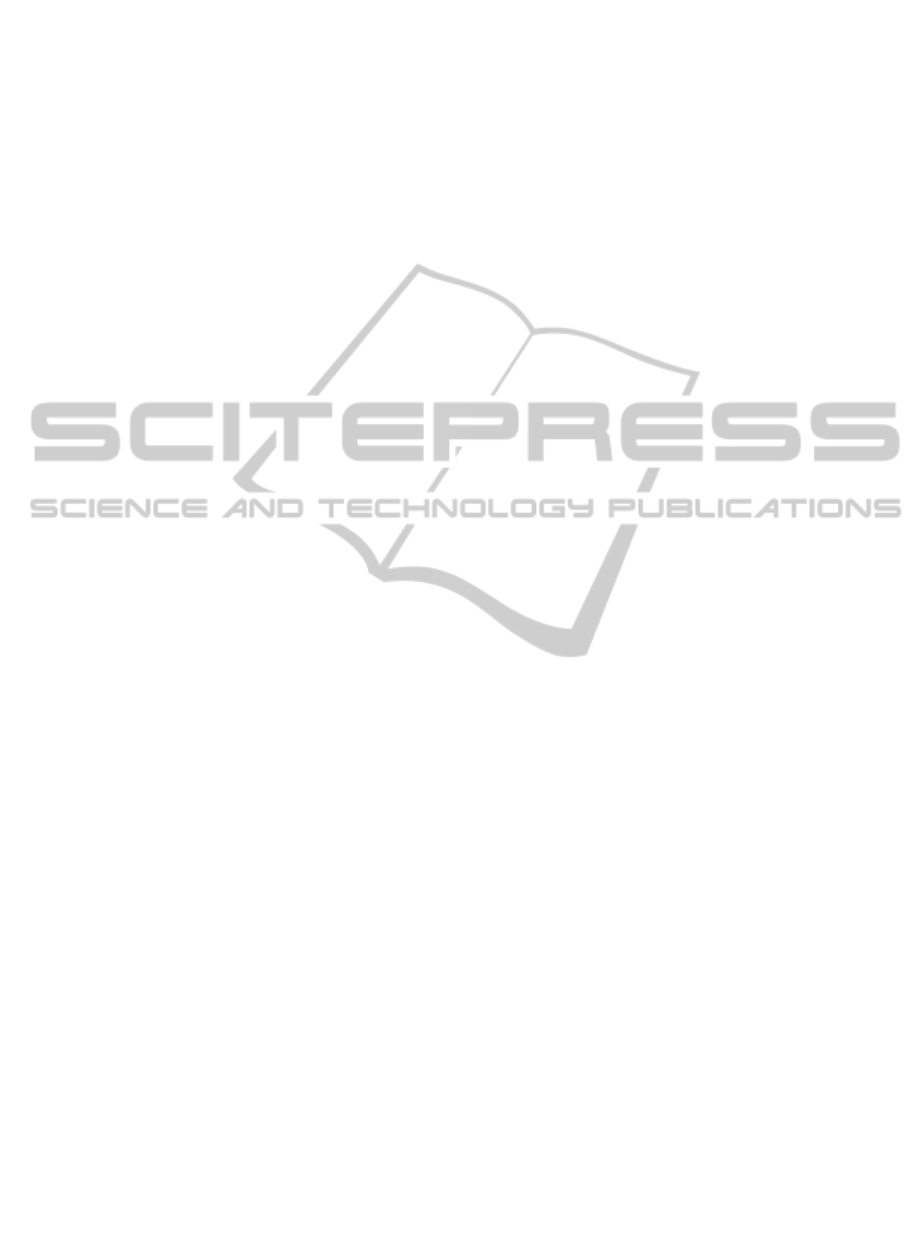
based on the analysis of the client’s requirements
and his tacit knowledge. Thus, experienced and
skilled human resources, i.e., MH (Man-Hour), are
required for accurate cost estimation. Those
resources, however, are limited for any contractor.
For these reasons, it is important to realize
appropriate allocation of MH for cost estimation to
each order to maximize the profits under the
constraints on the volume of total MH. In addition,
contractors should consider the possibility of
realizing a loss due to cost estimation error and a
competitive relationship with bidders. For example,
the bidding price needs to be cut to some extent to
accept the order successfully under a severe
competitive environment; however, a low bidding
price would reduce profit, or even worse, would
create a large loss. Moreover, just a few deficit
orders would result in the significant reduction of
realized profits when the number of accepted orders
is limited. (Note, in this paper, that we refer to the
order creating an eventual loss as a deficit order.)
In this paper, we develop a two-step bidding
price decision algorithm in consideration of the cost
estimation accuracy and the deficit order probability
under limited MH in EPC projects. The algorithm
assumes that the costs are estimated at the same time
for all orders. At the first step, the algorithm
allocates MH for cost estimation to each order
according to the ranking of orders under the
constraints on the volume of total MH. The MH
allocation determines the cost estimation accuracy of
each order. At the second step, it determines the
bidding price for maximizing the expected profit
under the deficit order probability constraint.
We develop a mathematical model for simulating
competitive bidding. Through the numerical results
obtained by using this model, we show that the
bidding price decision in consideration of the cost
estimation accuracy and the deficit order probability
is essential for the contractor to make a stable profit
in EPC projects, and that our two-step bidding price
decision algorithm is effective for making such
bidding price decisions.
2 RELATED WORK
Among the research related to the bidding price
decision, there are order acceptance and project
selection problems.
Order acceptance is basically the problem of
making a decision to accept each order or not in
Make-To-Order (MTO) manufacturing (Kolisch,
2001), and its objective is to maximize profits with
capacity limitations. As literature surveys done by
Slotnick and Morton (2007), Herbots et al. (2007),
and Rom and Slotnick (2009) have shown, there
exists a variety of related research topics. Project
selection, on the other hand, is the problem of
creating a mix of projects from candidate projects to
help achieve an organization’s goals within its
resource constraints. Research and development
(R&D), information technology, and capital
budgeting are typical application fields of the project
selection. Researchers have applied various kinds of
methods to these problems (Dey, 2006; Medaglia et
al., 2007; Wang et al., 2009).
Most of the literature dealing with the order
acceptance and the project selection problems has
assumed that the contractor can select orders or
projects according to the contractor’s own criteria
and by the contractor’s own initiative. In
competitive bidding, however, the contractor
basically offers a bidding price and accepts the order
based on the client’s decision.
A variety of studies, such as bidding theory,
bidding model, and auction design, have been
conducted on competitive bidding (see Ballesteros-
Pérez et al., 2012 for detailed references). In
particular, a number of papers regarding the
competitive bidding strategy date back to Friedman
(1956), who presented a method to determine an
optimal bidding price based on the distribution of
the ratio of the bidding price to cost estimate.
However, little attention has been paid to profit
volatility risk, which cannot be ignored in EPC
projects. When, for instance, the number of accepted
orders is limited, the realized total profit from the
projects might be sharply lower than expected
because the profit is significantly affected by a few
deficit orders. Accordingly, the deficit order
probability should be considered in the bidding price
decision.
In addition to the profit volatility risk, we
consider the allocation of MH for cost estimation to
each order when making a decision on the bidding
because certain MH is necessary to estimate cost
accurately in EPC projects. Several papers have
analysed the problem of allocating scarce resources
in competitive bidding (see Rothkopf and Harstad,
1994 for detailed references). Among them,
Kortanek et al. (1973) considered sequential bidding
models where the obtained contracts require the use
of restricted resources, such as production capacity,
at the time of actual production. Ishii et al. (2012)
develop a mathematical model where bidding prices
are determined in consideration of the MH allocation
for cost estimation to maximize the expected profit
SIMULTECH2013-3rdInternationalConferenceonSimulationandModelingMethodologies,Technologiesand
Applications
394