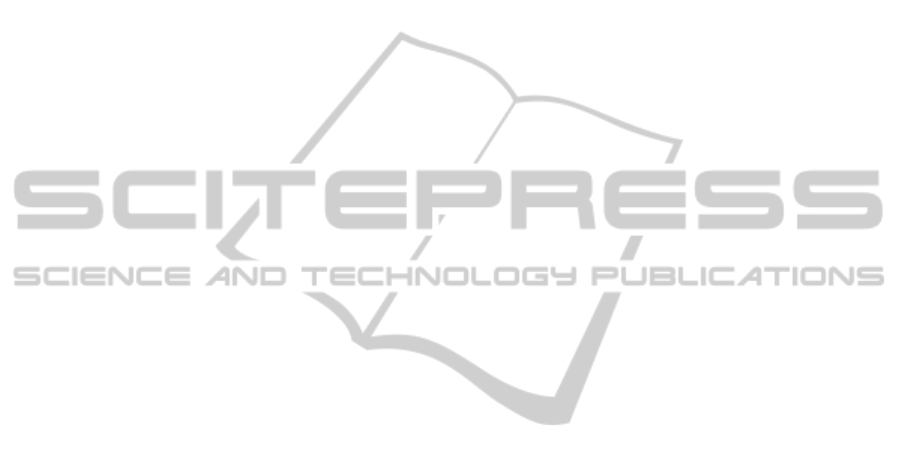
increases by 7%. These results are justified by the
importance of lumber demand that represents almost
80% of the total network demand. Thus, it becomes
essential to plan the supply chain efficiently in order
to deliver the right product to the right customer
with the right quality. By managing quality
standards (freshness) it becomes also possible to
offer a more advantageous and stable price.
6 CONCLUSIONS
This article proposes an integrated model to plan
supply chain operations for the forest industry while
considering key constraints related to the freshness
of the wood fibre. In particular, we analyze a case
study, which includes four sawmills and one paper
mill located in eastern Canada. To ensure a better
use of the wood fibre and a greater synchronization
of the network activities, the model provides
harvesting, transportation, production, and storage
plans for the forest companies of this region. The
model aims at improving the management of the
wood fibre quality while reducing the operating
costs such as storage, transportation, and processing.
The proposed model has been tested using three
different scenarios: variations of the wood freshness,
different patterns of lumber demand, and variations
of the lumber price. Results show that the wood
fibre freshness is a key criterion to consider for
increasing the benefit of the value network. On the
other hand, scenario analysis based on lumber price
and demand confirm the necessity for Canadian
forest product companies to expand their market to
avoid the effects of the relative instability of the
Canadian lumber market.
The next step will be to develop multiple models
based on a coordinated driving strategy for
addressing the fact that each company is
“independent” or autonomous. It will also be
necessary to develop some mechanisms to ensure a
fair benefit sharing generated of a better
synchronization of network members’ operations.
REFERENCES
Beaudoin, D., Frayret, J. M., LeBel, L., 2010. Negotiation-
based distributed wood procurement planning within a
multi-firm environment. Forest Policy and Economics,
vol. 12, no. 2, pp. 79–93.
Beaudoin, D., LeBel, L., Frayret, J. M., 2006. Tactical
Supply Chain Planning and Robustness Analysis in the
Forest Products Industry. Canadian Journal of Forest
Research, vol. 37, no. 1, pp. 128-140(13).
Carlsson, D., D'Amours, S., Martel, A., Rönnqvist, M.,
2006. Supply Chain Management in the Pulp and
Paper Industry. CENTOR, Working Paper, DT-AM-3.
Chang, Y. H., Weyb, W. M., Tseng. H. Y., 2009. Using
ANP priorities with goal programming for
revitalization strategies in historic transport: A case
study of the Alishan Forest Railway. Expert Systems
with Applications, vol. 36, no. 4, pp. 8682–8690.
D’Amours, S., Frayret, J. M., Rousseau, A., 2004. De la
forêt au client – Pourquoi viser une gestion intégrée
du réseau de création de valeur ? Université Laval,
FORAC, CENTOR, Document de travail.
Forest Products Association of Canada (FPAC)., 2011.
Industry by the number. Key economics facts.
Gaudreault, J., Frayret, J. M., Pesant, G., 2009. Distributed
search for supply chain coordination. Computers in
Industry, vol. 60, no. 6, pp. 441–451.
Horne, C. V., Frayret, J. M., Poulin, D., 2006. Creating
value with innovation: From centre of expertise to the
forest products industry. Forest Policy and
Economics,vol. 8, no. 7, pp. 751–761.
Lehoux, N., D’Amours, S., Langevin, A., 2008.
Collaboration et coordination dans les réseaux, une
revue des travaux clés. CIRRELT-2008-51.
Lehoux, N., D’Amours, S., Frein, Y., Langevin, A., Penz,
B., 2011. Collaboration for a two-echelon supply
chain in the pulp and paper industry: the use of
incentives to increase profit. Journal of the
Operational Research Society, vol. 62, pp. 581-592.
Maness, T. C., Norton, S. E., 2002. Multiple Period
Combined Optimization Approach to Forest
Production Planning. Scandinavian Journal of Forest
Research, vol. 17, no. 5, pp. 460-471.
Martel, A., 2003. Le pilotage des flux : concepts de base et
approches contemporaines. DF-3.1.1. La conception
de réseaux logistiques. CENTOR, Université Laval.
Ministère des ressources naturelles, de la faune et des
parcs, direction régionale de la Côte-Nord (MRNFP).,
2004. Région de la Côte-Nord. Document
d’information sur la gestion de la forêt publique.
Mirdamadi, S., Dupont, L., Fontanili, F., 2009.
Modélisation du processus de pilotage d’un atelier en
temps réel à l’aide de la simulation en ligne couplée à
l’exécution. Thèse de doctorat. Institut National
Polytechnique de Toulouse.
Suzanne, T., Roy, D. S., Ari-Pekka, H., 2004. From supply
chain to demand chain: the role of lead time reduction
in improving demand chain performance. Journal of
Operations Management, vol. 21, no. 6, pp. 613–627.
Trentesaux, D., Tahon, T., 2010. Pilotage hétérarchique
des systèmes de production. Habilitation à diriger des
recherches. L’Université de Valenciennes et du
Hainaut-Cambresis. LAMIIH. UMR CNRS 8530.
Walker, H. D., Preiss, S. W., 1988. Operational planning
using mixed integer programming. The Forestry
Chronicle, vol. 64, no. 6, pp. 485-488.
ICORES2013-InternationalConferenceonOperationsResearchandEnterpriseSystems
208