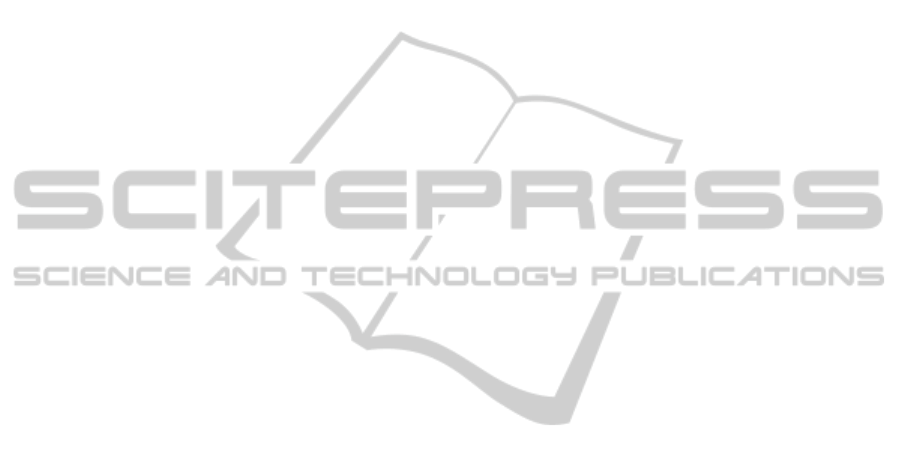
4 CONCLUSIONS
In this paper, we presented the first machine vision
based board tracing system to be used in a sawmill
to track when a particular board has completed the
manufacturing process. This is one important part of
the chain from raw material to final products. The
proposed system was evaluated using real life images
and was it able to find a correct match for over 96% of
the tested 495 images from a test set of 1003 images.
We proposed a projection signal based alignment
method, which increased the robustness of the system
considerably. Instead of using column sums, standard
deviation of the column was used to create the 1-D
signal. If the alignment accuracy is improved while
keeping the computational complexity low, smaller
subarea widths can be used, thus lowering the total
number of operations required.
The use of gradient images increased the accu-
racy and confidence of the CS-LBP based method.
One possible explanation for this is the material itself.
Grain patterns are unique to different boards, similar
to fingerprints. When the feature vector length was
increased the benefit from gradient images started to
decline, and with 256 long vectors, the matching ac-
curacy was the same. Both of the descriptors are com-
putationally inexpensive and they are well suited for
an application where real-time performance is a criti-
cal parameter.
For future work, implementation using parallel
computing needs to be considered. Accelerated meth-
ods for database queries and comparisons, as well
as strategies for limiting the number of feature ma-
trix comparisons, can offer a significant increase in
the total system performance. Initial pruning of pos-
sible candidates for matching can be started in the
alignment state. Also, a new ORB descriptor (Rublee
et al., 2011), which is claimed by original authors to
be tens of times faster than the SURF method, should
be tested in this application. Fingerprint matching
techniques could also be well suited for this kind of
task.
The described system was targeted here to be used
inside sawmills although it is not in any way limited
to that application area.
REFERENCES
Agarwal, R. and Cooley, J. (1977). New algorithms for dig-
ital convolution. Acoustics, Speech and Signal Pro-
cessing, IEEE Transactions on, 25(5):392 – 410.
Alliney, S. and Morandi, C. (1986). Digital image registra-
tion using projections. IEEE Transactions on pattern
analysis and machine intelligence, PAMI-8(2):222–
233.
Bay, H., Ess, A., Tuytelaars, T., and Gool, L. V. (2008).
Speeded-up robust features (SURF). Computer Vision
and Image Understanding, 110(3):346–359.
Fuentealba, C., Simon, C., Choffel, D., Charpentier, P.,
and Masson, D. (2004). Wood products identifica-
tion by internal characteristics readings. In IEEE In-
ternational Conference on Industrial Technology, vol-
ume 2, pages 763–768.
Gu, I. Y.-H., Andersson, H., and Vicen, R. (2010). Wood
defect classification based on image analysis and sup-
port vector machines. Wood Science and Technology,
44(4):693–704.
Heikkil¨a, M., Pietik¨ainen, M., and Schmid, C. (2009). De-
scription of interest regions with local binary patterns.
Pattern Recognition, 42(3):425–436.
Loan, C. V. (1992). Computational Frameworks for the fast
Fourier transform. SIAM Publications.
Ojala, T., Pietik¨ainen, M., and M¨aenp¨a¨a, T. (2002). Mul-
tiresolution gray-scale and rotation invariant texture
classification with local binary patterns. IEEE Trans-
actions on Pattern Analysis and Machine Intelligence,
24(7):971–987.
Rublee, E., Rabaud, V., Konolige, K., and Bradski, G.
(2011). Orb: an efficient alternative to sift or
surf. International Conference on Computer Vision,
Barcelona.
Sirkka, A. (2008). Modelling traceability in the forestry
wood supply chain. In IEEE International Conference
on Data Engineering Workshop, pages 104–105.
Stone, H. S. (2011). Image Registration for Remote Sens-
ing: Chapter 4 - Fast correlation and phase correla-
tion. Cambridge University Press.
AMachineVisionbasedLumberTracingSystem
103