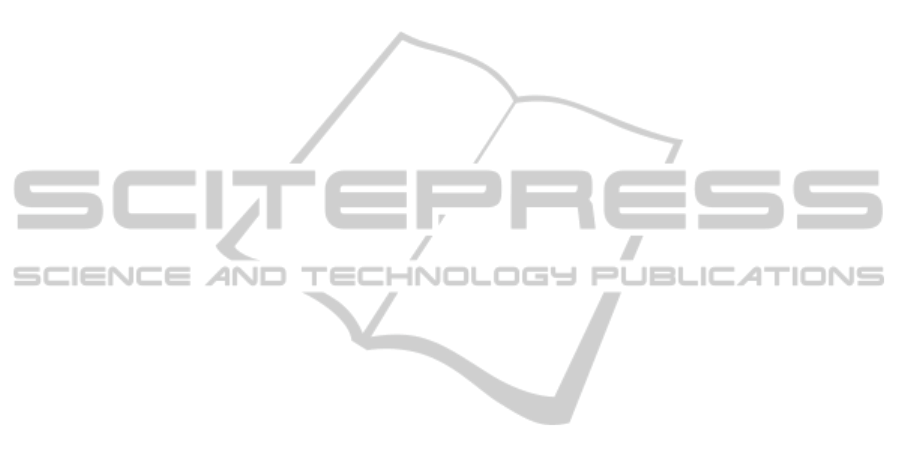
6 CONCLUSIONS
This paper proposes new SMC method with the in-
tegral action for EV traction control. The method
can improve the robust performance of EV traction
by controlling the slip ratio with low energy con-
sumption against the variation of mass of vehicle and
road conditions. We can verified that the the pro-
posed method shows good robust performance with
low energy consumption by comparing to conven-
tional method.
As future works, in this paper, the gain K
i
of in-
tegral action added in the sliding function was deter-
mined by trial and error, so it is necessary to develop
a systematic method to find the optimal value of K
i
.
Moreover, this paper was limited to showing the re-
sults with some example conditions using a simpli-
fied one wheel model, but to make the method practi-
cal, for a variety of road conditions and mass of vehi-
cle must be verified for more detailed two-wheel and
four-wheel models. In addition, the suitability of the
proposed method must be studied not only for the slip
suppression addressed by this paper but also for over-
all driving including during braking.
Even for this issue, however, the basic framework
of the proposed method can be used as is and can also
be extended relatively easily to form a foundation for
making practical high performed robust traction con-
trol systems with low energy consumption for EVs by
promoting further progress.
ACKNOWLEDGEMENTS
This research was partially supported by Grant-
in-Aid for Scientific Research (C) (Grant number:
24560538; Tohru Kawabe; 2012-2014) from the Min-
istry of Education, Culture, Sports, Science and Tech-
nology of Japan.
REFERENCES
Brown, S., Pyke, D. and Steenhof, P., 2010. Electric ve-
hicles: The role and importance of standards in an
emerging market, Energy Policy, Vol.38, Issue 7, pp.
3797–3806.
Mousazadeh, H., Keyhani, A., Mobli, H., Bardi, U., Lom-
bardi, G. and Asmar, T., 2009. Environmental assess-
ment of RAMseS multipurpose electric vehicle com-
pared to a conventional combustion engine vehicle,
Journal of Cleaner Production, Vol.17, Issue 9, pp.
781–790.
Hirota, T., Ueda, M. and Futami, T., 2011. Activities of
Electric Vehicls and Prospect for Future Mobility,
Journal of The Society of Instrument and Control En-
ginnering , Vol.50, pp. 165–170 (in Japanese).
Kondo, K., 2011. Technological Overview of Electric Ve-
hicle Traction, Journal of The Society of Instrument
and Control Enginnering (in Japanese), Vol.50, pp.
171–177.
Zanten, A. T., Erhardt, R. and Pfaff, G., 1995. VDC; The
Vehicle Dynamics Control System of Bosch, Proc. So-
ciety of Automotive Engineers International Congress
and Exposition 1995, Paper No. 950759.
Kin, K., Yano, O. and Urabe, H., 2001. Enhancements
in Vehicle Stability and Steerability with VSA, Proc.
JSME TRANSLOG 2001, pp.407–410 (in Japanese).
Sawase, K., Ushiroda, Y. and Miura, T., 2006. Left-Right
Torque Vectoring Technology as the Core of Super All
Wheel Control (S-AWC), Mitsubishi Motors Techni-
cal Review , No.18, pp.18–24 (in Japanese).
Kodama, K., Li, L. and Hori, H., 2004. Skid Prevention for
EVs based on the Emulation of Torque Characteristics
of Separately-wound DC Motor, Proc. The 8th IEEE
International Workshop on Advanced Motion Control
, VT-04-12, pp.75–80.
Mubin, M., Ouchi, S., Anabuki, M. and Hirata, H., 2006.
Drive Control of an Electric Vehicle by a Non-linear
Controller, IEEJ Transactions on Industry Applica-
tions , Vol.126, No.3, pp.300–308 (in Japanese).
Fujii, K. and Fujimoto, H., 2007. Slip ratio control based
on wheel control without detection of vehicle speed
for electric vehicle, IEEJ Technical Meeting Record,
VT-07-05, pp.27–32 (in Japanese).
Hori, Y., 2000. Simulation of MFC-Based Adhesion Con-
trol of 4WD Electric Vehicle, IEEJ Record of In-
dustrial Measurement and Control , IIC-00-12 (in
Japanese).
Kawabe, T., Kogure, Y., Nakamura, K., Morikawa, K. and
Arikawa, Y., 2011. Traction Control of Electric Vehi-
cle by Model Predictive PID Controller, Transaction
of JSME Series C, Vol. 77, No. 781, pp. 3375–3385
(in Japanese).
J. J. E. Slotine, J. J. E. and Li, W., 1991. Applied Nonlinear
Control, Prentice-Hall.
Eker, I., and AKinal, A., 2008. Sliding Mode Control with
Integral Augmented Sliding Surface: Design and Ex-
perimental Application to an Electromechanical sys-
tem, Electrical Engineering, Vol. 90, pp. 189–197.
H. B. Pacejka, H. B. and Bakker, E., 1991. The Magic For-
mula Tyre Model, Vehicle system dynamics, Vol.21,
pp.1–18.
ICINCO2013-10thInternationalConferenceonInformaticsinControl,AutomationandRobotics
18