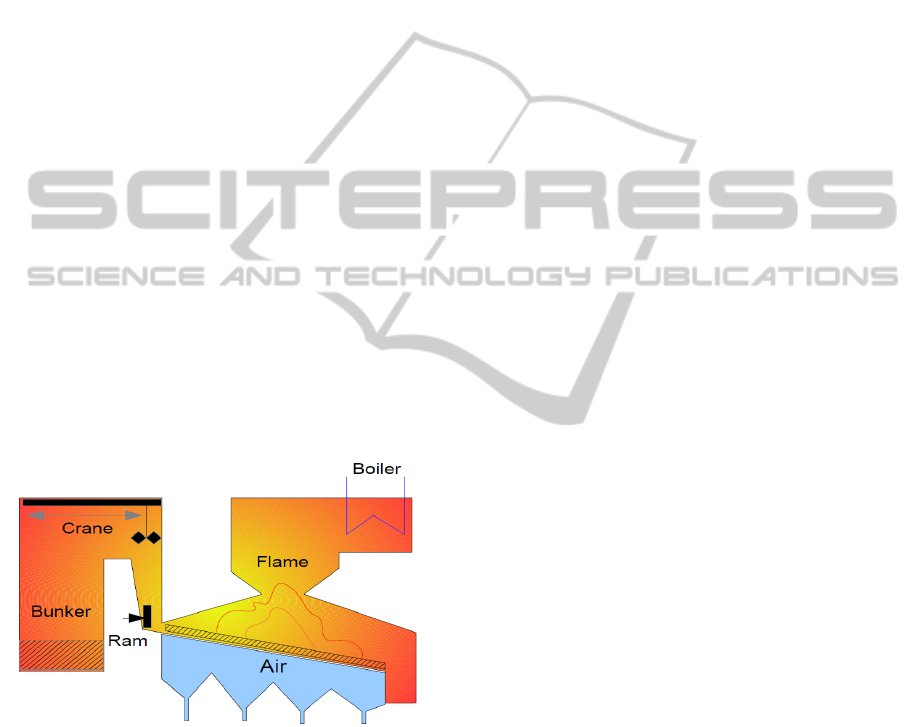
brief description of the plant where the incineration
of the biomass takes place is given followed by an
introduction to the main thermal decomposition
elements which the biomass undergoes in the
moving grate. In Section 3, a mathematical modeling
concept for the process is proposed along with a
brief overview on the control part of the plant.
Section 4 deals with the implementation and the
simulation of a part of the system.
2 PROCESS DESCRIPTION
As already mentioned, an efficient way to convert
biomass into a usable energy is through combustion
that takes place in so called incineration plants. The
biomass or the municipal waste is transported by
means of a truck or a train to the plant where it is
discharged into a storage unit called Bunker.
Consequently, the disposal is gripped and moved to
a large chute where it is thrown (see Figure 1).
At the bottom, the biomass, referred to as fuel, is
fed into the incineration chamber by a horizontally
moving ram and transported through the combustion
chamber by a moving grate. The grate has in
addition a rich oxygen air installation beneath, from
which air is gradually added through existing holes
in order to provide good stoichiometric combustion
conditions inside the chamber.
Figure 1: Incineration plant.
2.2 Biomass Thermal Decomposition
Process
While the biomass is traveling along the combustion
chamber by the moving grate, two main phases can
be distinguished: a solid phase and a gas phase. The
solid phase can be further divided into 4 steps: the
drying, pyrolysis/gasification, char burning, and
finally ash as an end product. In the gas phase, a
secondary air is introduced above the grate in order
to achieve good mixing conditions of the volatiles
and unburned gases released in the previous step, i.e.
the solid phase. The obtained hot gas, referred to as
flue gas, is further transferred to a boiler where the
steam is produced, that can be used as either in
district heating or in electricity production by a
turbine.
2.2.1 Drying
This step is very crucial and can have a strong
influence on the overall behavior of the combustion
in general and the temperature distribution inside the
chamber in particular. Moreover, as the
pyrolysis/gasification, char oxidation and ash take
place at a predefined position on the grate, a biomass
with high moisture content requires a longer time to
be dried. As a consequence, they shift their position
on the grate as reported in (Bauer et al., 2010).
Therefore, it can be concluded that the moisture
content in the biomass is an important variable.
The biomass moisture content evaporates at
temperatures >100 °C. This can be achieved by
radiation at the top of the fuel bed or by heat
conduction through the grate bars. Other plant
suppliers use a pre-heated primary air to speed up
the drying process. Consequently, the evaporated
water is transported by the primary air mass flux to
the upper part of the waste bed. Lastly, it should be
noted that the moist evaporation is an endothermic
process in the sense that it absorbs heat from the
chamber. (Van Loo and Koppejan, 2008) reported
that for a moist content above 60% the flame cannot
be maintained in the combustion chamber.
2.2.2 Pyrolysis/Gasification
After the wet biomass is dried in the previous step,
the temperature in the chamber starts to rise
considerably. As soon as the temperature reaches a
certain level, another thermal degradation of the fuel
takes place, namely the pyrolysis and its associate
the gasification. The pyrolysis occurs under oxygen
deficient conditions and high temperature levels,
which break up the hydrocarbons of the form
CH
x
O
y
N
z
into smaller species such as methane
(CH
4
), carbon monoxide (CO), hydrogen (H
2
),
nitrogen (N
2
), and residual carbon called char.
In contrast to pyrolysis where no oxygen exists
in order to oxidize the gasified hydrocarbons, the
gasification takes place in the presence of a limited
amount of oxygen, i.e. the thermal decomposition is
kept under stoichiometric levels. The product of this
phase is a combustible gas that will be burned in a
ComponentOrientedModelingofBiomassIncinerationPlants
397