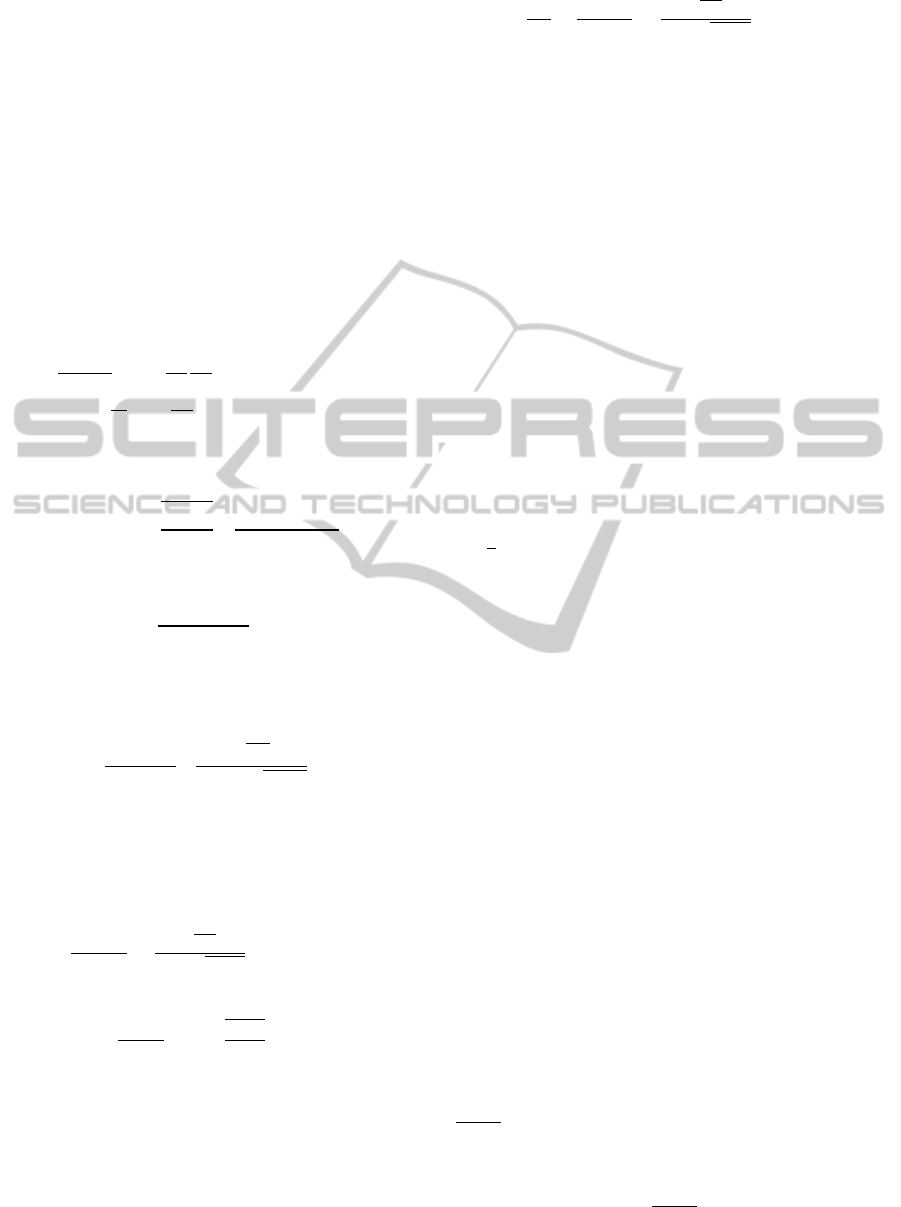
short period of time, the retailer only makes a one-
time purchase during the promotion period to take
advantage of the discount. After the short promotion
time, the retailer resumes its economic order
quantity
∗
for the rest of this period until the next
discount occurs at the beginning of the next period.
In particular, let
be this one time order quantity.
Since we assume that the discounts are offered by
the manufacturer regularly, the retailer has no reason
to order more than units when the deal is on. Thus,
we can restrict
without loss of generality. It
follows that the retailer’s total cost in one period is
given by
=
1
1
∗
1
∗
1
.
(2)
Differentiating
with respect to
, we
obtain
2
1
(3)
and
1
0.
(4)
Hence,
is convex in
and the optimal
order quantity, denoted by
∗
,is uniquely solved by
equation
0. It directly follows that
∗
1
2
1
.
(5)
Clearly that
∗
is strictly increasing in the discount
level d. Furthermore, notice that
∗
∗
when
0. Thus,
∗
∗
. Since the retailer would
never order more than units when the deal is on,
the maximum level of discount
̅
is given by
= 1,
(6)
or equivalently
1
.
(7)
Clearly, for any
̅
, the retailer would order
units at the discount price. Therefore, we shall
assume that
̅
in the following analysis, and
so
∗
.
Let α denote the proportion of the one-time
purchase out of its total demand when the price
discount is offered, i.e.,
α =
∗
1.
(8)
2.1 The Manufacturer Model
The manufacturer model studies the optimal
production schedule that minimizes the
manufacturer’s production and inventory holding
costs given the retailers’ purchasing pattern and the
capacity of the manufacturer’s facility. In this model,
we assume that there are many identical individual
retailers who independently make purchasing
decisions from this manufacturer. Here are the
notations we will use throughout the paper for the
manufacturer.
= the manufacturer’s setup cost per order;
= the manufacturer’s unit production cost;
= the manufacturer’s unit holding cost per period,
expressed as a percentage of the value of the item;
μ = the manufacturer’s production rate per period;
λ = the manufacturer’s aggregate demand rate per
period.
ρ =
, utilization of the manufacturer’s facility.
The retailer model discussed in Section 2.1 suggests
that individual retailer purchases a certain portion
(α) of its total one-period demand when the discount
is offered at the beginning of each period. Since we
assume identical retailers, it is clear that α portion of
the aggregate demand λ occurs when the discount is
offered at the beginning of the period, with no
demand for the following α period of time, and the
remaining demand (λ - αλ) occurs for the next
(1 – α) period of time. We assume that demand (λ -
αλ) occurs uniformly between time (1 – α) and time
1.
We now study the manufacturer’s optimal
production schedule that minimizes the total cost.
There exist four cases depending on the value of α
and the utilization of the facility ρ.
Case (i) 01 and 1
Case (i) represents the situation where some discount
is offered at the beginning of each period and the
utilization of the facility is lower than a
threshold1. In this case, the manufacturer
would start to build up the inventory at time [1-
–
so that he can get ready for the price
promotion that occurs at the beginning of the next
time period. Therefore, the last production run in this
period begins at time [1-
–
.
We next adopt the idea of the Economic
ICORES2013-InternationalConferenceonOperationsResearchandEnterpriseSystems
196