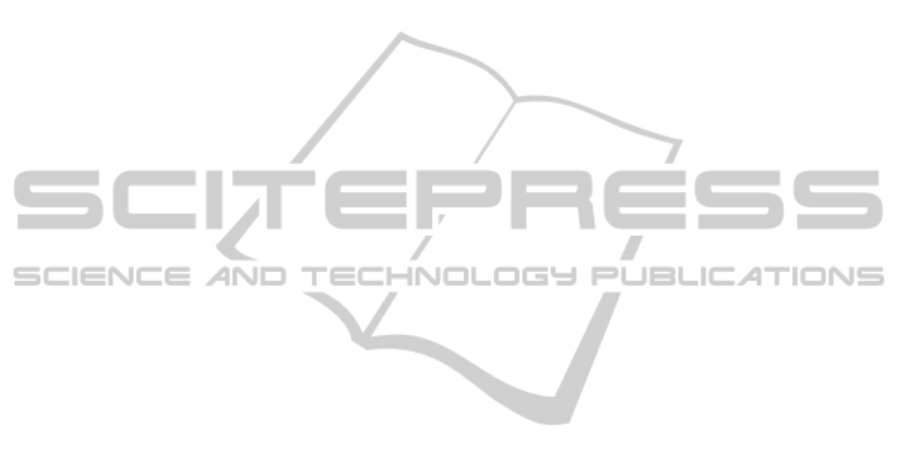
SYMBOLS USED
C
1ε
[-] model constant
C
2ε
[-] model constant
C
[-] model constant
g [m·s
-2
] acceleration of
gravity
G
k
[kg · m
-1
· s
-1
] production of
turbulent kinetic
energy
k [m
2
·s
-2
] turbulent kinetic
energy
M
f
[-] mal-distribution
factor
n [-] number of sample
points
P [Pa] pressure
ΔP [Pa] pressure drop
t [s] time
U [m·s
-1
] interstitial velocity
U
i
[m·s
-1
] local velocity
U
0
[m·s
-1
] superficial velocity
w [mm] width of the annular
channel
Greek symbols
ε [m
2
·s
-3
] turbulent energy
dissipation
ρ [kg·m
3
] density
μ [kg·m
-1
·s
-1
] viscosity
μ
[kg·m
-1
·s
-1
] turbulent viscosity
μ
io
[-] split ratio
σ
[-] model constant
σ
[-] model constant
Ф [mm] diameter
Subscripts
i, j coordinate index
in inlet
out outlet
REFERENCES
Cai, T. J., Chen, G. X., Fitz, C. W. & Kunesh, J. G. 2003.
Effect Of Bed Length And Vapour Maldistribution On
Structured Packing Performance. Chemical
Engineering Research & Design, 81, 85-93.
Dhotre, M. T. & Joshi, J. B. 2007. Design Of A Gas
Distributor: Three-Dimensional Cfd Simulation Of A
Coupled System Consisting Of A Gas Chamber And
A Bubble Column. Chemical Engineering Journal,
125, 149-163.
Fan, L., Chen, G., Constanzo, S. & Lee, A. 1997.
Hydraulic Performance Of Gas Feed Distribution
Devices. Icheme Symp Ser.
Fitz, C. W., King, D. W. & Kunesh, J. G. 1999. Controlled
Liquid Maldistribution Studies On Structured Packing.
Chemical Engineering Research & Design, 77, 482-
486.
Haghshenasfard, M., Zivdar, M., Rahimi, R. & Esfahany,
M. N. 2007. Cfd Simulation Of Gas Distribution
Performance Of Gas Inlet Systems In Packed
Columns. Chemical Engineering & Technology, 30,
1176-1180.
Lockett, M. J. & Billingham, J. F. 2003. The Effect Of
Maldistribution On Separation In Packed Distillation
Columns. Chemical Engineering Research & Design,
81, 131-135.
Mohammadkhah, A. & Mostoufi, N. 2009. Effect Of
Geometry Of The Plenum Chamber On Gas
Distribution In A Fluidized Bed. Industrial &
Engineering Chemistry Research, 48, 7624-7630.
Olujic, Z., Ali, A. M. & Jansens, P. J. 2003a. Effect Of
The Initial Gas Maldistribution On The Pressure Drop
Of Structured Packings. Chemical Engineering And
Processing, 43, 465-476.
Olujic, Z., Kaibel, B., Jansen, H., Rietfort, T., Zich, E. &
Frey, G. 2003b. Distillation Column
Internals/Configurations For Process Intensification.
Chemical And Biochemical Engineering Quarterly,
17, 301-309.
Petrova, T., Semkov, K. & Dodev, C. 2003. Mathematical
Modeling Of Gas Distribution In Packed Columns.
Chemical Engineering And Processing, 42, 931-937.
Stoter, F., Olujić, Ž. & De Graauw, J. 1993. Modelling
And Measurement Of Gas Flow Distribution In
Corrugated Sheet Structured Packings. The Chemical
Engineering Journal And The Biochemical
Engineering Journal.
Tu, J., Yeoh, G. H. & Liu, C. 2008. Computational Fluid
Dynamics -A Practical Approach, Amsterdam,
Elsevier Inc.
Versteeg, H. K. & Malalasekera, W. 1995.
An
Introduction To Computational Fluid Dynamics: The
Finite Volume Method, New York, Wiley.
Wehrli, M., Hirschberg, S. & Schweizer, R. 2003.
Influence Of Vapour Feed Design On The Flow
Distribution Below Packings. Chemical Engineering
Research & Design, 81, 116-121.
Zhang, L. H., Zhou, H. Y., Li, X. G. & Du, Y. P. 2004.
Cfd Analysis Of Gas Distributor In Packed Column -
Prediction Of Gas Flow And Effect Of Tower
Internals Geometry Structure. Transactions Of Tianjin
University, 10, 270-274.
CFDSimulationofaLarge-diameterCombinedGasDistributor
437