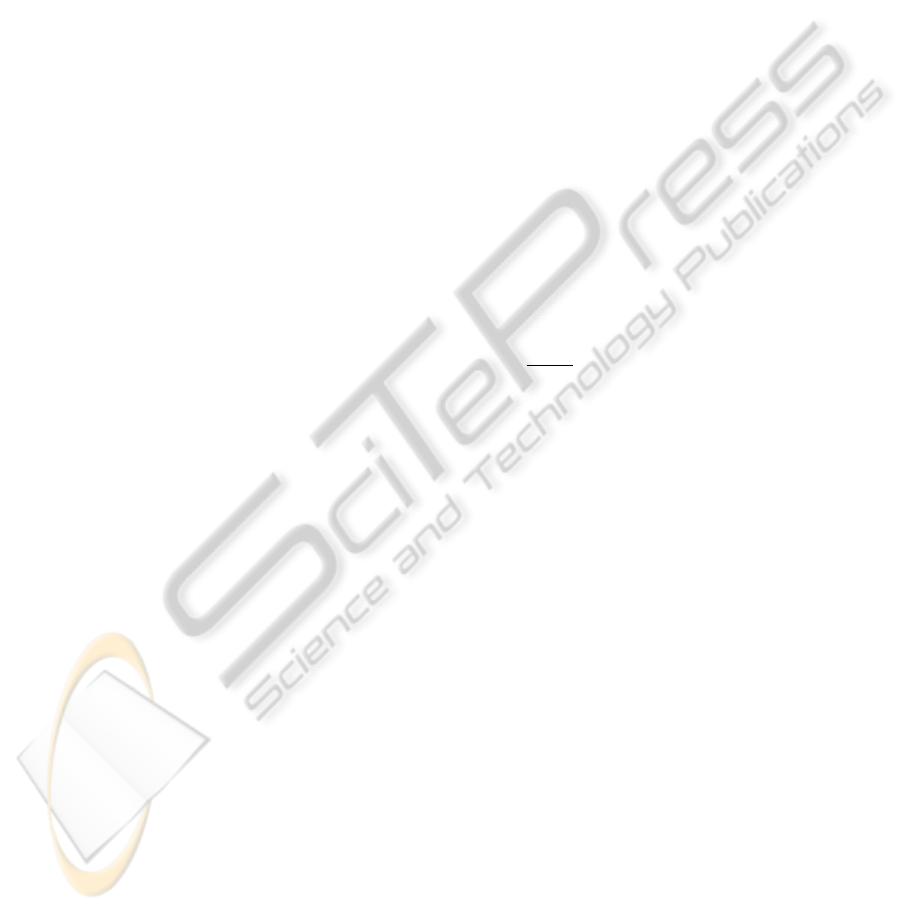
have only small daily costs and are located around.
Resolving the jobs with small daily costs first leads
to long detours, which could be compensated by the
savings in daily costs only in benchmark VI. In bench-
mark IV the small daily costs are low enough, so that
long detours to resolve them are not necessary. There-
with CB obtains the best result.
The heuristics have also been tested in further
benchmarks, with different jobs on the network and
different assignments of daily costs to jobs. We no-
ticed that it is hard to predict which heuristic obtains
the best result. But some statements are possible:
• If the daily costs have a small share in the mainte-
nance costs, then NJ and CB obtains good results,
because they minimise the travel costs.
• If the daily costs are high and scattered over the
track network, then CB obtains the best results.
MEJ resolves the expensive jobs more ordered by
daily costs and thus travels crisscross through the
network, where CB resolves the expensive jobs
first, too, but ordered by location. The resulting
savings in travel costs compensate the small in-
crement in daily costs.
• If the daily costs are medium or high and clus-
tered, then MEJ obtains good results, because of
the lower travel effort. Within CB the daily costs
often are underestimated in this type of bench-
marks, which leads to worse results.
4 ISSUES OF INTEREST FOR
FURTHER RESEARCH
The model presented in section 2 will be extended by
some additional points, see section 4.1.
In the further research solution approaches will
be developed that are suitable for arbitrary ratios be-
tween daily and travel costs, and that can handle the
additional restrictions from the model extension. The
metaheuristic Simulated Annealing (section 4.2) and
a multilevel solution approach (section 4.3) will be
implemented and compared in terms of solution qual-
ity and computation time in different benchmarks.
4.1 Model Extension
(1) K machines are available to resolve the jobs. So
K disjunctive job orders have to be defined and non-
simultaneous restrictions must be considered (e.g. a
minimal distance must be kept between two tamping
machines).
(2) Maintenance is not always possible. Due to night
trains, freight traffic, and other maintenance activities
the possible execution times of a certain job will be
restricted. In the model time windows will be defined
for each job when maintenance is possible. If the time
window ends before the maintenance works are fin-
ished, the crew must leave the track and wait for the
next time window.
(3) Consideration of depots. In some railway net-
works it is not possible or not common that the main-
tenance machine stays close to the track over the day.
There the machine stays in a depot. Then not only the
jobs are scheduled, but also the best depot to stay over
day must be determined and additional travel costs
must be considered.
4.2 Simulated Annealing
The basic idea of Simulated Annealing comes from
annealing processes in metallurgy. After heating the
metal the atoms are inordinated. Through the slow
cooling process they have enough time to order them-
self and to form crystals. This leads to a low-energy
state.
The algorithm starts in the “hot stage” with a
initial solution s and a high temperature T . Then
the solution ˜s is created by modifying s. Depen-
dent on the temperature T , the probability P(s, ˜s,T ) =
min{1, e
z(s)−z(˜s)
T
} to accept ˜s is calculated. If ˜s is ac-
cepted, then s := ˜s. After that the temperature is
cooled. This step – modify solution s, accept the mod-
ified ˜s with probability P(s, ˜s, T ), cool T – is repeated
until a given minimal temperature is reached. Then
the best solution is returned.
The challenge in the design of a proper Simulated
Annealing approach for an optimisation problem is
the definition of a modification heuristic to get the so-
lution ˜s and of a cooling schedule for T . For out tamp-
ing scheduling problem at first methods from solving
the TSP are implemented. The SA starts with a ran-
dom job order. The solution is modified by a 2-opt
method Meer (2007): Two indices 0 ≤ i < j ≤ n + 1
are chosen randomly and the suborder between i and
j is inverted. The temperature T is cooled exponen-
tially. This leads to a fast improvement of the solution
quality, but at the end the solution remains a bit frag-
mented. To smooth the solution a post-optimisation
method will be developed. With this, irregularities –
like jumping over a few jobs and resolve them later –
will be removed without losing the solution structure.
4.3 Multilevel Branch and Bound
Multilevel solution approaches are common methods
in graph partitioning Karypis and Kumar (1996) and
VLSI-design Cong et al. (2005). A multilevel solution
approach consist of three steps:
ICORES2013-InternationalConferenceonOperationsResearchandEnterpriseSystems
160