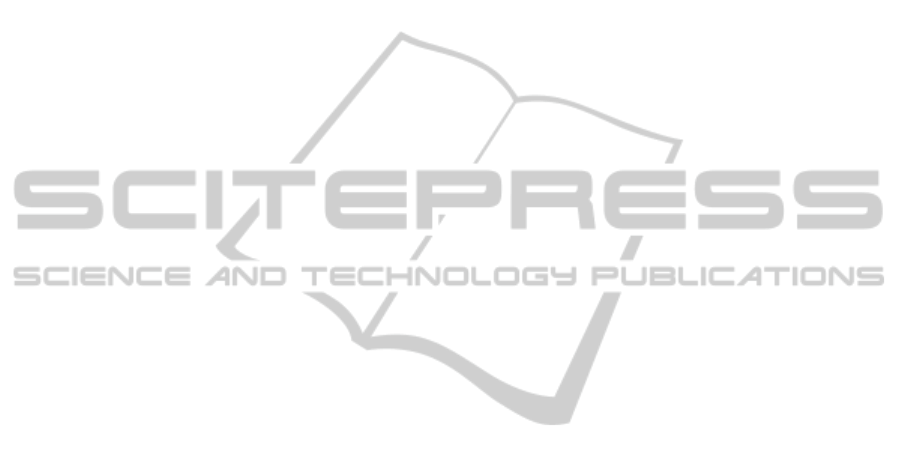
mapping technique. The space mapping correction is
applied both to the objectives and the constraints, en-
suring zero-order consistency and a perfect alignment
between the surrogate and the high-fidelity model. To
our knowledge, this is the first application of the space
mapping methodology used in conjunction with low-
fidelity approximation models in aerodynamic shape
optimization. The proposed approach performs well
and optimized designs are obtained using only a few
high-fidelity model evaluations.
ACKNOWLEDGEMENTS
This work was funded by The Icelandic Research
Fund for Graduate Students, grant ID: 110395-0061.
REFERENCES
Abbott, I. and Von Doenhoff, A. (1959). Theory of wing
sections: including a summary of airfoil data. Dover.
Alexandrov, N. and Lewis, R. (2001). An overview of first-
order model management for engineering optimiza-
tion. Optimization and Engineering, 2(4):413–430.
ANSYS (2010). ANSYS FLUENT Theory Guide. AN-
SYS, Southpointe 275 Thecnology Drive Canonburg
PA 15317, release 13.0 edition.
Bandler, J., Cheng, Q., Dakroury, S., Mohamed, A., Bakr,
M., Madsen, K., and Sondergaard, J. (2004). Space
mapping: the state of the art. Microwave Theory and
Techniques, IEEE Transactions on, 52(1):337–361.
Echeverria, D. and Hemker, P. (2005). Space mapping and
defect correction. Computational Methods in Applied
Mathematics, 5(2):107–136.
Forrester, A. and Keane, A. (2009). Recent advances in
surrogate-based optimization. Progress in Aerospace
Sciences, 45(1-3):50–79.
Haikin, S. (1998). Neural Networks: A Comprehensive
Foundation. Prentice Hall.
Journel, A. and Huijbregts, C. (1978). Mining geostatistics.
Academic press.
Koziel, S., Cheng, Q., and Bandler, J. (2008). Space map-
ping. Microwave Magazine, IEEE, 9(6):105–122.
Koziel, S., Ciaurri, D. E., and Leifsson, L. (2011).
Surrogate-based methods. In Computational opti-
mization and applications in engineering and indus-
try, volume 359. Springer.
Koziel, S. and Leifsson, L. (2012). Knowlegde-based air-
foil shape optimization using space mapping. In 30th
AIAA Applied Aerodynamics Conference.
Leifsson, L. and Koziel, S. (2011a). Airfoil shape opti-
mization using variable-fidelity modeling and shape-
preserving response prediction. In Comp. Opt., Meth-
ods and Algorithms, volume 356. Springer.
Leifsson, L. and Koziel, S. (2011b). Variable-fidelity aero-
dynamic shape optimization. In Comp. Opt., Methods
and Algorithms, volume 356. Springer.
Minsky, M. and Papert, S. (1969). Perceptrons: An intro-
duction to computational geometry. The MIT Press,
Cambridge, MA.
NASA (2008). Onera-m6-wing validation case. In
http://www.grc.nasa.gov.
O’Hagan, A. and Kingman, J. (1978). Curve fitting and
optimal design for prediction. Journal of the Royal
Statistical Society. Series B (Methodological).
Queipo, N., Haftka, R., Shyy, W., Goel, T., Vaidyanathan,
R., and Kevin Tucker, P. (2005). Surrogate-based anal-
ysis and optimization. Progress in Aerospace Sci-
ences, 41(1):1–28.
Raymer, D. (2006). Aircraft design: a conceptual approach.
American Institute of Aeronautics and Astronautics.
Robinson, T., Willcox, K., Eldred, M., and Haimes,
R. (2006). Multifidelity optimization for variable-
complexity design. In Proceedings of the 11th
AIAA/ISSMO Multidisciplinary Analysis and Opti-
mization Conference, Portsmouth, VA.
Schmitt, V. and Charpin, F. (1979). Pressure distributions
on the onera-m6-wing at transonic mach numbers. Ex-
perimental Data Base for Computer Program Assess-
ment, Report of the Fluid Dynamics Panel Working
Group 04, AGARD AR 138, May 1979.
Simpson, T., Poplinski, J., Koch, P., and Allen, J. (July
2001). Metamodels for computer-based engineering
design: survey and recommendations. Engineering
with computers, 17(2):129–150.
Smola, A. and Sch
¨
olkopf, B. (2004). A tutorial on sup-
port vector regression. Statistics and computing,
14(3):199–222.
Søndergaard, J. (2003). Optimization using surrogate mod-
els by the space mapping technique. PhD thesis, PhD.
Thesis, Technical University of Denmark, Informatics
and mathematical modelling.
Tannehill, J., Anderson, D., and Pletcher, R. (1997). Com-
putational fluid mechanics and heat transfer. Taylor
& Francis Group.
Wild, S., Regis, R., and Shoemaker, C. (2008). Orbit:
Optimization by radial basis function interpolation in
trust-regions. SIAM Journal on Scientific Computing,
30(6):3197–3219.
Zhu, J., Bandler, J., Nikolova, N., and Koziel, S. (2007).
Antenna optimization through space mapping. An-
tennas and Propagation, IEEE Transactions on,
55(3):651–658.
SIMULTECH 2012 - 2nd International Conference on Simulation and Modeling Methodologies, Technologies and
Applications
498