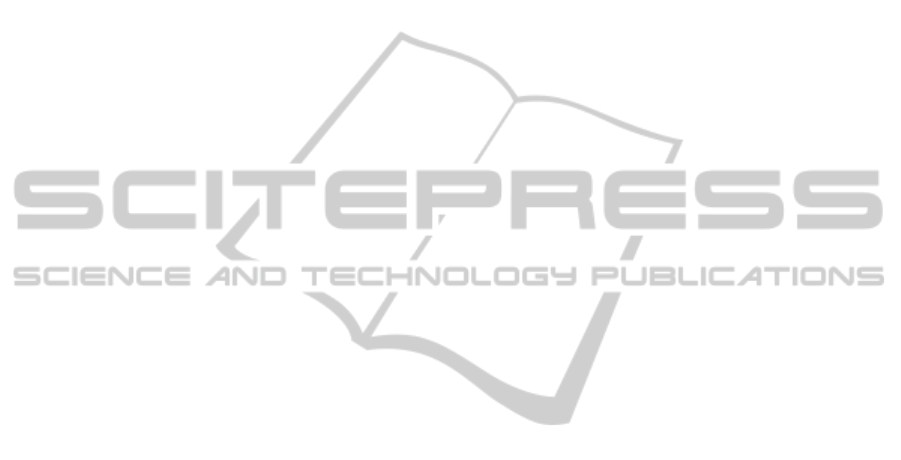
produced in human gait and running.
Parallel robots can generate dynamic forces in a
realistic and repeatable way. In this sense, realism is
improved compared to static calibration systems
(Hall et al., 1996) or dynamic systems using
mechanical devices, which do not represent real
efforts during clinical applications (Fairburn et al.,
2000); (Hsieh et al., 2011)
Moreover, the system allows programming any
kind of force in a wide range of amplitudes and
temporal patterns, which improves other manual
systems as described by other authors (Rabuffeti et
al., 2003); (Collins et al., 2009); (Cedraro et al.,
2009). The robot is able to apply cyclic repeatable
forces, allowing analyzing effects such as hysteresis
or potential drifts of the sensors.
We also propose a recalibration algorithm that
allows characterizing the sensitivity coefficients of
each sensor. The procedure is not based on a linear
recalibration matrix, but performs the calibration of
each sensor using a nonlinear model. This model
also includes a process for correcting the orientation
of the load cell used as a reference. The results
obtained show that this procedure offers better
results than some systems based on linear models.
In short, parallel robots are robust and versatile
devices able to generate dynamic load patterns
similar to the forces that appear in biomechanical
studies. Combined with a suitable calibration
algorithm, they can be very useful for dynamic
calibration of FP.
ACKNOWLEDGEMENTS
This work has been funded by the Spanish
Government and co-financed by EU FEDER funds
(Grants DPI2009-13830-C02-01, DPI2009-13830-
C02-02 and IMPIVA IMDEEA/2011/ 93).
REFERENCES
Cappello, A., D. Lenzi, D., Chiari, L., (2004). Periodical
in-situ re-calibration of force platforms: a new method
for the robust estimation of the calibration matrix.
Medical and Biological Engineering and Computing,
42, pp. 350–355.
Cappello A., Bagala, F., Cedraro, A., Chiari, L., (2011).
Non-linear re-calibration of force platforms. Gait &
Posture
33, pp: 724–726.
Cedraro, A., Cappello, A., Chiari, L., (2009). A portable
system for in-situ re-calibration of force platforms:
experimental validation.
Gait & Posture, 29, pp. 449–
453.
Chockalingama, N., Giakasb, and Iossifidoua, A., (2002).
Do strain gauge force platforms need in situ
correction?
Gait & posture, 16(3), pp: 233-237.
Collins, S. H., Adamczyk, P. G., Ferris, D. P., Kuo, A. D.,
(2009). A simple method for calibrating force plates
and force treadmills using an instrumented pole
. Gait
Posture
. 2009, 29(1): 59–64.
Díaz-Rodríguez, M., Mata, V., Valera, V., Page, A.
(2010). A methodology for dynamic parameters
identification of 3-DOF parallel robots in terms of
relevant parameters. Mechanisms and Machine
Theory
, 45(9), pp 1337–1356.
Fairburn, P. S., Palmer, R., Whybrow, J., Fielden, S.,
Jones, S., (2000). A prototype system for testing force
platform dynamic performance.
Gait and Posture, pp:
25–33.
Farhat, N., Mata, V., Rosa, D., Fayos, J, (2010). A
procedure for estimating the relevant forces in the
human knee using a four-bar mechanism. Computer
Methods in Biomechanics and Biomedical
Engineering
, 13(5), pp 577-587.
Hall, M. G., Fleming, H. E., Dolan, M. J., Millbank, S. F.
D., Paul, J. P., (1996). Static in Situ Calibration of
Force Plates.
J. Biomechanics, 29(5), pp. 659-665,
1996.
Hatze, H., (2002). The fundamental problem of
myoskeletal inverse dynamics and its implications.
Journal of Biomechanics
, 35(1), pp 109–115.
Hsieh, H.-J., Lu, T.-W. Chen, S.-H., Chang,C.-M., Hung,
C.(2011). A new device for in situ static and dynamic
calibration of force platforms.
Gait & Posture 33, pp:
701–705.
Page, A., de Rosario, H., Mata, V., Atienza, C., (2009).
Experimental analysis of rigid body motion. A vector
method to determine finite and infinitesimal
displacements from point coordinates.
Journal of
Mechanical Design
131, 031005 (8 pp.).
Rabuffetti, M. Ferrarin, M., Mazzoleni, P., Benvenuti, F.,
Pedotti, A. (2003). Optimised procedure for the
calibration of the force platform location.
Gait and
Posture
17, pp: 75-80.
Schmiedmayer, H. B., Kastner, J., (1999). Parameters
influencing the accuracy of the point of force
application determined with piezoelectric force plates.
J. Biomech., 32, pp. 1237–1242.
Vallés, M., Díaz-Rodríguez, M., Valera, A., Mata, V.,
Page, A., (2011) Mechatronic developmentand
dynamic control of a 3 dof parallel manipulator.
MUSME 2011, the Int. Symposium on Multibody
Systems and Mechatronics
, Valencia, Spain, 25-28
October 2011.
BIODEVICES2013-InternationalConferenceonBiomedicalElectronicsandDevices
136