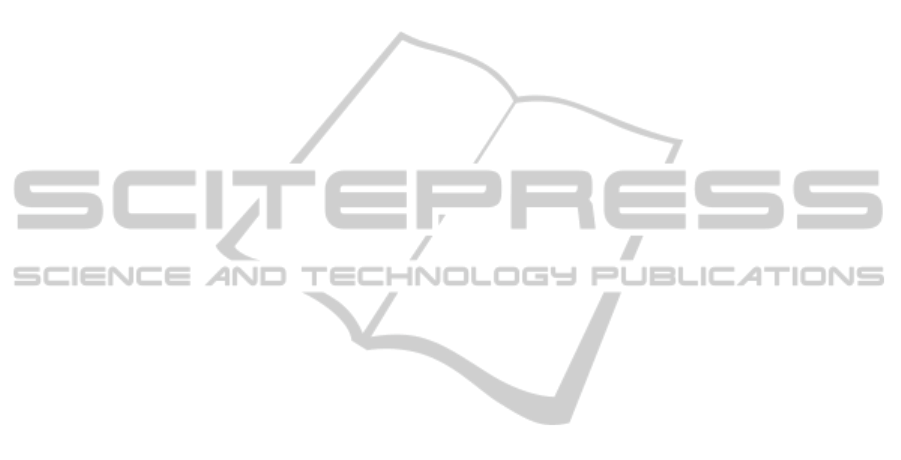
REFERENCES
Abdal, F., Abbas, R., and Abdulsada, M. A. (2010). Sim-
ulation of wind-turbine speed control by matlab. In-
ternational Journal of Computer and Electrical Engi-
neering, 2(5):912–915.
Abdin, E. and Xu, W. (2000). Control design and dynamic
performance analysis of a wind turbine-induction gen-
erator unit. IEEE Transactions on Energy Conversion,
15(1):91–96.
Astrom, K. and Wittenmark, B. (1995). Adaptive Control.
Addison-Wesley Publishing Company, 2nd edition.
Carter, R., Cruden, A., Hall, P., and Zaher, A. (2012).
An improved lead acid battery pack model for use in
power simulations of electric vehicles. IEEE Transac-
tions on Energy Conversion, 27(1):21–28.
Chiasson, J. and Vairamohan, B. (2005). Estimating the
state of charge of a battery. IEEE Transactions on
Control Systems Technology, 13(3):465–470.
Fuchs, E. F. and Masoum, M. A. (2011). Analyses and de-
signs related to renewable energy systems. In Power
Conversion of Renewable Energy Systems, pages 557–
687. Springer US.
Fusco, G. and Russo, M. (2008). Adaptive voltage regulator
design for synchronous generator. IEEE Transactions
on Energy Conversion, 23(3):946–956.
Fusco, G. and Russo, M. (2012). Nonlinear control design
for excitation controller and power system stabilizer.
Control Engineering Practice, 19(3):243–251.
Gentile, T. J. (2009). Smart grid a necessary component in
the remaking of america. IEEE-USA Annual Meeting.
Hiyama, T. (2011). Intelligent Automatic Generation Con-
trol. CRC-Press.
Jiang, Z., Li, F., Qiao, W., Sun, H., Wan, H., Wang, J., Xia,
Y., Xu, Z., and Zhang, P. (2009). A vision of smart
transmission grids. pages 1–10.
Jugo, J. (2002). Discretization of continuous time-delay
systems. In Proceedings of the 15th IFAC World
Congress, 2002, pages 117–122.
Kassem, A. M. (2012). Robust voltage control of a stand
alone wind energy conversion system based on func-
tional model predictive approach. International Jour-
nal of Electrical Power and Energy Systems, 41:124–
132.
Kassem, A. M. and Ali, M. Y. (2011). Robust control of an
isolated hybrid winddiesel power system using linear
quadratic gaussian approach. International Journal of
Electrical Power and Energy Systems, 33:1092–1100.
Kini, A. and Yaragatti, U. (2006). Modelling and simula-
tion of a wind/diesel hybrid power system. In Pro-
ceedings of the IEEE International Conference on In-
dustrial Technology, ICIT, pages 1670–1675.
Kuang, B., Wang, Y., and Tan, Y. L. (2000). An h
∞
con-
troller design for diesel engine systems. In Proceed-
ings of the International Conference on Power System
Technology, volume 1, pages 61–66.
Kumar, B., Mishra, S., Bhende, C., and Chauhan, M.
(2008). Pi controller based frequency regulator for
distributed generation. In Proceedings of the TEN-
CON - IEEE Region 10th Conference, pages 1 –6.
Lee, S.-H., Yim, J.-S., Lee, J.-H., and Sul, S.-K. (2008).
Design of speed control loop of a variable speed diesel
engine generator by electric governor. pages 1–5.
Minchala, L., Garza, L., and Calle, E. (2012). An intelli-
gent control approach for designing a low voltage dc
breaker. Number 4, pages 163–166.
Munoz-Aguilar, R., Doria-Cerezo, A., Fossas, E., and Car-
doner, R. (2011). Sliding mode control of a stand-
alone wound rotor synchronous generator. IEEE
Transactions on Industrial Electronics, 58(10):4888–
4897.
Nagrath, I. and Gopal, M. (2008). Control Systems En-
gineering. Anshan Ltd Press, United Kingdom., 5th
edition.
Schwaegerl, L., Tao, J.P.; Lopes, A., Madureira, P., Mancar-
ella, A., Anastasiadis, N., Hatziargyriou, and Krkol-
eva, A. (2009). Report on the technical, social, eco-
nomic, and environmental benefits provided by micro-
grids on power system operation.
Vandoorn, T., Meersman, B., Degroote, L., Renders, B., and
Vandevelde, L. (2011). A control strategy for islanded
microgrids with dc-link voltage control. IEEE Trans-
actions on Power Delivery, 26(2):703–713.
Vechiu, I., Camblong, H., Tapia, G. B., and Dakyo, C. N.
(2004). Dynamic simulation model of a hybrid power
system: Performance analysis. 2004 European Wind
Energy Conference.
Wang, L. (2009). Model Predictive Control System Design
and Implementation Using MATLAB. Springer Pub-
lishing Company, Incorporated, 1st edition.
Zeng, L. and Hu, G.-D. (2010). Discretization of
continuous-time systems with input delays. Acta Au-
tomatica Sinica, 36(10):1426–1431.
Model-basedControlApproachesforOptimalIntegrationofaHybridWind-dieselPowerSysteminaMicrogrid
21