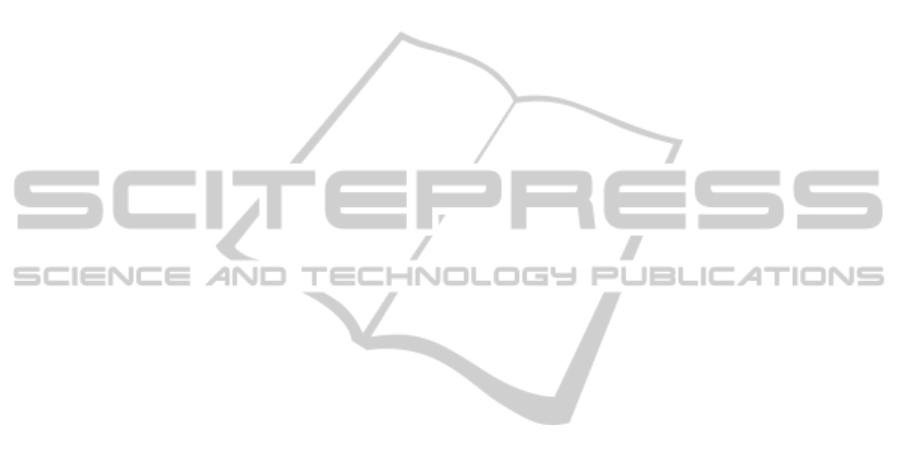
higher hierarchical levels, where it brings the
capability to flexibly coordinate multiple, largely
smart and otherwise autonomous subsystems. This
perfectly reflects fundamental constraints in closed-
loop control, which occurs in numerous instances for
a smart system. Piaget can be effective and
interactive in real-time; easy to operate, configure
program, for the average user; and similarly so for
experts, in case of parallel and distributed
implementation. An industrial case is studied,
involving multiple, otherwise independent,
commercially available subsystems, such as
industrial robot arm, PLC, IP camera or joint
controller. A special, multi-tool end-effector, had to
be designed. Highlight is given of selected software
items, relating to the overall application, to the robot
arm, or to the vision part. Experiments are reported,
addressing three of the most significant process
components. The results show good performance.
Ideally, the system should be equipped with a smart
controlling system such as without programming
language for users (Perrollaz et al., 2012);
(Yoshitake et al., 2013), but for complex
applications this goal seems far away and
approaches like Piaget provide a pragmatic solution
today.
REFERENCES
Ando, N., Suehiro, T., Kitagaki, K., Kotoku, T. and Yoon,
W-K. (2005). RT-middleware: Distributed Component
Middleware for RT (Robot Technology). In
Proceedings of 2005 IEEE/RSJ International
Conference on Intelligent Robots and Systems, Alberta,
Canada, Aug. 2005, pp. 3933-3938.
Calvo, I., Perez, F., de Albeniz, O.G. and Etxeberria-
Agiriano, I. (2011). Towards a OMG DDS
communication backbone for factory automation
applications. In Proceedings of 2011 IEEE 16th
Conference on Emerging Technologies & Factory
Autom., Toulouse, France, pp. 1-4.
Dessimoz, J.-D. (2010). Elements of Hybrid Control in
Autonomous Systems and Cognitics. Research and
Education in Robotics - EUROBOT 2010,
International Conference, Rapperswil-Jona,
Switzerland, pp.30-45.
Dessimoz, J.-D. (2011). Cognitics - Definitions and
metrics for cognitive sciences and thinking machines.
Roboptics Editions, Cheseaux-Noréaz, Switzerland,
January 2011, ISBN 978-2-9700629-1-2, pp169.
Dessimoz, J.-D., Gauthey, P.-F. and Omori, H. (2012).
Piaget Environment for the Development and
Intelligent Control of Mobile, Cooperative Agents and
Industrial Robots. In Proceedings of the International
Symposium on Robotics, Taipei, Taiwan, Aug.28-31,
2012.
García, H., Salazar, A. and Orozco, Á. (2012). Statistical
Models for Emotion Recognition using Facial
Expression Analysis. In Proceedings of the 9th
International Conference on Informatics in Control,
Automation and Robotics, Rome, Italy, July, 2012, pp.
238-243.
Konidaris G. et al., Org, (2012) Designing Intelligent
Robots: Reintegrating AI, AAAI Spring Symposium
2012, March 26th-28th, Stanford University.
Liu, Z.-T., Mu, Z., Chen, L.-F., Le, P. Q., Fatichah, C.,
Tang, Y.-K., Tangel M. L., Yan F., K. Ohnishi,
Yamaguchi M., Y. Adachi, Lu, J.-J., Li, T.-Y.,
Yamazaki, Y., Dong, F.-Y. and Hirota, K. (2012).
Emotion Recognition of Violin Music based on
Strings Music Theory for Mascot Robot System. In
Proceedings of the 9th International Conference on
Informatics in Control, Automation and Robotics,
Rome, Italy, July, 2012, pp. 5-14
Maier A., Tack, T. and Niggemann, O. (2012). Visual
Anomaly Detection in Production Plants, In
Proceedings of the 9th International Conference on
Informatics in Control, Automation and Robotics,
Rome, Italy, July, 2012, pp. 67-75.
Mizukawa, M., Sakakibara, S. and Otera, N. (2004).
Implementation and applications of open data network
interface 'ORiN', In Proceedings of SICE 2004 Annual
Conference, Sapporo, Japan, Aug. 2004, vol.2, pp.
1340-1343.
Perrollaz, M., Khorbotly, S., Cool, A., Yoder, J.-D. and
Baumgartner E. (2012). Teachless teach-repeat:
Toward Vision-based Programming of Industrial
Robots. In Proceedings of International Conference
on Robotics and Automation, Saint Paul, MN, USA,
May, 2012, pp. 409-414.
Quigley, M., Gerkey, B., Conley, K., Faust, J., Foote, T.,
Leibs, J., Berger, E., Wheeler, R. and Ng, A. (2009).
ROS: an open-source Robot Operating System. In
Proceedings of Open-Source Software Workshop of
the International Conference on Robotics and
Automation, Kobe, Japan.
Quigley, M. and Jackson, J. (2007). Microsoft robotics
studio: A technical introduction. Robotics &
Automation Magazine, vol.14, no.4, pp.82-87.
Son, M., and Yi, M.-J. (2010). A study on OPC
specifications: Perspective and challenges. In
Proceedings of International Forum on Strategic
Technology, Ulsan, Korea, Oct. 2010, pp.193-197.
Tsai, M.-S., Yen, C.-L. and Yau, H.-T. (2012).
Development of Robust Learning Control and
Application to Motion Control. In Proceedings of the
9th International Conference on Informatics in
Control, Automation and Robotics, Rome, Italy, July,
2012, pp. 148-152.
Yoshitake, S., Nagata, F., Otsuka, A., Watanabe, K. and
Habib, M. K. (2013). Development of CAM system
based on industrial robotic servo controller without
using robot language. Journal of Robotics and
Computer Integrated Manufacturing, Vol. 29, Issue 2,
April 2013, pp. 454 – 462.
PiagetfortheSmartControlofComplexRobotizedApplicationsinIndustry
535