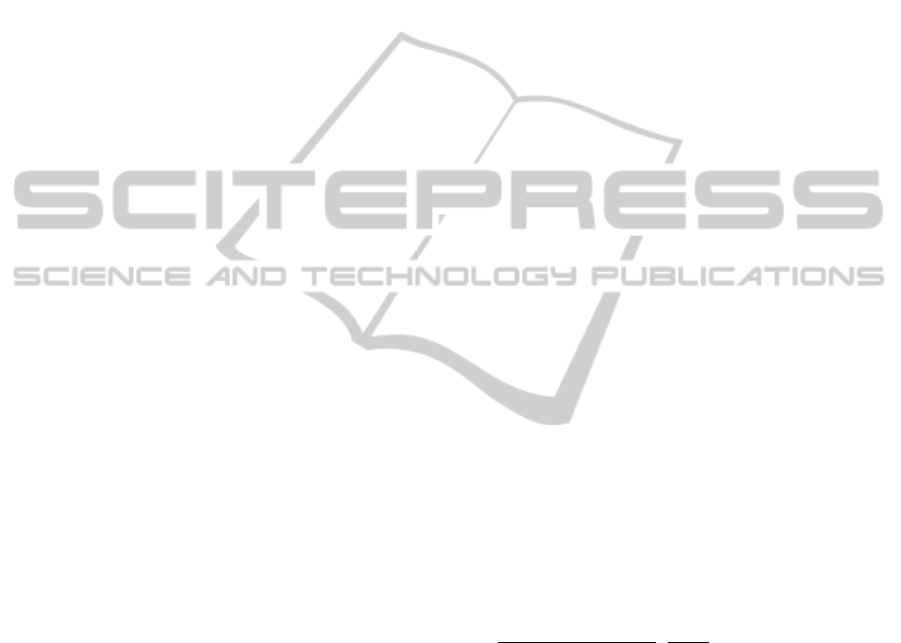
= Set of job site locations
, = Indices used for locations ,∈
= Set of works being done in site ∈
= Index used for works
= Index used for time (day)
= Beginning time of scheduling
1
= Latest time possible for starting work
= Earliest time possible for starting work
= Duration of work (in units of time)
= Travel time from location to location
= Transportation cost from location to
= Rental price from location for use in location
at time ($/day)
= Usage cost (depreciation cost) for an owned
equipment in location at time ($/day)
= Available owned equipment in at time
= Utility value of doing work at time ($)
Variables used in the model are as following.
1amachinefromlocationiassignedto
worknattimetinlocationj
0otherwise
1arentalmachinefromlocationi
assignedtoworknattimetinlocationj
0otherwise
Numberofavailablemachineswithnowork
assignedtoinlocationiattimet
The problem is modelled as a multi-objective model
incorporating several objectives as following.
i. Maximizing utility:
.
∈
∈
∈
(1)
ii. Minimizing transportation cost:
.
∈
∈∈
(2)
iii. Minimizing rental cost:
.
∈
∈∈
(3)
iv. Minimizing usage cost:
.
∈
∈∈
(4)
To combine all objectives, without loss of generality
it is assumed that they all have same weight and
importance for the company; however, knowing the
trade-offs between different objectives, the decision
maker can decide on the weight vector based on his
utility function by studying the Pareto set of
attributes (Bui and Alam, 2008). Following are the
constraints in the model.
∈
1;∀∈,∀∈
(5)
∈
∈
;∀∈,∀
(6)
∈
∈
∈
∈
;∀
∈,∀
(7)
0 ;∀∈,∀
(8)
,
;∀∈,∀∈,∀,∀∈
(9)
Constraints (5) enforce exactly one piece of
equipment being assigned to each job in the
acceptable time period. Constraints (6) assure not
sending more than available idle equipment from
each location to other locations. Constraints (7)
define the number of available idle equipment in
each location at each time period.
To define
, value of doing a job at time t, as
in (10), three factors are employed. First is cost and
penalty of conducting the work at any time other
than the planned schedule. This signifies the
difference between critical and non-critical jobs.
Second is the importance and priority of conducting
a job from the perspective of managers which can be
calculated using Analytic Hierarchy Process method
(Saaty, 1990). Third is the linkage between different
jobs due to the technical issues in a project.
0;
∑
∈
1
∗
∗
∑
∈
∗;
(10)
is set of all projects which project is one of
their predecessors.
is set of all projects which are
in need of the equipment at time t. 01 is the
project
’s importance index for the managers, and
is the budget assigned to project .
The predictive-reactive scheduling has two steps.
The model presented above generates a predictive
schedule employing available data in the first stage.
In the second stage, which can be repeated several
times, the original model is adjusted in order to
revise the schedule in response to real time events
and changes. In this stage notations are borrowed
from the first stage; however, the additional letter
“P” identifies updated information and the new set
of variables after rescheduling time (tp
0
in stage
APredictive-ReactiveDynamicSchedulingunderProjects'ResourceConstraintsforConstructionEquipment
187