor.
IEEE
Transactions on Industrial Electronics, vol. 52, no.6,
pp. 1653-1659
.
Consoli, A., Scarcella, G., Testa, A., 2004. Slip-Frequency
Detection for Indirect Field-Oriented Control Drives.
IEEE Transactions on Industry Applications, vol. 40,
no. 1, pp. 194-201
.
Kwon, T. S., Shin, M. H., Hyun, D. S., 2005. Speed
Sensorless Stator Flux-Oriented Control of Induction
Motor in the Field Weakening Region Using
Luenberger Observer.
IEEE Transactions on Power
Electronics, vol. 20, no. 4, pp.864-869
.
Zhen, L., Xu, L., 1998. Sensorless Field Orientation
Control of Induction Machines Based on a Mutual
MRAS Scheme.
IEEE Transactions on Industrial
Electronics, vol. 45, no. 5, pp. 824-831
.
Lascu, C., Boldea, I., Blaabjerg, F., 2004. Direct Torque
Control of Sensorless Induction Motor Drives: a
Sliding-Mode Approach.
IEEE Transactions on
Industry Applications, Vol. 40, No. 2, pp. 582-590
.
Kim, S. H., Park, T. S., Yoo, J. Y, Park, G. T., 2001.
Speed-Sensorless Vector Control of an Induction
Motor Using Neural Network Speed Estimation,”
IEEE Transaction on Industrial Electronics, vol. 48,
no. 3, pp. 609-614
.
Chen, T. C., Ren T. J., Lou, Y. W., 2011. Design of
recurrent fuzzy neural network and general regression
neural network controller for traveling-wave ultrasonic
motor.
International Conference on Neural
Computation Theory and Applications (NCTA2011),
Paris, France, Oct. 24-26
.
Bose, B. K., 1986.
Power Electronics and Ac Drives,
Prentice-Hall, Englewood Cliffs.
InductionMotorSpeedControlusingFuzzyNeuralNetworkSpeedEstimation
625