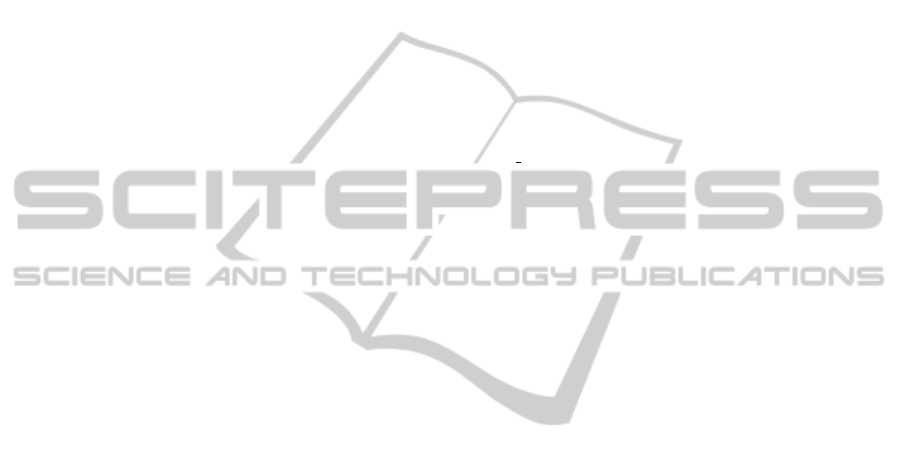
mand is larger than the power delivered, the battery
discharges. This is verified in the acceleration phase
and also during the power cut, in order to support the
minimum speed.
Figure 6d represents the distance traveled by the
train during simulation. By comparing these graphics
with the speed profile shown in 6a it is possible to see
that the model is consistent.
Accounting for a time schedule was implemented
by feeding the Petri net model with a timing signal
from the external environment. A simulation was
performed where the train is required to travel 1 km
within a maximum time of 360 s. The results are
shown in Figure 7.
Figure 7a shows the minimum velocity required
in order to reach the target within the maximum time
given. A higher velocity is allowed as long as the pan-
els are able to sustain it. Through Figure 7b it is pos-
sible to see that until time 100 the panels are able to
sustain a higher velocity, which causes the minimum
velocity value to decrease as time passes. From that
time instant forward the panels stop delivering power,
which causes the train to assume the value of mini-
mum velocity, in order to reach the target in time. The
train travels at this velocity until it stops at the target
within the defined schedule.
7 CONCLUSIONS
This paper describes a simulation tool to assess the
viability of the Helianto solar train project.
The whole infrastructure was modeled as a dis-
crete events system (DES), represented by Petri nets,
and a supervisory controller was designed for the
whole system. Two key toolboxes were used for these
purposes, respectively, QSS and Netlab. The perfor-
mance of the train is analyzed for multiple scenarios
and evaluated based on energy consumption, travel
time and speed achieved.
Simulations are performed on two different sce-
narios. The first scenario refers to a situation where an
obstacle is detected on the track and the second refers
to a power cut during travel. Temporal constraints
such as the ones introduced by time schedules are also
accounted for. The results were consistent, showing
that the velocity achieved by the train allowed the mo-
tion to be maintained by the panels alone, resorting to
battery only during acceleration phase, where a power
peak demand occurs, or when a power failure occurs
in order to sustain minimum velocity.
The results obtained show consistency in the sense
that the train behaves as realistically expected and the
energy consumption was effectively managed. More-
over, taking advantage of the flexibility of the Mat-
lab/Simulink environment the overall tool is suitable
for hardware-in-the-loop experiments.
ACKNOWLEDGEMENTS
This work was partially supported by FCT project
PEst-OE/EEI/LA0009/2011.
REFERENCES
State of California Energy Commission and California Pub-
lic Utilities Commission (2013). Go Solar Califor-
nia. http://www.gosolarcalifornia.ca.gov/equipment/
pv modules.php. Accessed January 2013.
Andr
´
e, J. (2006). Transporte Interurbano em Portugal, vol-
ume 2. IST Press. Lisbon (in Portuguese).
Bogdan, S., Lewis, F., Kovacic, Z., and Meireles Jr, J.
(2006). Manufacturing Systems Control Design: A
Matrix Based Approach. Springer.
Davidrajuh, R. (2008). Developing a New Petri Net Tool
for Simulation of Discrete Event Systems. In Procs.
2nd Asis Int. Conf. on Modeling and Simulation.
G. Cassandras, C. and Lafortune, S. (2008). Introduction to
Discrete Event Systems. Springer.
Godoy Simaes, M., Franceschetti, N., and Adamowski, J.
(1998). Drive System Control and Energy Manage-
ment of a Solar Powered Electric Vehicle. In Procs. of
the 13th Annual Applied Power Electronics Conf. and
Exposition (APEC’98), volume 1.
Helianto (2013). The Helianto Project. Available at http://
helianto.ist.utl.pt.
Jinrui, N., Fengchun, S., and Qinglian, R. (2006). A Study
of Energy management System of Electric Vehicles.
In Procs. IEEE Vehicle Power and Propulsion Conf
(VPPC’06).
Moody, J., Yamalidou, K., Antsaklis, P., and Lemmon, M.
(1994). Feedback control of Petri nets based on place
invariants. Lake Buena Vista.
Netlab (2008). Petri Net Toolbox: Netlab. Available
at http://www.irt.rwth-aachen.de/en/fuer-studierende/
downloads/petri-net-tool-netlab/.
QSS (2008). QSS-Toolbox. Available at http://
www.idsc.ethz.ch/ Downloads/ qss.
SoDa (2012). SoDa, Solar Radiation Data. http://
www.soda-is.com. Accessed January 2012.
SRoeCo Solar (2013). Most Efficient Solar Panels.
http://sroeco.com/solar/most-efficient-solar-panels.
Accessed January 2013.
SIMULTECH2013-3rdInternationalConferenceonSimulationandModelingMethodologies,Technologiesand
Applications
430