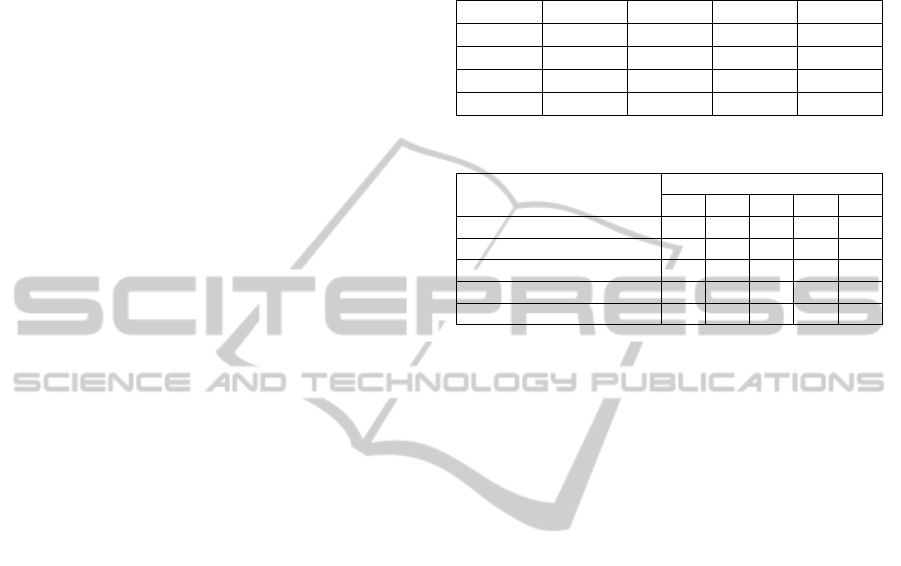
is de-fined by state of every agent. The unified
spatio-temporal scale is defined to achieve visibility
of results and unified logic: time is counted from the
start of the modeling process, i.e. from the moment
of the first order entry. The upper border of planning
is determined by the planning horizon, calculated in
days. The distances are brought to time scale by
division of the distances by the average speed. By
doing this, we can account for quality conditions and
traffic capacity of roads (that’s why longer road can
result in shorter trip due to higher speed, it allows).
Current states of agents are changing and are
measured when new orders come into the system
and at the moments of start and finish of execution
of each order. That’s why the scale of N orders in
general case consists of 3N points.
When a new order comes into the MAS-system,
a request for its allocation is sent to all the truck
agents. Then the agents analyze their current state,
availability of ’time slots‘ in the future schedule,
need for empty run to loading point, assess their pos-
sible profit and send answer to the order agent.
’Candidates‘ for re-scheduling (in case of increasing
profit) are ordered of the prospective profit. Then the
order agent chooses the truck that gives the maximal
profit. The profit is calculated as a difference
between the order revenue (price) and the order full
cost. When order implies an empty run to loading
point, its cost is also deducted from the revenue.
That’s why orders with high revenue, but long
empty runs to loading points, can be ousted by
orders with lower revenue, but without empty runs.
In case of strategy (model), where penalties are
applied, their influence on profit is analyzed. For
penalty is proportional to time of delay, the orders
with big delays will not be scheduled. Orders in the
past (earlier than the current time) do not participate
in the scheduling.
The process continues by processing of the
events of order arrival, start and finish of order
execution, simulating real-time order management.
In the process of research the above 4 models of
cargo transportation were implemented and
compared to show benefits of adaptive scheduling.
5 WORLD OF SIMULATIONS
Let’s consider world of simulations and example of
calculation of fleet profit in adaptive real time
scheduling for one truck. Let’s look at the example.
There are 4 cities (points) given, among which
the distances are determined by the matrix (see
Table 1) in days of trip. Time of trip doesn’t
necessarily correspond to the distance, because
quality of roads may be different that affects the
maximum speed of truck on the roads.
Table 1: Matrix of distances among cities.
Point 1 Point 2 Point 3 Point 4
Point 1 0 1 1 2
Point 2 1 0 2 1
Point 3 1 2 0 1
Point 4 2 1 1 0
Table 2: Parameters of orders.
Characteristics
Order number
1 2 3 4 5
Time of entry
1 3 5 6 7
Start time of execution
3 4 7 8 9
Finish time of execution
5 5 9 9 10
Where from
4 3 1 4 3
Where to
1 1 4 3 1
At the beginning of the trip the truck is located in
the point 1.
At different times cargo transportation orders #1-
5 to different points come into the system. Duration
of execution of an order is 1-2 days. Scheduling
horizon equals t = 10 days. The costs of orders are
calculated equally using company tariff as c = 3
standard units (SU) / day, i.e. 2-days trip would have
cost of 6 SU. Idle time of a truck leads to daily loss
of qa=0.3 SU. Use 15-point type for the title, aligned
to the center, linespace exactly at 17-point with a
bold font style and all letters capitalized. No
formulas or special characters of any form or
language are allowed in the title.
Daily running cost in case of empty run of truck
or order execution is q=1. Drivers are allowed to
execute orders with delays, but every day of delay
costs pp = 0.6 SU. Some orders are shifted to the
right on the time axis because of this. The aim is to
be able to schedule trips, as orders come in (the
orders are not known in advance) and calculate
profit.
Orders are marked with a number according to
the place in the sequence of entry into the system
and characterized by time of their entry (moment of
entry t), moments of start and finish of order
execution, duration (in days), point of loading and
point of unloading (Table 2).
Figure 1 shows orders as rectangles, with the
order number and the time of entry, divided by
comma inside the rectangle, above each rectangle
’where from – where to‘ locations are described. The
start and the finish of each rectangle correspond to
the start and the finish of the order execution.
ICAART2013-InternationalConferenceonAgentsandArtificialIntelligence
246