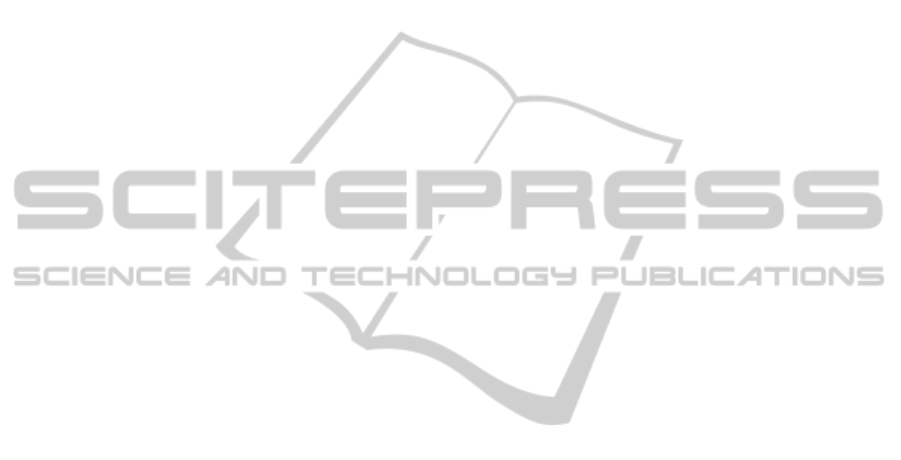
sustainable and reverse supply chains and with a
special emphasis on the remanufacturing case. In the
third section, we propose a new mathematical model
and prove that the convex-hull associated with the
linear relaxation of this formulation is contained in
the convex-hull of the classical formulation. In the
fourth section, we present experimental results for
large sets of data that were generated randomly. The
last section contains conclusions and directions for
future research.
2 LITERATURE REVIEW
In the last few years, mathematical modeling and
solution methods for the efficient management of
return flows (and/or integrated with forward flows)
has been studied in the context of reverse logistics,
closed-loop supply chains, and sustainable supply
chains. The problem of locating facilities and
allocating customers is not new to the operations
research community and covers the key aspects of
supply chain design (Daskin et al., 2005). This
problem is one of “the most comprehensive strategic
decision problems that need to be optimized for
long-term efficient operation of the whole supply
chain” (Altiparmak et al., 2006).
Mathematical models proposed in the literature
for planning reverse logistics networks have been
reviewed by Fleischmann et al., (2000). Fleischmann
et al., (2001) proposed a generic recovery network
model based on the elementary characteristics of
return networks identified in Fleischmann et al.
(2000). Zhou and Wang (2008) proposed a generic
mixed integer model for the design of a reverse
distribution network including repairing and
remanufacturing options simultaneously.
Models for reverse logistics networks in
connection with location problems have been
discussed by Bloemhof-Ruwaard, Salomon, and Van
Wassenhove (1996) and Barros, Dekker, and
Scholten (1998). For example, the last authors
described a network for recycling sand from
construction waste and proposed a two-level
location model to solve the location problem of two
types of intermediate facility.
Regarding remanufacturing location models,
Krikke et al., (1999) described a small reverse
logistics network for the returns, processing, and
recovery of discarded copiers. They presented a
MILP model based on a multi-level uncapacitated
warehouse location model. The model was used to
determine the locations and capacities of the
recovery facilities as well as the transportation links
connecting various locations. In Jayaraman et al.,
(2003), a 0-1 MILP model for a product recall
distribution problem is proposed. They analysed a
particular case in which the customer returns the
product to a retail store and the product is sent to a
refurbishing site which will rework the product or
dispose it properly. The reverse supply chain is
composed of origination, collection, and
refurbishing sites. With the objective to minimize
fixed and distribution costs, the model has to decide
which collection sites and which refurbishing sites to
open, subject to a limit on the number of collection
sites and refurbishing sites that can be opened.
Several authors have studied different aspects of
closed-loop supply chain design problems. See, for
example, Jayaraman et al., (1999), Fleischmann
(2003), Barbosa-povoa et al., (2007); Guide and Van
Wassenhove (2009), and Neto et al., (2010). For
example, Sahyouni et al., (2007) presented three
generic facility location MIP models for the
integrated decision making in the design of forward
and reverse logistics networks. The formulations are
based on the well-known uncapacitated fixed-charge
location model, and they include the location of used
product collection centers and the assignment of
product return flows to these centers. Lu and Bostel
(2007) presented a two-level location problem with
three types of facilities to be located in a reverse
logistics system. They proposed a 0–1 MILP model
which simultaneously considers “forward” and
“reverse” flows and their mutual interactions. The
model has to decide the number and locations of
three different types of facilities: producers,
remanufacturing centers, and intermediate centers.
Reverse logistics models are recently discussed
by Salema et al., (2010); Gomes et al., (2011) and
Alumur et al., (2012). Almost all this research
proposed MILP models. The majority of solution
methods are based on standard commercial
packages.
3 MATHEMATICAL MODEL
In this section a new MILP model for the problem of
designing a remanufacturing and sustainable supply
chain network is proposed. This problem is a single
product, static, three-layer, capacitated location
model with known demands. The remanufacturing
supply chain network consists of three types of
members: sourcing facilities (origination sites such
as a retail store), collection sites (reprocessing
facilities) and remanufacturing facilities. At the
customer layer, there are product demands and used
ANovelMathematicalFormulationfortheStrategicPlanningofaReverseSupplyChainNetwork-Theoreticaland
ComputationalResults
571