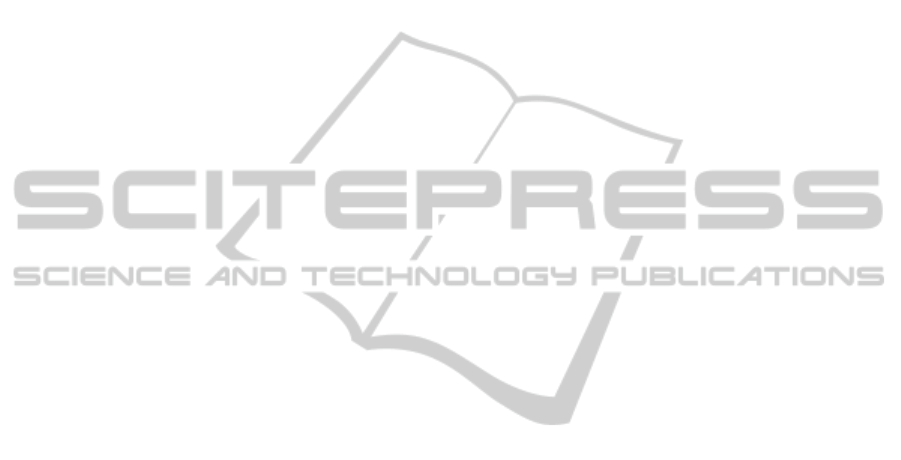
als can be tuned in real-time and at high update rates
to ensure the successful interception of dynamic ob-
jects. A video demonstration of this capture process
can be viewed at http://youtu.be/yTx4a9UAMAM.
This paper describes the following:
• Choosing suitable polynomial trajectories that are
characterized by low-jerk and allow sufficient
flexibility to alter position, velocity and acceler-
ation while preserving continuity at every instant
in time during real-time capture.
• Re-computingthe polynomialtrajectories at every
instant in response to incoming velocity estimates
at a sampling frequency of 200 Hz.
• Reducing jerk during the entire process of inter-
ception, with the additional capability of extend-
ing the same acceleration profile for post-capture
(deceleration).
• Experimental testing and results of the method
during real-time interception of a dynamically
moving object with continuous velocity estima-
tion in the presence of noise.
2 BACKGROUND
During robotic interception and capture, a differ-
ence in velocity at the grasping instant may result
in slippage or impact which can cause damage
to the object or even damage to the manipulator
(Lin et al., 1989). Traditional methods of solving this
velocity matching problem involve predicting the po-
sition of an incoming object and positioning the end
effector at the computed interception point to capture
the object (Borg et al., 2002; Bauml et al., 2010).
Several path-planning techniques exist to achieve this
interception point including the use of polynomi-
als in general as described in (Croft et al., 1998;
Papadopoulos et al., 2005) and cubic splines
in specific (Gasparetto and Zanotto, 2008;
Wang and Horng, 1990). Many of these techniques
use a one-shot design approach for the polynomi-
als, assuming a priori knowledge of the incoming
object such as constant acceleration and velocity
(Campos et al., 2006) and resulting in pre-planned
trajectories for robotic interception. While these
methods are suitable in constrained environments
with repetitive tasks, the velocity of the incoming ob-
ject may change in unconstrained environments. The
capture of such objects presents a challenge due to a
continuously changing predicted interception point.
Additionally, with purely predictive interception
systems, impact and bounce are issues that must be
addressed. High speed robotics (Namiki et al., 2003;
Imai et al., 2004) overcomes the need for prediction
by simply reacting to the changing position estimates
of an object at a very high frequency. However,
no consideration of smoothness or jerk reduction is
possible with such systems.
Several researchers have previously addressed
the need for velocity matching. Nelson et.al.
(Nelson et al., 1995) emphasize in their work the need
for fast and stable transitions from non-contact states
to contact states, with minimum impact and bounce.
An approach where force and vision feedback are
simultaneously used to minimize the impact forces
when a stiff manipulator makes contact with a stiff
surface is presented. In effect, the static surface can
be thought of as having zero velocity and the manip-
ulator is forced to achieve minimum velocity just be-
fore contact. In (Lin et al., 1989), a coarse tuning al-
gorithm which drives the end effector into the neigh-
borhood of the object in minimum time, and a fine
tuning algorithm which ensures zero relative velocity
and acceleration at the time of grasping is presented.
A sensor based system employing the above method
is simulated for a two-degree of freedom (2DOF) pla-
nar robot at a sampling rate of 20 Hz.
The authors of (K¨ovecses et al., 1999) describe
the equations of the robotic end effector and object
independently before the interception phase. Ac-
cording to the authors, the dynamics are dependent
on the velocities and angular velocities at the in-
stant of contact. It is proved that when these com-
ponents are zero, there are no impulsive forces act-
ing on the system, resulting in a smooth capture.
(Zhang and Buehler, 1994) define a smooth grasp as
one in which the position, velocity and acceleration
of the robot end effector matches that of the moving
object at the point of contact.
While trying to achieve a certain end effector ve-
locity, it is important to be able to control its trajec-
tory. A trajectory defines the position, velocity and
accelerations of the end effector in its task space coor-
dinates. Confining the trajectory of the end effector to
be in line with the path of the object can significantly
help minimize the mismatch in velocities between the
two. Commonly used trajectories such as a linear tra-
jectory, with parabolic blends are subject to high jerk,
due to sudden changes in acceleration. The also re-
quire the application of an instantaneous change in
force by the actuator which is not practical. Other
methods of trajectory generation include third- and
fifth-order polynomials that describe the end effector
path in joint space; fifth-order polynomials have the
added advantage that they ensure low jerk values.
A third-order spline interpolation based trajectory
planning method to minimize the instantaneous ve-
locity change during bipedal robot foot contact is pro-
ICINCO2013-10thInternationalConferenceonInformaticsinControl,AutomationandRobotics
418