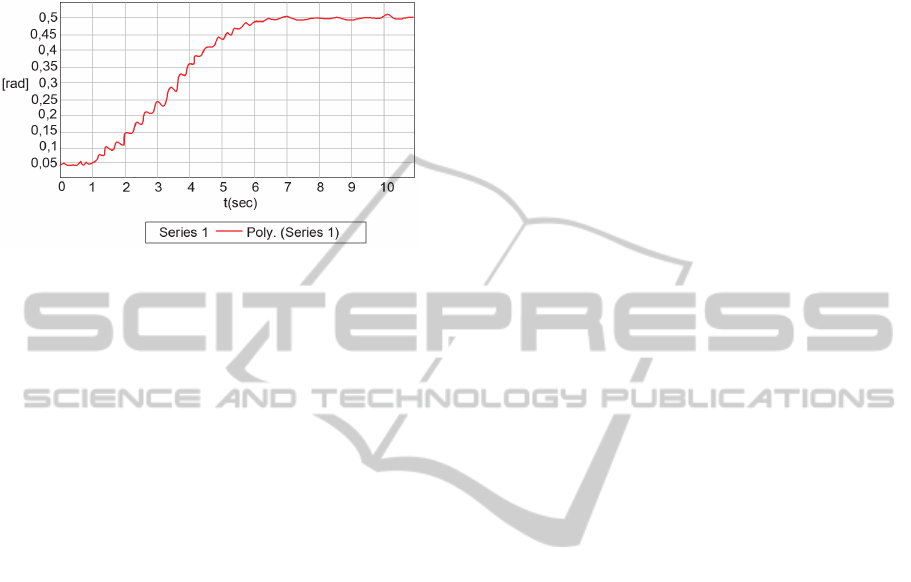
new desired position
2.7cos
1.5
. This
position is illustrated in Fig 8 and the sensor data are
presented in Fig 10. An analyse of this experimental
result confirms the algorithm performance.
Figure 10: Tracking position- Cluster Sensor2.
6 CONCLUSIONS
In this paper, the control problem that is related to a
class of tentacle arms has been discussed. The model
basis consists of a chain of vertebrae periodically
spaced, each element having a special joint that
ensures the rotation, elastic contact and a
controllable friction force with the following
element. All the joints are passive. We propose a
hybrid controller with two control components: a PD
boundary control and a pneumatic system that
controls the locking forces in the joints. For the
dynamic model described by a hyperbolic PDE with
uncertain components, a robust algorithm based a
spatial weighted error technique is discussed.
Liapunov methodes are used to prove the control
system stability. Numerical simulations and
experimental results verify the effectiveness of the
presented algorithms and techniques.
ACKNOWLEDGEMENTS
This work has been supported by PPCA 150/2012
Romania.
REFERENCES
Robinson ,G., Davies, G. B. C., 1999 “Continuum Robots
– A state of the art”, Proc. IEEE Int. Conf. on Robotics
and Automation, Detroit, May 1999, pp. 2849 – 2854.
Gravagne, Ian A., Walker, Ian D., 2000, On the kinematics
of remotely - actuated continuum robots, Proc. 2000
IEEE Int. Conf. on Robotics and Automation, San
Francisco, April 2000, pp. 2544-2550.
Gravagne, Ian A., Walker, 2000 Ian D., Kinematic
Transformations for Remotely-Actuated Planar
Continuum Robots, Proc. 2000 IEEE Int. Conf. on
Rob. and Aut., San Francisco, April 2000, pp. 19-26.
Chirikjian, G. S., Burdick, J. W., 1990, An obstacle
avoidance algorithm for hyper-redundant mani-
pulators, Proc. IEEE Int. Conf. on Robotics and
Automation, Cincinnati, Ohio, May 1990, pp. 625 – 631.
Mochiyama , H., Kobayashi, H., 1999, The shape Jacobian
of a manipulator with hyper degrees of freedom, Proc.
1999 IEEE Int. Conf. on Robotics and Automation,
Detroit, May 1999, pp. 2837- 2842.
Braganza, D., D. M. Dawson, Walker, N. Nath, N., 2007,
“A neural network controller for continuum robots”,
IEEE Transaction Robotics, vol. 23, issue 6, Dec.
2007, pp. 1270 – 1277.
Walker, I., M. Hannan, M., 1999, “A novel elephant’s
trunk robot”, AIM ’99, pp. 410 – 415.
Jones, B., I. D. Walker, 2006, “Practical kinematics for
real-time implementation of continuum robots”, IEEE
Trans. Robotics, vol. 22, no. 6, Dec. 2006, pp. 1087 –
1099.
Kapadia, I. Walker, D. Dawson, 2009 “A model – based
sliding mode Controller for Extensible Continuum
robots”, Recent Advances in Signal Processing,
Robotics and Automation, ISPRA Conf., 2009, pp. 103
– 120.
Ivanescu, M., Florescu, M. C., Popescu, N., Popescu,
D.,2008, Position and Force Control of the Grasping
Function for a Hyperredundant Arm, Proc. of IEEE
Int. Conf. on Rob. and Aut., Pasadena, California,
2008, pp. 2599-2604.
Ivanescu, M., Bizdoaca, N., Florescu, M., Popescu,N.,
Popescu, D.,2010, Frequency Criteria for the Grasping
Control of a Hyper-redundant Robot, Proc.of IEEE
International Conference on Robotics and
Automation, Anchorage, Alaska (ICRA 2010), May 3
– 8, 2010, pp. 1542-1549.
Ivanescu , M., D. Cojocaru, N. Bizdoaca, M. Florescu, N.
Popescu, D. Popescu, S. Dumitru,2010, “Boundary
control by boundary observer for hyper-redundant
robots”, Int. Journal of Computers, Communications
and Control, 2010, pp. 755 – 767.
G. La Spina, M. Sfakiotakis, D. Tsakiris, A. Memciassi, P.
Dario,2007, Polychaete-Like Undulatory Robotic
Locomotion in Unstructured Substrates, IEEE Trans
on Robotics, vol 23,No 6,Febr 2007, pp1200-1212
KeJun Ning, F.Worgotter, 2009, A Novel Concept for
Building a Hyper-Redundant Chain Robot, IEEE
Trans on Robotics, vol 25,No 6,Dec 2009, pp 1237-
1248.
Rucker, D. C., B. A. Jones, R. J. Webster III,2010, A
Geometrically Exact Model for Externally Loaded
Concentric-Tube Continuum Robots, IEEE Trans on
Robotics, vol 26,No 5,Oct 2010, pp769-780.
Bailly,Y., Y. Amirat, G. Fried, Modeling and Control of a
Continuum Style Microrobot for Endovascular
Surgery, IEEE Trans on Robotics, vol 27,No 5,Oct
201, pp 1024-1030.
AHybridControlSystemforaTentacleArm
55