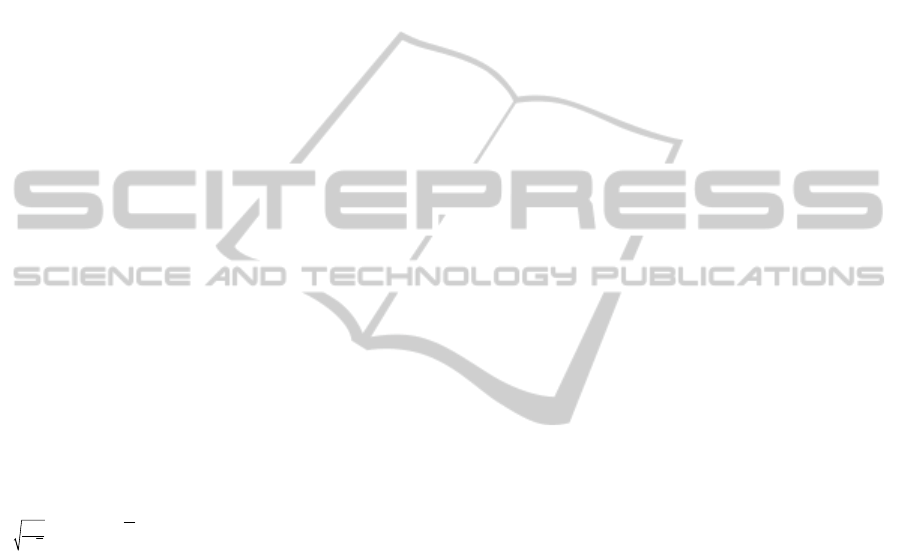
machine j,
j
p
is the total processing times of
jobs on machine j included in group g,
j
a
is the
number of tools needed additionally to assign
group g to machine j that we have available copy
and
j
b
is the number of tools needed
additionally to assign group g to machine j that
we do not have available copy.
Select the job with minimum priority value. Let
the group be g
.
2. Remove the tools from machine j that are not
elements of w
g
.
3. Load the tools that are elements of w
g
to
machine j and that are not already loaded on
machine j.
If a required tool is not free, then delay the
starting time of group g
on machine j until the
tool is free.
Go to Step 1.
There are two neighbourhood structures that
generate a solution. The first neighbourhood
structure is to swap two groups without considering
whether they are assigned to different machines or
not. The second structure is to remove a group from
its position and insert to another place on the same
or different machine. Infeasible solutions are not
considered due to complex structure of tooling.
Tabu attributes for this problem is the following;
when a group is assigned to a position on a machine,
removing that group from its place is called tabu for
a specified number of iterations. Tabu tenure is set
to
/
n
cl
, where l is the average number of tools
required by jobs.
5 CONCLUSIONS
In this study, we consider the scheduling of jobs on a
group of parallel CNC machines together with their
required tools in a flexible manufacturing system.
We also consider the tool switches between the jobs.
Our objective is to minimize the makespan. We
provide the mathematical model of the problem and
propose a heuristic approach based on decomposing
the problem into two subproblems: forming the job
groups and scheduling the groups on the machines.
In the future, we are planning to design
computational experiments and evaluate the
performance of our heuristic approach. Next, we will
work on efficient exact solution approaches such as
constraint programming.
ACKNOWLEDGEMENTS
This work is supported by The Scientific and
Technological Research Council of Turkey
(TÜBİTAK) grant no: 110M492.
REFERENCES
Agnetis, A., Alfieri, A., Brandimarte, P., Prinsecchi, P.,
1997. Joint job/tool scheduling in a flexible
manufacturing cell with no on-board tool magazine.
Computer Integrated Manufacturing Systems, 10, 61-
68.
Avci, S., Akturk, M. S., 1996. Tool magazine arrangement
and operations sequencing on CNC machines.
Computers and Operations Research, 23, 1069-1081.
Blazewicz, J., Finke, G., 1994. Scheduling with resource
management in manufacturing systems. European
Journal of Operational Research, 76, 1-14.
Crama, Y., Kolen, A. W. J., Oerlemans, A. G., Spieksma,
F.R.C., 1994. Minimizing the number of tool switches
on a flexible machine. International Journal of
Flexible Manufacturing Systems, 6, 33-54.
Crama, Y., 1997. Combinatorial optimization models for
production scheduling in automated manufacturing
systems. European Journal of Operational Research,
99, 136-153.
Ecker, K. H., Gupta, J. N. D., 2005. Scheduling tasks on a
flexible manufacturing machine to minimize tool
changing delays. European Journal of Operational
Research, 164, 627-638.
Gökgür, B., Hnich, B., Özpeynirci, S., 2012. Mathematical
modeling and constraint programming approaches for
operation assignment and tool loading problems in
flexible manufacturing systems. 21
st
International
Symposium on Mathematical Programming.
IBM ILOG OPL V6.3, 2009. Language User’s Manual.
Karakayalı, İ., Azizoğlu, M., 2006. Minimizing total flow
time on a single flexible machine. International
Journal of Flexible Manufacturing Systems, 18, 55-73.
Kellerer, H., Strusevich, V. A., 2004. Scheduling
problems for parallel dedicated machines under
multiple resource constraints. Discrete Applied
Mathematics, 133, 45-68.
Laporte, G., Salazar-Gonzalez, J. J., Semet, F., 2004.
Exact algorithms for the job sequencing and tool
switching algorithm. IIE Transactions, 36, 37-45.
Özpeynirci, S., Gökgür, B., 2011. A tabu search algorithm
for scheduling with tool assignment in flexible
manufacturing systems. 24
th
Conference of European
Chapter on Combinatorial Optimization.
SchedulingwithToolSwitchinginFlexibleManufacturingSystems
181