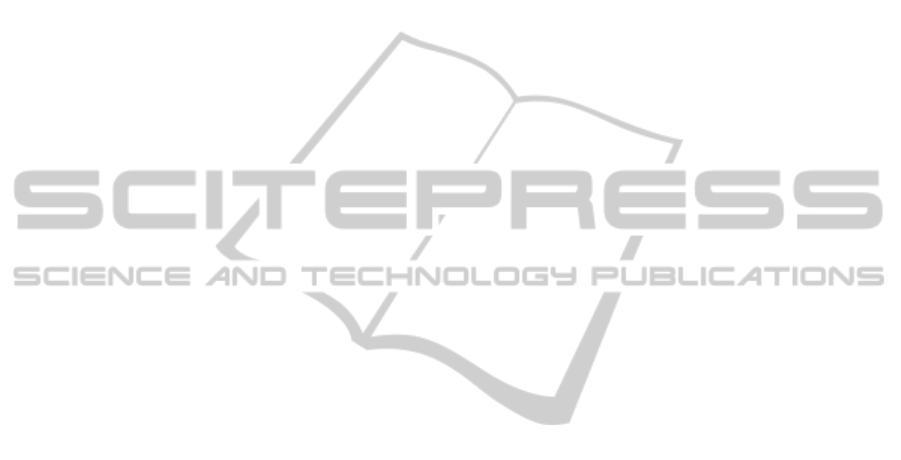
properties of the egg, i.e. the mass and stiffness of the
shell, the mass of the egg yolk, etc.
Since passive observation of an object is not suf-
ficient for estimation of its physical properties, an ac-
tive interaction is required. We adapt the analogy of a
widely used ’Black Box’ technique in system identi-
fication. We give an initial impulse to the object and
estimate its internal parameters from the resulting re-
sponse based on its external geometry and total mass.
In this paper, we present a vision based grasp-
less approach for estimating the center of mass and
the mass distribution. We use a bottom-up technique,
where we make an initial assumption about the cen-
ter of mass based on the external 3D geometry of the
object. This is used to compute possible points of in-
teraction between the robot and the object. We cor-
rect the center of mass by analyzing the observed ro-
tational motion (Fig. 1) resulting from the interaction,
and use it together with knowledge of total mass and
the external 3D geometry of the object to estimate the
mass distribution (Fig.2).
2 RELATED WORK
Most of the approaches for estimation of physical
properties of the objects require some direct interac-
tion between the robot and the object. These interac-
tions can be of various types, such as poking, striking,
tilting, grasping, etc. We break down the information
resulting from these interactions into three categories:
acoustic, visual (spatial/angular motion), and tactile.
In (Frank et al., 2010) a method for robot navi-
gation in an environment with deformable objects is
introduced, where the robot estimates the stiffness of
the object based on the tactile and visual information
acquired from poking. Femmam et al. (Femmam
et al., 2001) and Krotkov et al (Krotkov et al., 1995)
present an approach for characterizing the material of
the object based on its internal friction. Here they use
the acoustic information acquired from striking the
object. However, since the material type defines only
its molecular properties for the purpose of manipu-
lation this information is not sufficient. In (Krotkov,
1995) authors use both the visual and acoustic infor-
mation from strike to first estimate the mass of the ma-
terial then the type. Nevertheless the questions con-
cerning the mass distribution, and the center of mass
remain unresolved. Tanaka et al. (T.Tanaka et al.,
2003) introduce a method for constructing a reality
based virtual simulator. They use as input parameters
the mass and elasticity of the object, which are ex-
tracted from visual and tactile information acquired
by pushing. Here as well the extracted information
remains insufficient for purposes of object manipula-
tion. Yu et al. (Yu et al., 1999) present an approach
for estimating the mass and center of mass of the ob-
ject with previously unknown shape. For this, the au-
thors use tactile information acquired from tilting the
object from several points. However, the position of
the tilting points, and the stability of the tilts are not
addressed.
Our method uses the visual information acquired
while striking the object to estimate the center of
mass, the mass distribution, and the moment of inertia
of the object based on the given mass and the external
3D structure of the object. Thus it fills the gap in the
information required for object manipulation.
In Section 3, we describe our approach for esti-
mating the physical properties of the object. This sec-
tion is divided into three logical subsections:
• 3D model analysis (Sec. 3.1), where we com-
pute the robot/object interaction points based on
the appearance of the object.
• Estimation of the center of mass (Sec. 3.2), where
the center of mass is computed based on the pro-
file of the observed angular motion of the object.
• Estimation of mass distribution (Sec. 3.3), where
the mass distribution is computed based on the
profile of angular motion of the object and the
center of mass.
In Section 4, we describe the conducted experi-
ments, the experimental setup (Sec. 4.1), provide an
error sensitivity analysis of the approach (Sec. 4.2)
and present the results (Sec. 4.3, 4.4). We conclude
in section 5.
3 APPROACH
Our approach allows us to estimate physical proper-
ties, such as center of mass (CoM), moment of inertia
(MoI), and mass distribution of objects with unknown
internal structure. We require the mass m which could
be acquired by means described in (T.Tanaka et al.,
2003), (Krotkov, 1995) and the 3D model of the ex-
terior of the object, i.e the point cloud P = {p
i
} that
represents the surface of the mentioned object. This
can be acquired by laser scanner, stereo reconstruc-
tion, etc., as an input (Fig 2). By analyzing the 3D
point cloud (Sec. 3.1.1), we define possible points of
rotation (Sec. 3.1.2) around which we desire the ob-
ject to be rotated (Fig. 1). Later, we compute the cor-
responding interaction points (Sec. 3.1.3) that are the
places where the object should be struck by a robot to
achieve the desired rotation. The latter is defined as
VisualEstimationofObjectDensityDistributionthroughObservationofitsImpulseResponse
587