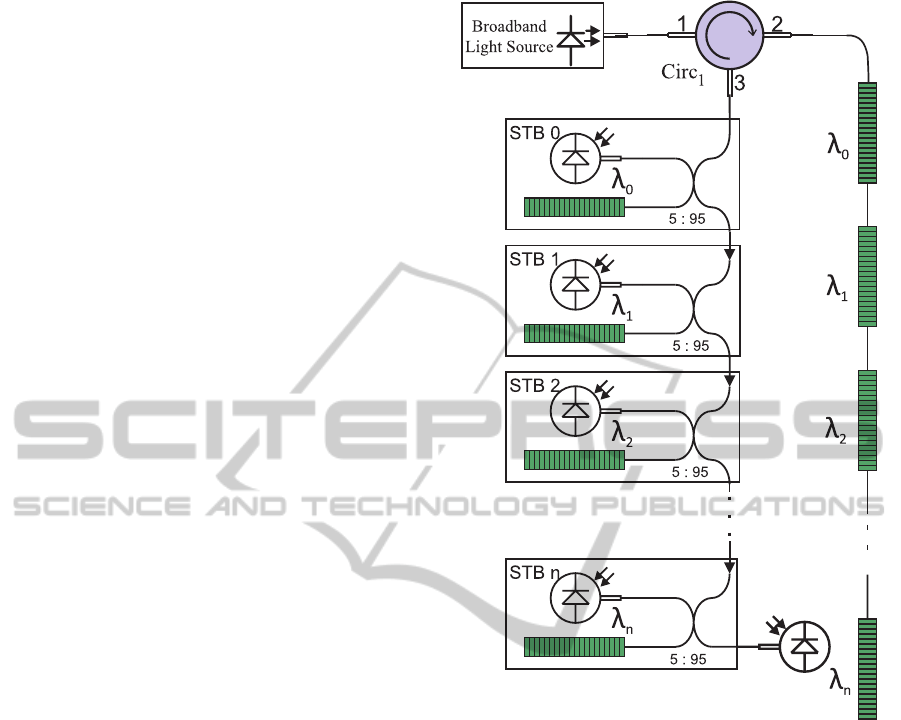
After the temperature of the first FBG is read, the
PID controller is disconnected from the TEC power
driver and the microcontroller DAC starts to heat the
TEC, in order to the laser reach the next FBG. Again,
when the output of the transimpedance amplifier indi-
cates that the laser wavelength is at the beginning of
the spectrum of next FBG, the same procedure done
with the first FBG is repeated (the DAC is discon-
nected, the PID takes control of the system, etc.). This
is repeated until the last FBG in the chain is measured,
when the system begins to travel backwards (by cool-
ing the laser), in the direction of the first FBG.
The only difference when measuring the FBGs
during the returning path (cooling the laser) is that
now it is necessary to drive the TEC until the laser
crosses the whole FBG spectrum and the condition
V
out
= 0.9V
0
is reached, that is, the laser wavelength
is at the left side of the FBG so that the PID takes
control of the system always at the same point. It is
important to notice that this system is relatively slow,
since the measurements cannot be performed simul-
taneously and the time required to scan four FBGS
(heating/cooling time, PID time necessary to stabilize
the system) can take up to 2 minutes.
2.3 Multi-Point FBG Sensing with
Broad Band Lasers
Implementing a closed-loop interrogator using a
broad band laser leads to a system which can accept a
large number of sensing FBGs and a extremely very
fast measurement time, typically in the order of a few
microseconds for each FBG. A block diagram of the
interrogation system using a broad band laser is pre-
sented in Figure 3. In this scheme, the number of
optical components is proportional to the number of
FBGs sensing elements, and the final cost of an inter-
rogation system with input for more than 3 FBG tem-
perature sensors is dominated by the cost of the opti-
cal components (tracking FBGs, couplers and photo-
diodes).
The broad band laser illuminates the chain with
n FBGs sensing elements through a optical circula-
tor Circ
1
. The reflected light from the chain of FBG
sensing elements is fed into a series of optical cou-
plers. Each optical coupler let 95% of the incoming
light goes to the next coupler, and 5% of the light
is directed into a small circuit called Signal Tracking
Block (STB
i
. In each STB there is one FBG (called
tracking FBG, which is glued to a Zn substrate), one
photodiode, one thermoelectric cooler, one semicon-
ductor temperature sensor and one microcontroller
with its the electronic circuitry. Although it is not nec-
essary that the tracking FBGs be matched to the sens-
Figure 3: Block diagram of the broad band laser multi-point
closed-loop interrogator.
ing FBGs, it is easier to design the system if the FBGs
in each pair of tracking/sensing FBGS have their cen-
tre λ close. The basic schematic of each STB block is
presented in Figure 4,
The STB electronics circuits drive the TEC while
the microcontroller acquires the output of the tran-
simpedance amplifier, which value is equal to the con-
volution between the sensing and the tracking FBGs.
A PID algorithm executed in the microcontroller con-
trols a DAC and a TEC driver circuit, forcing the
value of this convolution (output voltage of the tran-
simpedance amplifier V
out
) to be equal to a reference
value V
ref
. If the temperature behaviour of the track-
ing FBG was previously characterized, measuring its
temperature it is possible to determine the centre λ of
the tracking FBG. Knowing the centre λ of the track-
ing FBG and remembering that, in the same FBG pro-
file (one has to choose to operate on the left or on the
right side of the FBG profile) the convolution value
is uniquely related to the centre wavelength of sens-
Closed-loopInterrogationTechniquesforTemperatureMeasurementusingFibreBraggGratings
37