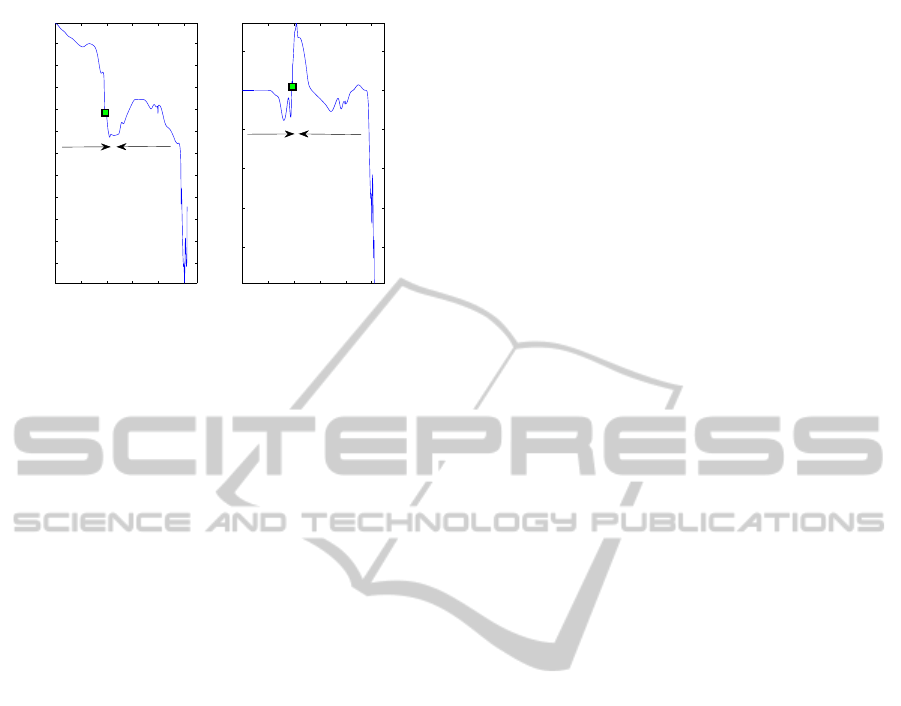
0 1000 2000 3000 4000 5000
−10
−8
−6
−4
−2
0
2
4
6
8
10
0 1000 2000 3000 4000 5000
−4
−3
−2
−1
0
1
TimestepTimestep
F
x
(N)
F
y
(N)
Open
Open
Close
Close
Figure 8: Door opening and closing where the door is ini-
tially open at 8 degrees. The time step is equal to 1ms.
door’s joint is characterized as revolute and estimate
the joint space constrains which is computed, see Fig.
6. This angle space constitutes the input state space in
terms of which the force trajectories are learned from
multiple demonstrations. Fig. 7 shows learning of the
2-dimensional force for a door opening-closing task
from 3 demonstrations by using the method described
in Section 2.3. The force is learned separately for the
two phases of the task. Following learning, we desire
to generalize the force generation policy to different
tasks with different current state. More specifically,
the case is considered where the car door is already
open at 8 degrees and the force profile is estimated
which needs to be exerted in order to open the door
completely and close it afterwards. Fig. 8 shows the
generalized force for this task where the two phases,
opening and closing.
4 CONCLUSIONS
In this paper, we propose a method for articulated ob-
ject modeling by combining visual and haptic data.
Visual processing contributes to recognizing the ob-
ject and identifying its structure and more specifi-
cally, its skeleton topology, the number and type of
joints as well as the current joint states. Haptic data
represented by force are learned from multiple task
demonstrations in order to be able to operate the ar-
ticulated mechanism. The forces are encoded with
respect to joint states so that the system can gener-
alize to new situations where the initial object con-
figuration, and thus, joint state differs. The proposed
method is demonstrated in manipulation of a single-
joint car door. Future work will focus on modeling
of a wide-variety of objects which also involve more
than one joint.
ACKNOWLEDGEMENTS
This work is supported in part by the DFG excel-
lence initiative research cluster ”Cognition for Tech-
nical Systems – CoTeSys,” see www.cotesys.org, the
FP7 EU-STREP ”Interactive Urban Robot (IURO)”,
see www.iuro-project.eu, the Institute for Advanced
Study (IAS), Munich, and the China Scholarship
Council (CSC), see http://en.csc.edu.cn.
REFERENCES
Calinon, S., Guenter, F., and Billard, A. (2007). On learn-
ing, representing, and generalizing a task in a hu-
manoid robot. Systems, Man, and Cybernetics, Part
B: Cybernetics, 37(2):286–298.
Huang, X., Walker, L., and Birchfield, S. (2012).
Occlusion-aware reconstruction and manipulation of
3d articulated objects. In In Proc. of the IEEE In-
ternational Conference on Robotics and Automation
(ICRA), pages 1365–1371, St. Paul, Minnesota.
Kalakrishnan, M., Righetti, L., Pastor, P., and Schaal, S.
(2011). Learning force control policies for compli-
ant manipulation. In Intelligent Robots and Systems
(IROS), pages 4639–4644.
Katz, D. and Brock, O. (2008). Manipulating articulated
objects with interactive perception. In In Proc. of the
IEEE International Conference on Robotics and Au-
tomation (ICRA), pages 272–277, Pasadena, CA.
Lee, D. and Ott, C. (2011). Incremental kinesthetic teaching
of motion primitives using the motion refinement tube.
Autonomous Robots, 31(2):115–131.
Lutscher, E., Lawitzky, M., Cheng, G., and Hirche, S.
(2010). A control strategy for operating unknown
constrained mechanisms. In In Proc. of the IEEE In-
ternational Conference on Robotics and Automation
(ICRA), pages 819–824, Anchorage, Alaska, USA.
Rusu, R. B., Bradski, G., Thibaux, R., and Hsu, J. (2010).
Fast 3d recognition and pose using the viewpoint fea-
ture histogram. In In Proc. of the International Con-
ference on Intelligent Robot Systems (IROS), pages
2155–2162, Taipei, Taiwan.
Sturm, J., Stachniss, C., and Burgard, W. (2011). A prob-
abilistic framework for learning kinematic models of
articulated objects. Journal of Artificial Intelligence
Research, 41(2):477–526.
Tagliasacchi, A., Zhang, H., and Cohen-Or., D. (2009).
Curve skeleton extraction from incomplete point
cloud. In ACM Trans. on Graph, 28(3):71.
Wang, W., Brˇsˇci´c, D., He, Z., Hirche, S., and K¨uhnlenz,
K. (2011). Real-time human body motion estimation
based on multi-layer laser scans. In In Proc. of the
International Conference on Ubiquitous Robots and
Ambient Intelligence, pages 297–302, Incheon, Korea.
ArticulatedObjectModelingbasedonVisualandHapticObservations
259