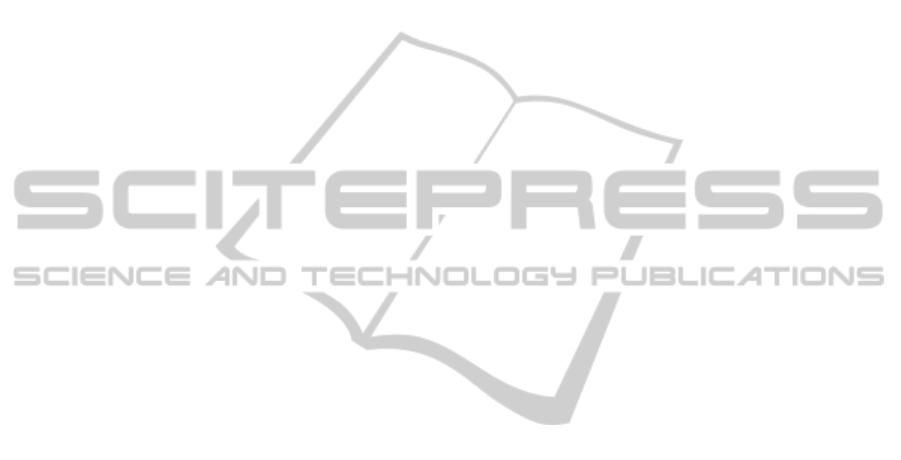
to detect the target tracking region. We present a
method that can find correct corresponding points
even if the target texture is not on planar surface. By
using this method, we can remove color makers from
the T-shirt. Furthermore, we improvedpoint sampling
method, which allowed us to obtain more accurate
point cloud from captured 3D data.
One important characteristic of our method is that
we achieve accurate non-rigid surface deformation in
real-time with simple hardware and equipment. This
was achieved by only using inexpensive devices: reg-
ular PC, commodity RGB-D camera, and a display. In
addition, the users are not required to wear specially
prepared T-shirt, such as the ones that are specially
colored or have markers attached.
Generally, depth components captured by com-
modity RGB-D camera contain noises. Therefore,
we couldn’t get accurate deformed mesh by using 3D
reconstruction from these noisy data. Our method
is based on learning representative deformation of
meshes, deformed mesh is registered to the target sur-
face. The shape of registered mesh is accurate and
noise-free.
The rest of this paper is structured as follows. Sec-
tion 2 briefly describes the related works in non-rigid
surface tracking, and states the contribution of this
paper. Section 3 describes our system. Section 4
explains the detection of the region on non-rigid ob-
ject. Section 5 describes the tracking and overlaying
texture approach for non-rigid surface in RGB-D se-
quence. Finally, Section 6 presents experimental re-
sults.
2 RELATED WORKS AND
CONTRIBUTION
Non-rigid surface tracking and texturing have re-
cently been addressed by a number of researchers.
Most of them are applying a two or three dimensional
deformable model reconstructed from RGB camera.
There are some researches approaching practical
virtual fitting system. For example, Hilsmann and
Eisert proposed a real-time system that tracks clothes
and overlays a texture on them by estimating the elas-
tic deformations of the clothes from a single camera
in the 2D image plane (Hilsmann and Eisert, 2009).
The problem of self-occlusion is addressed by using a
2D motion model regularizing an optical flow field. It
works correctly in real-time, but under an assumption
that the motion is small enough, and that the T-shirt is
specially colored and textured.
In order to handle larger and sharp deformation,
many researches about 3D deformable model recon-
struction have been done. Pilet et al. have pre-
sented a feature-based fast method which detects and
tracks deformable objects in monocular image se-
quences (Pilet et al., 2007). They applied a wide base-
line matching algorithm for finding correspondences.
Shen et al. recovered the 3D shape of an inextensi-
ble deformable surface from a monocular image se-
quence (Shen et al., 2010). Their iterative L
2
-norm
approximation process computes the non-convex ob-
jective function in the optimization. The noise is re-
duced by applying a L
2
-norm on re-projection errors.
All these 3D reconstruction methods yield impres-
sive results. However, they need sophisticated acqui-
sitions setups or have a high computational cost. We
strive for a different goal, i.e. to estimate non-rigid
surface of common T-shirt in real-time with normal
hardware. For that purpose we are interested in gen-
eration of a deformation mode space from the PCA
(Principal Component Analysis) of sample triangular
meshes (Salzmann et al., 2007). Reducing DOF (De-
gree of Freedom) by PCA achieved real-time 3D de-
formable model reconstruction. The non-rigid shape
is then expressed by the combination of each defor-
mation mode. This step does not need an estimation
of an initial shape or a tracking. Later, they proposed
a linear local model for a monocular reconstruction
of a deformable surface (Salzmann and Fua, 2011).
This method reconstructs an arbitrary deformed shape
as long as the homogeneous surface has been learned
previously. However, these approaches require a lot
of corresponding points between a template image
and an input image. Therefore, users have to wear
texture-rich T-shirt.
Hayashi et al. improved the method proposed
by Salzmann (Hayashi et al., 2012). By using 3D
data captured by a RGB-D camera, even though input
depth data is noisy, this learning-based method can
generate a natural and smooth mesh. And, because
the 3D data is directly captured, texture-rich surface
is not required. Furthermore, this method achieves a
real-time process by taking the advantage of PCA, a
simple method of reducing the dimensionality of the
data, which in this case is the meshes. Unfortunately,
in this method, users are required to set color markers
on their T-shirt for detecting target region.
In our research, we improved non-rigid surface
tracking method based on Hayashi’s method. The
main contribution of this paper lies in a real-time
tracking and texture overlaying method for non-rigid
surfaces on common T-shirt. Common T-shirt means
a T-shirt without rich texture or markers. The dif-
ficulty is to detect sufficiently accurate correspond-
ing points from texture on the shirt. We present
a method which can detect accurate corresponding
Non-rigidSurfaceTrackingforVirtualFittingSystem
13