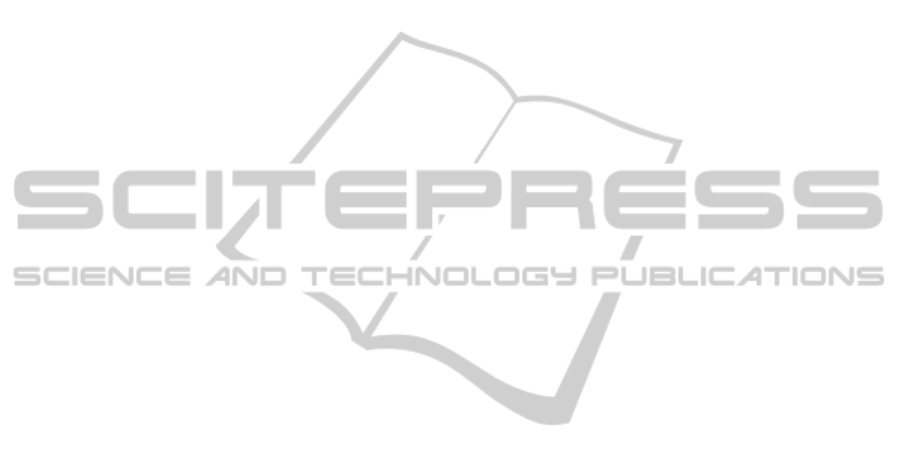
ACKNOWLEDGEMENTS
The present paper was developed with the economic
support of MIUR (Italian Ministry of University and
Research) performing the activities of the project
PON01_01268 “Digital pattern product
development: a pattern driven approach for
industrial product design”.
REFERENCES
Bondy, J. A., Murty U. S. R., 2008. Graph theory,
Springer. New Delphi.
Charchut, W., Thomas, A. K., 1972. Ingranaggi, Tecniche
Nuove. Milano.
Chen, X., Gao, S., Yang, Y., Zhang, S., 2012. Multi-level
assembly model for top-down design of mechanical
products. Computer Added Design, vol. 44, pp. 1033-
1048.
Deo, N., 2004. Graph theory with applications to
engineering and computer science, PHI Learning.
New Delphi.
Franciosa, P., 2009. Modeling and simulation of
variational rigid and compliant assembly for tolerance
analysis, PhD Thesis. Naples.
Franciosa, P., Patalano, S., Riviere, A., 2010. 3D tolerance
specification: an approach for the analysis of the
global consistency based on graphs. International
Journal of Interactive Design and Manufacturing, vol.
4 (1), pp. 1-10.
Franciosa P., Gerbino S., Patalano, S., 2011. Simulation of
Variational Compliant Assemblies with Shape Errors
Based on Morphing Mesh Approach, Int. Journal of
Advanced Manufacturing Technology, vol. 53,
Numbers 1-4, pp.47-61, ISSN 0268-3768.
Franciosa P., Gerbino S., Lanzotti A, Patalano S., 2012.
Automatic evaluation of variational parameters for
tolerance analysis of rigid parts based on graphs,
International Journal of Interactive Design and
Manufacturing, ISSN 1955-2513, Springer Paris, DOI
10.1007/s12008-012-0178-4.
Juvinall, R. C., Marshek, K. M., 1994. Fondamenti della
progettazione dei componenti delle macchine, ETS.
Lockett, H. L., Guenov, M. D., 2005. Graph-based feature
recognition for injection moulding based on a mid-
surface approach. Computer-Aided Design, vol. 37,
pp. 251-262.
Marler, R. T., Arora, J. S., 2004. Survey of multi-objective
optimization methods for engineering. Structural and
multidisciplinary optimization vol. 26 (6), pp. 369-
395.
Sandeberg, M, 2003. Knowledge based engineering – in
product development. ISSN: 1402-1536.
Shai, O., 2003. Transforming engineering problems
through graph representations. Advanced Engineering
Informatics, vol. 17, pp. 73-93.
Shai, O., Preiss, K., 1999. Graph theory representations of
engineering systems and their embedded knowledge.
Artificial Intelligence in Engineering, vol. 13, pp.
273–285.
Sham Tickoo, 2010. CATIA V5R19 for engineers and
designers, Dreamtech Press.
Sham Tickoo, 2012. NX8 for designers, CADCIM
Technologies.
Sharmin, M., Bailey, B. P., Coats, C., Hamilton, K., 2009.
Understanding knowledge management practices for
early design activity and its implications for reuse.
CHI 2009 Proceedings of the 27
th
international
conference on human factors in computing systems,
pp.2367-2376.
Suh, N. P., 1990. The principles of design. Oxford
University Press. New York.
Suh, N. P., 1997. Design of Systems. Annals of the CIRP,
vol. 46 (1), pp. 75-80.
Tang, D., Zhang, G., Dai, S., 2009. Design as integration
of axiomatic design and design structure matrix.
Robotics and Computer-Integrated Manufacturing,
vol. 25, pp. 610-619.
Tang, D., Zhu, R., Tang, J., Xu, R., He, R., 2010. Product
design knowledge management based on design
structure matrix. Advanced Engineering Informatics,
vol. 24, pp. 159-166.
VV.AA., 2008. CATIA - Product Knowledge Template
Definition 2, Dassault Systemes. www.3ds.com/
product/catia.
VV.AA., 2012. Data sheet CREO Advanced Assembly
Extension, PTC Inc.
Wilson, R. J., 1978. Introduzione alla teoria dei grafi,
Cremonese Editore.
APPENDIX A - NOTATION
Below are listed the parameters shown in Table 2,
Table 3 and Table 4:
= transverse pressure angle;
= number of teeth on driven gear;
= number of teeth on drive gear;
= helix angle;
= module;
= face factor;
= Lewis’s geometric factor;
= 0.830.88∗ for 15°30°;
= torque;
= allowable stress;
= allowable pressure;
= dynamic factor;
= helix angle factor.
AGraph-basedSoftwareToolfortheCADModelingofMechanicalAssemblies
69