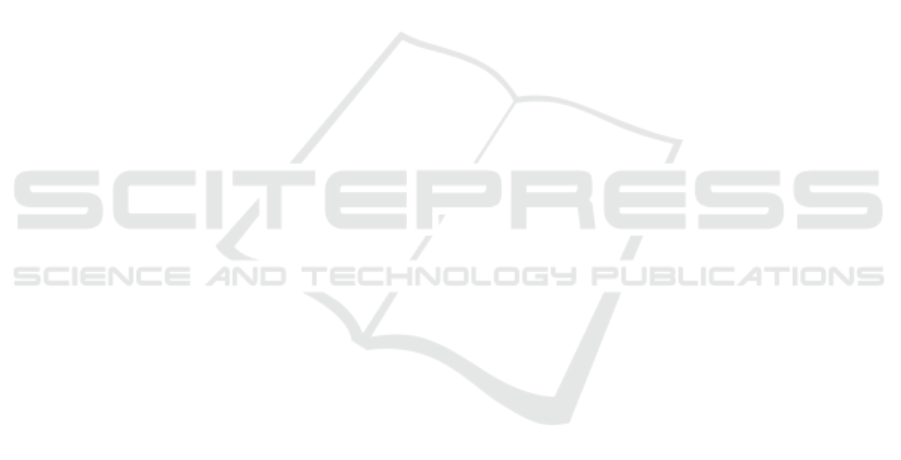
A Computerized System, the FANDAS Code, for Design, Flow,
Performance and Noise Predicitions of Industrial Axial FAN
Chan Lee and Hyun Gwon Kil
Department of Mechanical Engineering, University of Suwon, Hwaseong, Korea
Keywords: FANDAS, CFX, Design, Analysis, Optimization, Performance, Noise.
Abstract: FANDAS (FAN Design and Analysis System) code is developed for the design, the performance and the
noise predictions of industrial axial fan. In the FANDAS code, the 3-D geometrical designs for impeller
blades and casing of fan are made through blade angle distribution, camber line determination and blade
airfoil thickness distribution processes along blade span height, and their results are shown in GUI( Graphic
User Interface ) window. Based on the design fan geometry, the FANDAS code automatically predicts the
flow field inside fan and the overall performance map of fan by using flow deviation and pressure loss
models. The noise level and spectrum of designed fan are also evaluated by the FANDAS code which
contains noise analysis models for discrete frequency and broadband noise components of axial fan. All the
performance and the noise prediction results are displayed on GUI windows. The simulation technique of
the FANDAS code is coupled with the CFX code and applied to an actual air-conditioning fan design
practice for optimizing design variables to maximize efficiency and minimize overall noise level of fan. The
optimal fan design obtained from the FANDAS simulation results shows about 10% efficiency
improvement and 11dB noise reduction compared with the commercial market product of a reference
model, and its simulation results are well-agreed with the measurement within a few percent relative error.
1 INTRODUCTION
Axial flow fans are widely used rotating machines in
industrial, ventilation and air-conditioning systems.
However, air-born noise of the axial flow fan is strongly
related with the aerodynamic flow field and the
performance of fan, so the noise control and reduction of
fan must be attempted with the consideration of the
interaction between aerodynamic and acoustic
characteristics. For this reason, the actual fan design
practice in industry calls for reliable analysis method for
predicting both performance and noise level. With the
recent advances in computational fluid dynamics and aero-
acoustic methods, the flow, the performance and the noise
predictions have been being attempted by many previous
researchers (Belamri et al., 2005; Carolus et al., 2007).
However, because their methods are based on
computational fluid dynamics techniques so have still
shortcomings requiring a lot of input data, complicated
modeling work, long computing time and skillful
engineer’s experience for successful iterative computation,
they still remain as analysis tools and can’t be applied to
the actual design stage of axial fan.
Therefore, the present study introduces a simpler and
less time consuming fan design-analysis method,
FANDAS( FAN Design and Analysis System ), for design
and performance/ noise predictions. The fan design
process of FANDAS gives 3-D rotor and stator blade
geometries from fan design requirements and
specification, and can transfer them to CFD code.
FANDAS also analyzes the internal flow field and the
performance of designed fan by combining quasi-3D
inviscid computation scheme, flow deviation and pressure
loss models. With the predicted fan flow field and
performance data, FANDAS predicts the discrete
frequency fan noise at blade passing frequency and its
harmonics due to rotating steady aerodynamic lift and
blade by secondary and tip leakage flows. Broadband
noise of fan is predicted with the use of the correlation
model expressed in terms of the performance parameters.
The present study applies the FANDAS method
coupled with CFX code to optimize actual air conditioning
fan. Through the parametric study by FANDAS, optimal
fan design variables are firstly determined for high
efficiency and low noise, and more optimized fan
geometry is achieved by the 3-D CFD simulation of CFX
code. Furthermore, the FANDAS prediction results are
compared with measured results to verify the reliability
and the prediction accuracy of FANDAS.
331
Lee C. and Gwon Kil H..
A Computerized System, the FANDAS Code, for Design, Flow, Performance and Noise Predicitions of Industrial Axial FAN .
DOI: 10.5220/0004403303310336
In Proceedings of the 3rd International Conference on Simulation and Modeling Methodologies, Technologies and Applications (SIMULTECH-2013),
pages 331-336
ISBN: 978-989-8565-69-3
Copyright
c
2013 SCITEPRESS (Science and Technology Publications, Lda.)